Refrigeration is the process of removing heat. For thousands of years, people have used some kind of refrigeration to cool beverages and preserve food. Since the mid-1800’s, refrigeration has been widely used to keep food from spoiling. Today, food is stored in home refrigerators and freezers. Grocery stores and supermarkets use refrigerated display cases, freezing rooms, and cold-storage warehouses. Frozen and fresh produce is carried locally in delivery vans and long distances in refrigerated trucks and containers. Industry uses refrigeration in the processing of chemicals, lubricants, rubber, and steel.
Refrigeration has many uses besides preserving food. Air conditioning depends on refrigeration to cool the interiors of all types of buildings: homes, offices, theaters, and stores. It also cools passenger transport, including automobiles, trains, and airplane cabins. Computers generate heat, so cooling at data centers is essential for the electronic communications necessary for business and social networks. Hospitals require close climate control in many areas used for storage of serums, vaccines, blood plasma, and other lifesaving medical supplies. Drug companies use refrigeration to make penicillin and other drugs. Florists refrigerate cut flowers to preserve their fresh appearance. Drinking fountains supply cold water. Ice machines provide blocks, cubes, flakes, and chips of ice. Ice plants and skating rinks use refrigerating machines to manufacture ice. Refrigeration is also used in producing frozen fruit juices, candy, ice cream, and many other products.
Additionally, refrigeration technology is now becoming widely applied in providing useful heat by means of heat pumps. Heat pumps can help conserve energy. Refrigeration, air conditioning, and heat pump equipment consumes 25 to 30 percent of the world’s electricity. However, the refrigeration industry’s power use goes largely unnoticed by conservationists.
Principles of refrigeration
Refrigeration removes heat from solids, liquids, and gases. Removal of heat requires the presence of a colder substance because, according to the second law of thermodynamics, heat flows only from warmer bodies to colder bodies (see Thermodynamics). For example, hot cocoa becomes cooler and slightly heats the surrounding air. It will never increase in temperature unless the surrounding air is hotter. Heat cannot go from a colder substance to a warmer substance on its own accord. During refrigeration, heat transfer occurs when we place the substance we wish to cool near a refrigerant (cooling agent).
Heat transfer.
The flow of heat from warmer bodies to colder bodies is called heat transfer. Heat transfer will always occur at a rate that depends on the temperature difference between the bodies and on the resistance of the bodies to the flow of heat. Resistance is commonly called insulation.
A simple type of refrigeration occurs when we cool a warm bottle of water in a running stream. The stream’s water acts as a refrigerant. It absorbs heat and slightly rises in temperature as it flows over the bottle, which cools.
Effects of heat transfer.
Heat transfer can produce several effects. It can both cool the warmer body and warm the body that absorbs the heat. Heat transfer may also change the physical state of a substance. For example, removing sufficient heat may cause a gas to change to a liquid. This process is called condensation. The reverse of condensation is vaporization or evaporation (the process of a liquid changing to a gas). A gas loses heat when it condenses, but it does not change in temperature. Likewise, a liquid absorbs heat when it vaporizes. The temperature at which a substance condenses or vaporizes at a given pressure is its boiling point. Boiling points increase as pressure rises. Removing enough heat from a liquid causes it to freeze (become solid). The temperature at which a substance freezes is called its freezing point. The reverse of freezing is melting. Melting is the process of changing a solid to a liquid. Liquids lose heat when they freeze. Solids gain heat when they melt. The heat gained or lost during a change of state is called latent heat. The heat gained or lost during temperature change is called sensible heat. See Heat [Changes in state].
Ice refrigeration
Ice is one of the oldest methods of refrigeration. The Chinese cut and stored ice as long ago as 1000 B.C. Ice makes a useful refrigerant because it always maintains the same temperature—its constant melting temperature of 32 °F (0 °C). Ice absorbs large quantities of heat as it changes into water.
Iceboxes work because warm air rises. A block of ice in the upper part of an icebox absorbs heat from the warm air. This cools the warm air and increases its density. The colder, heavier air flows downward to the food compartments. The air becomes warmer and lighter as it absorbs heat from the food. The warmer, lighter air rises and again loses heat to the ice.
Ice can be enhanced by endothermic reactions, in which chemical reactions absorb heat from the atmosphere. By itself, ice could never absorb enough heat to reduce the temperature of a substance below its own melting point of 32 °F (0 °C). But endothermic reactions enable ice to further reduce the temperature of a substance. Certain chemical compounds, particularly salts, produce a cooling effect when mixed with ice or snow. These chemical combinations are called endothermic mixtures. Such compounds as calcium chloride, sodium chloride, and ammonium nitrate form endothermic mixtures when mixed with ice or snow. These mixtures create a chemical reaction that absorbs heat. This allows more heat to be transferred from the substance to the mixture, so the substance can be cooled to a lower temperature than could be reached with ice alone. Adding sodium chloride can lower the melting point of ice to about –15 °F (–9 °C). Some mixtures can produce even lower temperatures. See Salt, Chemical.
Homemade ice cream production is an example of the use of endothermic mixtures. Ice cream begins to freeze at about 28 °F (–2 °C). The ingredients for homemade ice cream are cooled by mixing them in a container that is surrounded by crushed ice and salt. The endothermic reaction of the ice and salt absorbs latent heat from the ingredients, causing them to freeze.
Using chemicals to reduce temperature is not new. About 1550, people in Italy found that a mixture of potassium nitrate (saltpeter) and water could be used to cool bottled liquors.
Dry ice is solid carbon dioxide. As a refrigerant, it has two important advantages over ice made from water. Like water ice, dry ice undergoes change at a constant temperature. But instead of changing to a liquid, dry ice sublimes (vaporizes) directly to a gas (see Sublimation). For this reason, boxes containing food packed in dry ice do not leak fluid as they would if the food was packed in water ice. This characteristic gives dry ice its name.
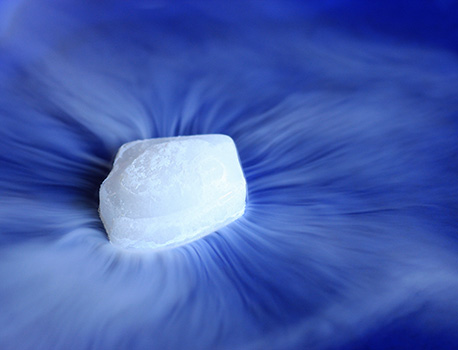
Dry ice sublimes at –109.3 °F (–78.5 °C). That temperature is much lower than the melting temperature of water ice. As a result, dry ice produces much lower temperatures than water ice. Food processing companies find dry ice valuable for keeping foods and ice cream frozen. Dry ice must be handled carefully, however. It can cause frostbite and severe burnlike injuries. See Dry ice.
Mechanical refrigeration
The first mechanical refrigeration systems used air as a refrigerant. The air refrigeration cycle works when air is compressed and then has heat removed from it. The air is then allowed to expand, which reduces its temperature to below the temperature it had before it was compressed. With its pressure reduced, the air is ready to be compressed again, and the cycle can be repeated (see Gas [Gas laws]). Early mechanical refrigeration systems were pioneered by J & E Hall, a company in England. The effectiveness of J & E Hall’s cold air machinery was demonstrated when one of the first cargoes of frozen meat was successfully shipped from the Falkland Islands to England in 1886.
Today, air refrigeration is commonly used for cooling aircraft cabins. Heavy and costly air cycle machines, however, were replaced when more compact and cheaper vapor compression cycle systems became available for aircraft. The vapor compression cycle makes use of a refrigerant that exists as both liquid and gas at convenient temperatures and pressures.
The electric refrigerator.
Most modern household refrigerators utilize the vapor compression cycle. Gas at a low pressure and low temperature enters the compressor, where it is compressed. The compressor is powered by an electric motor. The compression raises the temperature of the gas. The heated gas is then transferred to a condenser (the coils behind the refrigerator), where heat is released into the surrounding air. Vent fins help heat transfer by increasing the contact area with the surrounding air. Because the gas is now at high pressure, condensation occurs. As the gas condenses into a liquid, it goes through an expansion device where its pressure is suddenly lowered. When the liquid’s pressure is reduced, its boiling point becomes much lower, and a portion of it vaporizes. This change of state from liquid to gas has a cooling effect. Cooled liquid is then fed through evaporator coils within the refrigerator itself, where it absorbs heat from the air inside. The low-pressure, low-temperature gas that exits the evaporator coils then reenters the compressor, and the cycle begins again.
Non-vapor compression methods.
There are alternatives to vapor compression. The most significant are the absorption system and evaporative cooling.
In the absorption system, the refrigerant is heated directly by gas, steam, or some other heat source instead of by compression. During the 1850’s, Ferdinand Carré, a French engineer, developed the first absorption system.
The gas refrigerator
works on the absorption system. It uses heat energy as a source of power. A gas refrigerator has no moving parts. Its five basic parts are the generator, the separator, the condenser, the evaporator, and the absorber.
In one type of gas refrigerator, ammonia serves as the refrigerant. Heat from a gas flame is applied to the generator, a tank containing a solution of ammonia dissolved in water. The heat causes the solution to boil. Ammonia vapor and some of the solution rise to the separator. The separator removes the liquid. The hot ammonia gas continues its rise to the condenser. In the condenser, it cools and liquefies. Because water has been separated from the ammonia, the liquid is now almost pure ammonia. The liquid ammonia flows through a tube into the evaporator, or freezing unit. There it vaporizes with hydrogen gas. The hydrogen equalizes the pressure between the condenser and the evaporator. The vapor absorbs heat and produces refrigeration. The heavy mixture passes downward into the air-cooled absorber. There the ammonia is absorbed by water. The light hydrogen gas separates from the solution. The hydrogen rises through a pipe above the absorber and returns to the evaporator. The cool ammonia-water solution flows back to the generator.
Gas refrigerators in recreational vehicles (RV’s), campers, and some industrial units use absorption systems. Large absorption systems are frequently used where waste heat is available from an industrial process.
Evaporative refrigeration
can provide air cooling over a limited temperature range from vaporization of water at atmospheric pressure. An example is covering food containers with a damp cloth in warm weather. Evaporative coolers draw air over a wet pad and send the cooled air into a designated space. Sometimes called adiabatic cooling, these systems are simple and inexpensive ways to provide comfort in hot climates. However, the systems are limited in the amount of cooling they provide and dependent on the weather.
Steam-jet refrigeration
systems work on the principle that water vaporizes easily when it is under low pressure. The lower the pressure on the water, the faster the evaporation and the lower the temperature that will be produced.
In such systems, water flows through a chamber with an opening. A high-speed jet of steam passes across the opening. The steam creates suction within the space above the water and lowers the pressure in the chamber. Some of the water evaporates, absorbing heat from the liquid water remaining in the chamber, which can then be circulated to cool other things.
Steam-jet refrigeration has wide use in industrial and shipboard cooling. In addition, many brewers and distillers use this type of mechanical refrigeration.
Very low temperature refrigerators
are called cryogenic refrigerators or cryocoolers. They can produce temperatures as low as –459 °F (–273 °C), near absolute zero. Cryogenic refrigerators have important uses in science and industry. For example, physicians use them to freeze living parts of the body for future use. Manufacturers use them to cool miniature electronic systems. See Cryogenics.
A cryogenic refrigerator uses helium, nitrogen, or another gas as a refrigerant. Typically, it utilizes the Joule-Thomson effect. This effect is the temperature change of a gas when it is forced through a valve or other resistance, from high pressure to low pressure. Several stages may be involved. Helium is used as the refrigerant in the lowest-temperature refrigeration. Helium is the only substance that can remain liquid below –435 °F (–259 °C).
Some new cooling methods are magnetic cooling, thermoelectric cooling, and adsorption systems. They are currently the subject of investigation and research.
Refrigerants.
The first vapor compression cycle applications used carbon dioxide and ammonia as refrigerants. Carl von Linde of Germany patented the first commercially successful compression refrigerator using ammonia in 1876. It suited the larger type of refrigerators in use at the time. But the properties of these refrigerants limited their use. Ammonia is toxic (poisonous), and carbon dioxide must be kept under high pressure. A breakthrough came in the 1930’s when the American chemist Thomas Midgley, Jr., introduced the first chlorofluorocarbon (CFC) refrigerant, known by its trade name, Freon. This refrigerant had a high latent heat, meaning it could absorb much heat, and it could be used at moderate pressures. Freon is nonflammable and nontoxic. It is also inexpensive. As more CFC’s, and similar refrigerants called hydrochlorofluorocarbons (HCFC’s), were developed to suit various temperature ranges, more companies began to produce them.
Around the same time, compressor technology saw the introduction of the first hermetically sealed (gastight) compressors. Small compressors with integral motors suitable for home appliances became available and were manufactured on a large scale. Prior to this, refrigerator compressors were powered by a belt drive and motor. The airtight-sealed unit was much more compact. It also eliminated refrigerant leakage and the maintenance associated with an external drive.
These developments allowed refrigeration and air conditioning to become widespread. Refrigeration applications are typically divided among domestic, commercial, and industrial sectors. The commercial sector includes retail refrigerators, cold rooms, and small cold stores. Larger scale industrial systems are often custom designed and custom built. Up until the 1980’s, chlorine-containing CFC’s and HCFC’s were typically used in household and commercial refrigeration. Ammonia remained desirable as an industrial refrigerant despite safety concerns, due to its low cost and superior performance. Carbon dioxide refrigerants were only used in applications where ammonia could not be safely used.
Refrigeration and the environment
In the mid-1980’s, scientists discovered that CFC’s were damaging the protective ozone layer in Earth’s upper atmosphere. Although these refrigerants were typically used in sealed appliances, inevitable leaks and repairs released CFC gas into the atmosphere. In 1987, an international agreement called the Montreal Protocol went into effect. It provided a global framework to reduce the production and use of CFC’s, ending the use of these chemicals in refrigeration. CFC refrigerants were largely replaced with chemicals called hydrofluorocarbons (HFC’s). These refrigerants do not have chlorine and do not harm the ozone layer of the atmosphere.
However, in the early 1990’s, HFC’s were found to be powerful greenhouse gases. Such gases trap heat in the atmosphere, increasing Earth’s surface temperature. The production and use of such gases are now regulated through international agreements. The agreements restrict the use of HFC’s with the goal of drastically reducing their contribution to global warming.
HFC’s must be replaced with refrigerants that have sufficiently low Global Warming Potential (GWP) to meet the regulations. Ammonia and carbon dioxide refrigerants have been mainly restricted to the industrial sector. Ammonia is considered too dangerous to use in occupied spaces due to its toxicity. Carbon dioxide, which has rarely been used as a refrigerant, is now being applied in some commercial systems. Commercial and home refrigeration systems, and most air conditioning, had previously used only nonflammable refrigerants. Some systems now use flammable propane as a refrigerant. However, safety codes in Europe and the United States now call for refrigerants that have low flammability. The use of hydrofluoroolefins (HFO’s), a new class of refrigerants that are nonflammable and have low GWP, is becoming more widespread.
Carbon emissions.
The refrigeration industry is responsible for a significant percentage of the world’s electricity consumption. A portion of that electricity is generated by burning fossil fuels that contribute to global warming. Powering a refrigeration system contributes more to global warming over the system’s operational lifetime than does any contribution due to the system’s leakage of refrigerant. Therefore, any new refrigeration system must operate more efficiently and consume less electricity to reduce GWP. Good practices in operation and maintenance are also essential if newer refrigeration systems are to deliver the results intended by their designers.