Polyvinyl chloride (PVC) is a strong, durable plastics material. It mixes easily with lubricants, fillers, and colorings to make plastics with many different properties. There are two basic types of PVC plastics—rigid and flexible. Products made of rigid PVC plastic include bottles, pipes, siding, and window sashes. Flexible PVC plastic products include rainwear, shower curtains, garden hoses, and electrical insulation. Many people refer to PVC simply as vinyl.
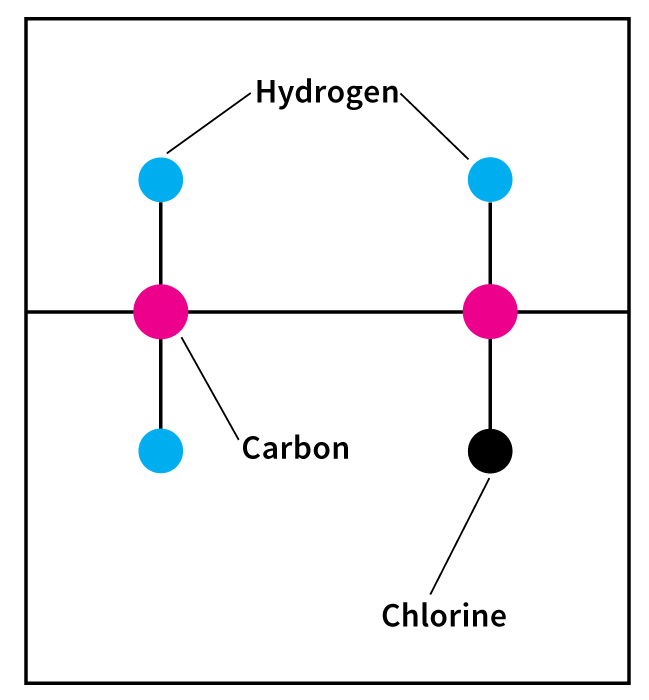
PVC is a synthetic polymer. A polymer is a long, chainlike molecule. The “links” are repeating patterns of simple groups of atoms called monomers. PVC is made from vinyl chloride monomers, each consisting of two carbon atoms, three hydrogen atoms, and one chlorine atom. PVC is a thermoplastic—that is, it softens and melts at high temperatures (see Plastics (Types of plastics) ).
The most common method of making PVC is suspension polymerization. In this process, vinyl chloride monomer—a gas—is fed into water under pressure. There, the monomers link up to form the polymer.
Manufacturers make PVC plastic products by extrusion (pushing melted plastic through an opening), injection molding (forcing it into a mold), and calendering (pressing it between rollers to form sheets).
Vinyl chloride can also form many copolymers, polymers made up of more than one monomer. The most important of these contains vinyl chloride and vinyl acetate. This copolymer is used for floor tiles.
Because PVC plastics contain many ingredients, they are difficult to recycle. However, recyclers commonly grind them into powders that are used as fillers.
The first PVC became available in the late 1920’s. Production accelerated during World War II (1939-1945), when PVC was used in synthetic rubber and in insulation for electric wires and cables.
See also Phthalates .