Propeller is a device for producing motion that has blades mounted on a power-driven shaft. A propeller changes an engine’s power into forward thrust. The best-known types of propellers are those that drive airplanes and ships.
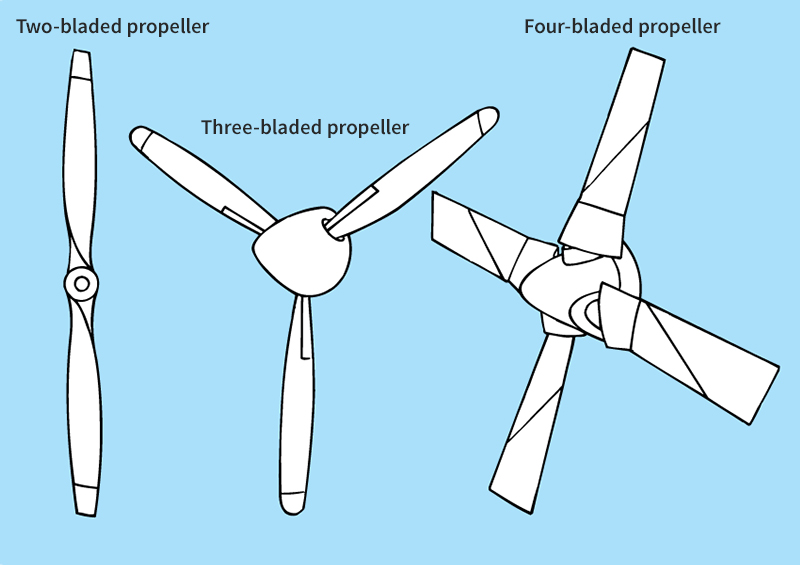
The first screw propeller was developed by the American inventor John Fitch in 1796. His propeller was in the form of a spiral around a cylindrical rod. John Ericsson, a Swedish-American inventor, developed the first successful propeller with blades in 1836 (see Ericsson, John ). Modern propeller design is based in large part on theories developed by the Wright brothers, the American aviation pioneers.
Airplane propellers
are also known as airscrews. They have two or more blades. The cross sections of the blades are airfoils similar to those used in airplane wings—that is, they have aerodynamic shapes designed to provide lift. The pitch is the angle between the cross section of the blade and the plane (flat surface) in which the propeller rotates. Propeller blades are twisted, and so the pitch changes along the length of the blade. As a result, each section of the propeller blade meets the air at the angle that results in the most efficient generation of thrust. The efficiency of a propeller decreases and the noise it makes increases rapidly as the speed of the tips of its blades exceeds the speed of sound.
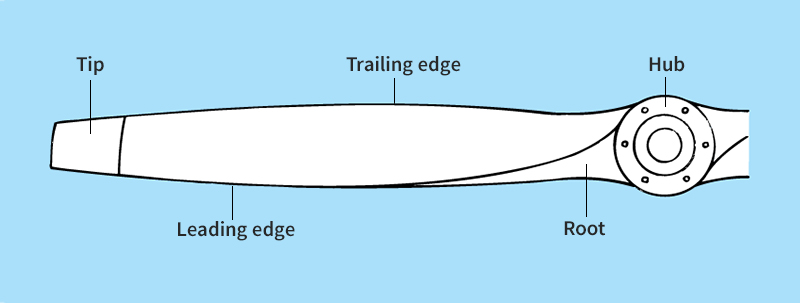
A fixed-pitch propeller
is one in which the blades are set at a fixed angle. Such propellers are efficient only at one speed of flight and for a specific power output. They usually are used on small aircraft.
A constant-speed propeller
has variable pitch. The angle of the blades adjusts continuously to provide the most efficient operation at every flight speed. The propeller automatically turns the same number of revolutions per minute under all conditions of flight. It does not gain speed in dives or lose speed in climbs.
Many constant-speed propellers have special features that are used in emergency situations. For example, a feathering device enables the pilot to increase the blade angle enough to streamline the blades with the engine stopped. In case of an engine failure, the pilot can feather, or rotate, the blades to prevent windmilling. In windmilling, aerodynamic forces act on the blades, causing the propeller to turn. This action can cause significant damage to the engine and the airplane.
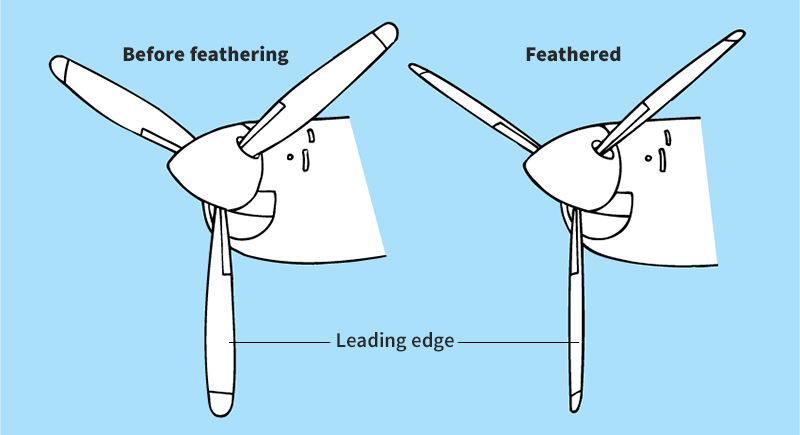
Another feature of many constant-speed propellers is reversible-pitch. On such propellers, the blades can be set at a negative pitch so that the direction of the thrust is reversed. This acts as a brake and reduces the landing run on the ground. Reversible-pitch is of great value for large airplanes, particularly when runways are covered with ice or snow, making the wheel brakes ineffective.
Ship propellers,
also called marine propellers, range in diameter from 10 inches (25 centimeters) for small boats to more than 25 feet (7.5 meters) for large tankers. They are usually made of manganese and bronze.
Battleships and large tankers may have propellers with five or six blades, while smaller ships use three- or four-bladed propellers. Propellers on single-screw ships turn to the right, or clockwise, when viewed from the stern when the ship is going ahead. Twin-screw vessels usually have counter-rotating propellers. To move the ship ahead, the starboard screw—the one on the right when facing the bow—turns clockwise, and the port screw, the one on the left, turns counterclockwise. Twin-screw ships are easily steered by reversing one of the engines while the other goes full ahead. Destroyers and other small craft can make sharp turns in this way. Conventional propellers are less effective at high speeds because of cavitation, the formation of a vacuum on the side of the blade that does not push against the water. A propeller called a supercavitating propeller is designed so that cavitation increases its effectiveness at high speeds.
See also Aerodynamics (Lift) ; Airplane (Propellers) ; Ducted propeller ; Screw ; Ship (Engine-driven ships ) (The first propeller-driven ships) .