Textile has traditionally meant a woven fabric. The term comes from the Latin word texere, meaning to weave. Today, textile refers to any product that is woven, knitted, braided, or otherwise constructed of fibers. The textile industry also uses the term textiles to mean the fibers themselves. The term fabric is closely related to textile. It generally refers to textiles that are eventually made into consumer products, especially clothing and home furnishings. In popular usage, however, fabric is often used to mean any textile.
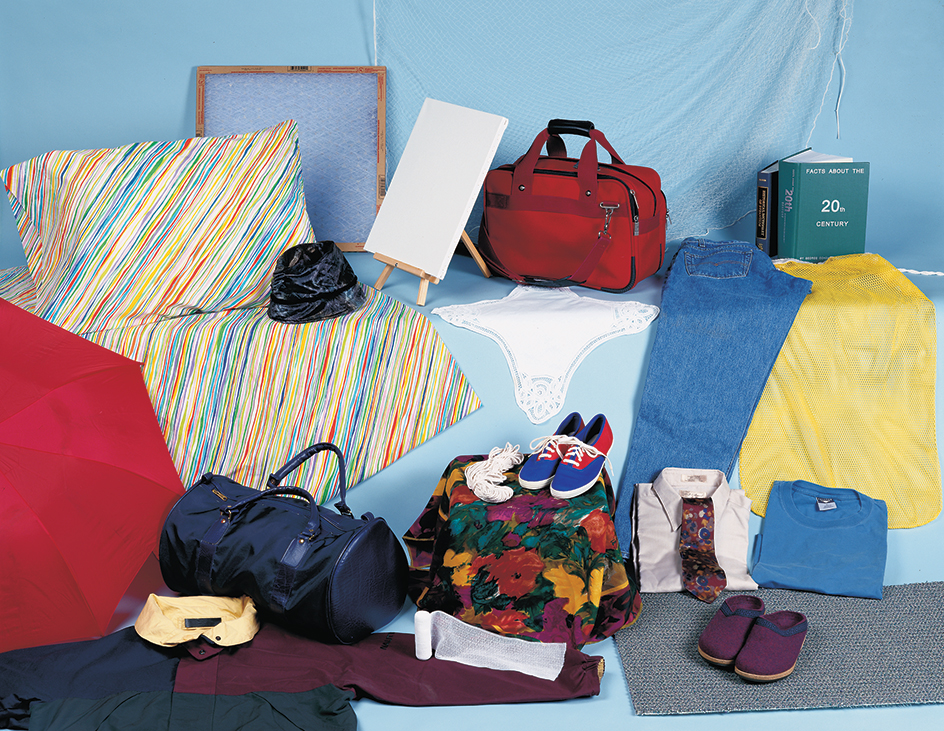
Textile manufacturing plants produce an incredible variety of textiles. Textiles are made from such fibers as acetate, cotton, flax, nylon, polyester, rayon, silk, and wool. These textiles come in every color imaginable and in countless patterns.
Textiles are used in thousands of products. Textile products include basketball nets, boat sails, bookbindings, fire hoses, flags, insulation materials, mailbags, parachutes, and umbrellas. Automobile manufacturers use textiles to make airbags, brake linings, carpeting, seat belts, tires, and upholstery. Hospitals use such textile products as adhesive tape, bandages, and surgical gowns.
Most textiles are produced by twisting fibers into yarns. Then the yarns are knit or woven into a fabric. This method of making cloth has been used for thousands of years. But for most of that time, workers did the twisting, knitting, or weaving largely by hand. With modern machinery, textile manufacturing plants can produce as much fabric in a few seconds as workers could make in weeks by hand.
In the United States, clothing and accessories make up the largest share of textile production. The second largest share is used in industrial products. Such products include conveyor belts and filters. The third largest share goes to rug and carpet manufacturers. The rest is used to make household products. These products include draperies, blankets, sheets, and towels.
Sources of textile fibers
Fibers are the raw materials for all textiles. Some fibers occur in nature as fine strands. The strands can be twisted into yarns. These natural fibers come from plants, animals, and minerals. Most natural fibers used for textile production measure 1/2 to 8 inches (1.3 to 20 centimeters) or longer. Such short fibers are called staple fibers.
For most of history, people had only natural fibers to use in making cloth. But textile scientists have learned how to produce fibers by chemical and technical means. Today, these manufactured fibers account for more than two-thirds of the fibers processed by U.S. textile mills. Unlike most natural fibers, the majority of manufactured fibers are produced in long, continuous lengths. Such lengths are called filaments. Many manufactured fibers are designed to have certain qualities superior to those of natural fibers. For example, they may be stronger or more elastic.
Natural fibers.
Plants provide more textile fibers than do animals or minerals. In fact, one plant, cotton, accounts for the vast majority of the natural fibers used in textiles. Cotton fibers produce soft, absorbent fabrics. They are widely used for clothing, sheets, and towels. Fibers of the flax plant are made into linen. The strength and beauty of linen have made it popular for tablecloths, napkins, handkerchiefs, and clothing. Fibers of the jute plant can be woven into burlap. Burlap is a coarse, heavy cloth. It is used for sacks and as backing for rugs and carpets. Ramie and kenaf are other plant fibers. They can be used for clothing.
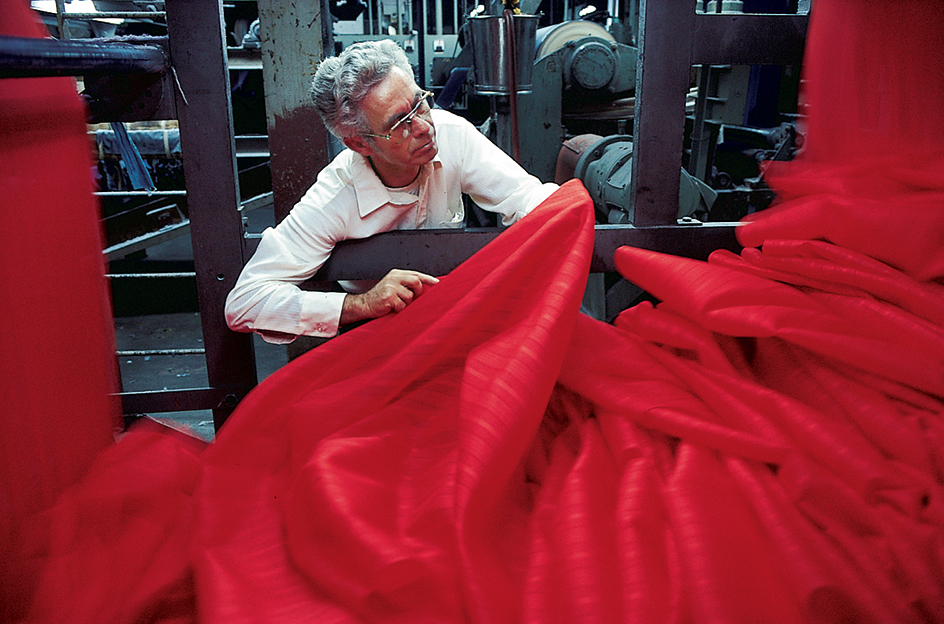
The main animal fiber used for textiles is wool. Sheep supply most of the wool. Members of the camel family and some goats also furnish wool. Wool provides warm, comfortable fabrics. It is used for dresses, pants, suits, and sweaters. Another animal fiber, silk, produces one of the most luxurious fabrics. Silk comes from cocoons spun by silkworms. Workers unwind the cocoons to obtain long, natural filaments. Silk fabrics are soft and lustrous. They can be dyed brilliant colors. Silk is especially popular for scarves and neckties.
The only natural mineral fiber used for textiles is asbestos. Asbestos comes from rocks. It will not burn. But it melts at high temperatures. The use of asbestos to make textiles has been discontinued in many countries. This happened after scientists determined that inhaling the mineral can result in lung disease. But manufacturers in a few countries still use asbestos in automobile brake linings and other products.
Manufactured fibers.
Most manufactured fibers are made from wood pulp, cotton linters, or petrochemicals. Wood pulp comes from trees and the waste products of the lumber industry. Linters are the short fibers remaining on cottonseeds after the longer fibers have been removed. Petrochemicals are chemicals made from crude oil and natural gas.
The fibers made from wood pulp and linters are rayon and acetate. These fibers are called cellulosics because they are made from the cellulose in wood pulp and cotton. Rayon and acetate are used for clothing, draperies, and upholstery. The properties of rayon resemble those of cotton. Rayon produces absorbent fabrics that dye easily. Fabrics of acetate are silkier than those of rayon. Acetate resists shrinking and stretching.
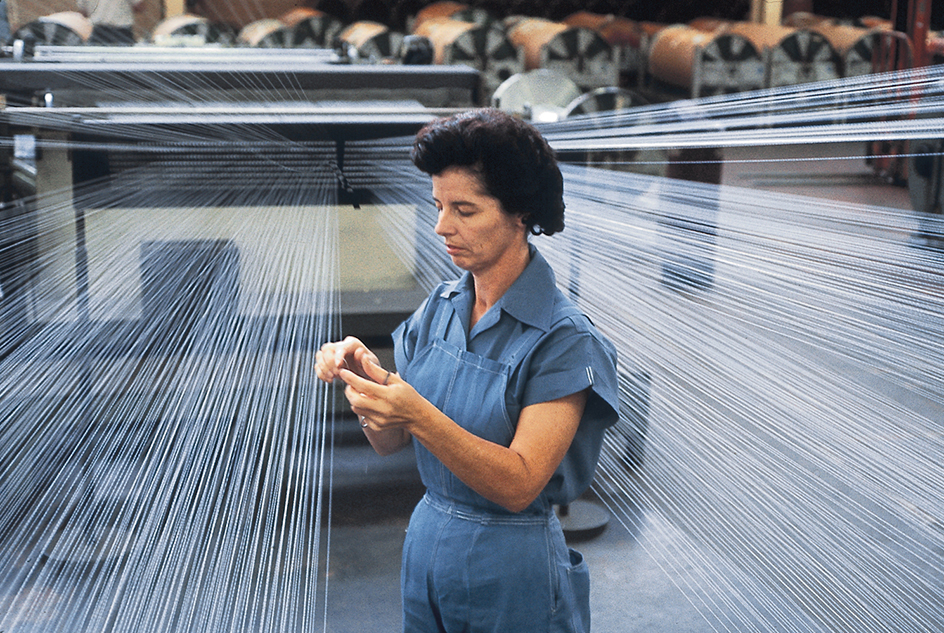
The chief fibers manufactured from petrochemicals include nylon, polyester, acrylic, olefin, and elastomeric fibers. Nylon has exceptional strength. It also wears well. It is easy to launder. Nylon is popular for hosiery and other clothing. It is also popular for carpeting and upholstery. Such products as conveyor belts and fire hoses are also made of nylon. Polyester resists wrinkling. It is widely used in clothing. Acrylic fibers produce soft, bulky, lightweight fabrics. They are used for blankets, carpeting, and cold-weather clothing. Olefin cleans easily and dries quickly. It also resists mildew. It is widely used for indoor-outdoor carpeting. Elastomeric fibers, such as spandex, are often blended with other fibers. This combination provides stretch and comfort in sportswear and other clothing.
Other manufactured fibers include those made from glass and metals. Glass fibers are used for insulation. They are also used to make flame-resistant textiles. Metallic fibers are made chiefly by bonding aluminum, gold, and silver foils to plastics. These fibers provide decorative yarns for bedspreads, evening gowns, and tablecloths.
Kinds of textiles
To make textiles, manufacturing plants may use yarns finer than sewing thread or as heavy as rug yarn. The majority of textiles are made by weaving or knitting.
Woven fabrics
are made of two sets of yarns. A lengthwise set is called the warp. A crosswise set is called the filling or weft. The warp yarns are threaded into a loom through a series of frames called harnesses. During weaving, the harnesses raise some warp yarns. They lower others. This action creates a space, or shed, between the yarns. In traditional looms, a device called a shuttle carries the filling through the shed. The filling yarns form the crosswise yarns of the fabric. In modern weaving machines, called shuttleless looms, the filling yarn is carried from one side to the other by other means. It may be carried by jets of air or water. The pattern in which the harnesses are raised and lowered for each insertion of the filling yarn determines the kind of weave. There are three basic patterns. They are plain weave, twill weave, and satin weave.
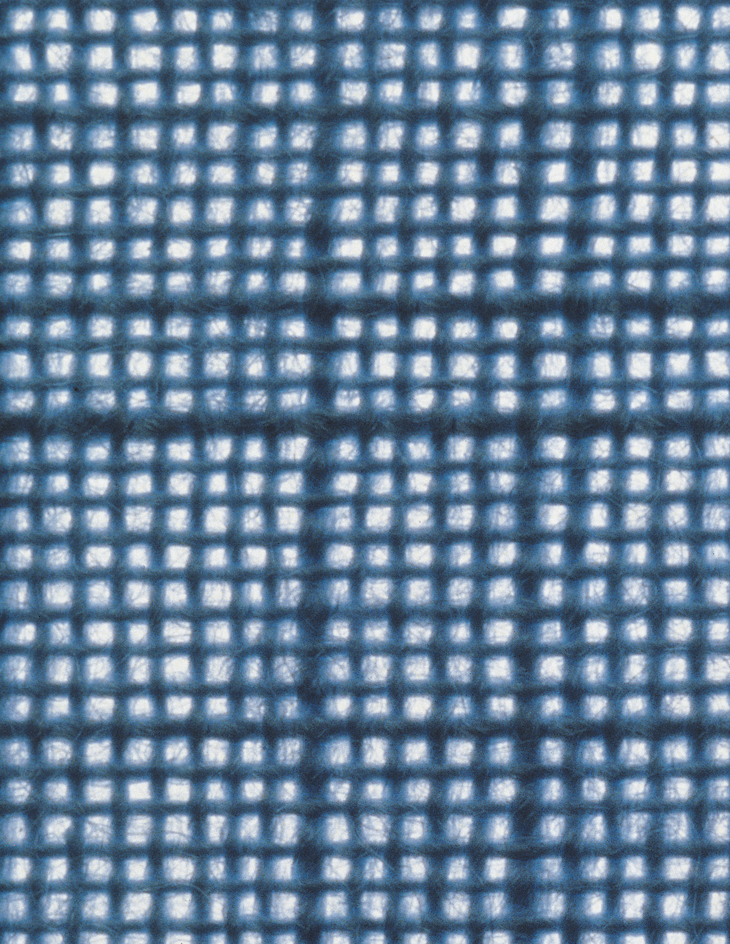
Plain weave
is the simplest and most common pattern. In this weave, the crosswise filling passes over one warp yarn and under the next alternately across the width of the fabric. The weave produces long-lasting, flat-textured fabric. The fabric is used for making such products as bedsheets, dresses, and upholstery. Plain-weave fabrics include gingham, percale, and taffeta.
Twill weave
has a pattern of raised diagonal lines. The filling crosses over and then under two, three, or four warp yarns at a time. Each row follows the same pattern. However, each row’s pattern begins slightly to the right or left of the pattern in the previous row. This technique creates the diagonal lines. The twill weave produces strong, tightly woven cloth. Twill is used in coats, sportswear, and work clothes. Popular twill fabrics include denim and gabardine.
Satin weave
is the least common pattern. The filling may span as many as 12 warp yarns. The weave produces soft, luxurious cloth. But it may snag easily. Satin-weave fabrics are made into such products as draperies and formal clothing. Common satin weaves include damask and satin fabrics.
Knitted fabrics
are made from a single yarn or a set of yarns. In making cloth, a knitting machine forms loops in the yarn. It links them to one another by means of needles. The finished fabric consists of rows of loops. The crosswise rows of loops are called courses. The lengthwise rows of loops are called wales. This looped structure makes knitted fabrics more elastic than woven ones. Garment manufacturers use knitted fabrics to produce comfortable, lightweight clothing. Knitted clothing also resists wrinkling. Textile mills manufacture knit goods by two basic methods. They are weft knitting and warp knitting.
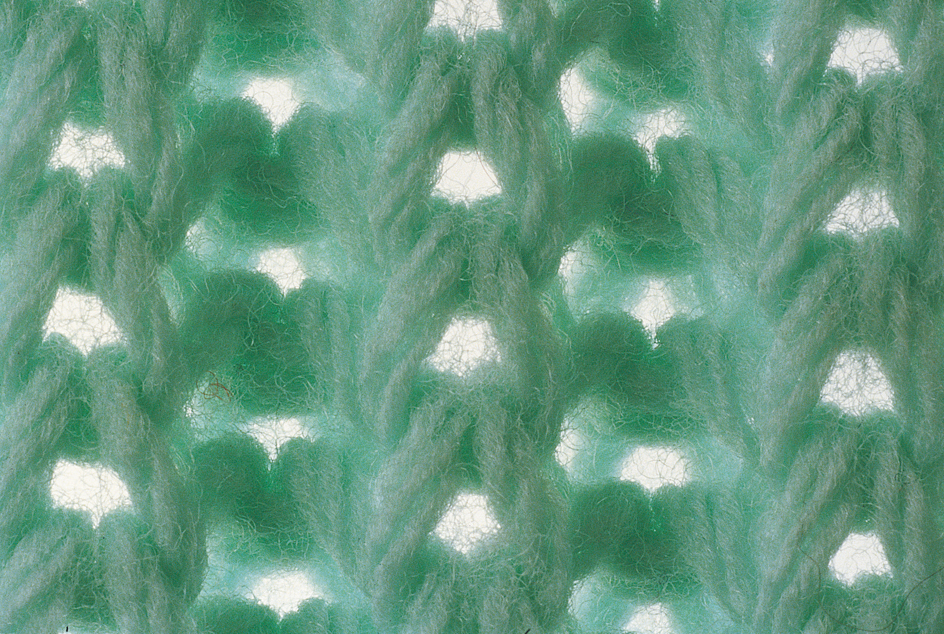
Weft knitting
is done with single lengths of yarn. A knitting machine forms the lengths of yarn into the crosswise courses one row at a time. The loops of each course are pulled through the loops of the previous course. This process forms the wales at the same time as the courses. Weft knits can be made in the shape of a tube or as flat pieces of fabric.
Most weft-knitted fabrics are used in making T-shirts, hosiery, sweaters, and underwear. These fabrics are knitted in three basic constructions. They are known as jersey fabric, rib fabric, and purl fabric. All of them are based on a simple loop. Jersey fabric is sometimes called plain knit or single knit., In this fabric, the long part of the loop forms a V shape over the face of the fabric. The curved, or bottom, part of the loop forms the reverse side. In rib fabrics, the V part of the loop makes up long, vertical raised wales. They alternate with wales consisting only of the curved part of the loop. A kind of rib fabric called double knit is made with smaller, tighter stitches. Double knits are used for sportswear. Lightweight cotton double knits are usually sold as interlock knits. A purl fabric consists of rows in which the V shape alternates with the curved part of the loop.
Warp knitting
requires hundreds of yarns fed as a sheet to a knitting machine. A separate needle for each yarn forms the wales of the fabric. At the same time, the needles interloop the wales crosswise. They thus form the yarns into a fabric. Almost all warp knits are produced in flat pieces.
Warp-knitted fabrics may be tightly constructed. Thus, they may not stretch as much as weft knits. In warp knits, the loops stand out on the face of the cloth. The connecting yarns stand out on the back. Common warp-knitted fabrics include tricot and raschel. Tricot knits are lightweight fabrics. They are widely used in making bedsheets, blouses, dresses, and women’s underwear. Raschel knits can be either finely knitted, lacelike fabrics or heavier, bulkier fabrics. They are used for a variety of products, including blankets, swimwear, and thermal (cold-weather) underwear.
Other textiles
include tufted fabrics, nets and laces, braids and felt. They also include a category of textiles called nonwovens. None of these textiles are woven or knitted.
Tufted textiles
consist of cut or uncut loops of yarn punched through a backing material. Such textiles make up the vast majority of carpeting.
Nets and laces
are also called open-mesh fabrics. They have wide spaces between the yarns. These fabrics can be produced on certain kinds of knitting machines. Netting is used for curtains, fishing nets, hammocks, and tennis nets. Laces have delicate designs. They are popular as trim for clothing.
Braids
consist of three or more interlaced yarns. Braided textiles are used for shoelaces, drawstrings, and similar items.
Felt
is produced chiefly from fibers of wool, fur, or animal hair. The fibers are matted together by moisture, heat, and pressure. Felt is used in making such items as slippers, hats, and padding.
Nonwoven fabrics
consist of one or more sheets of fibers bonded together by any of several methods. The fibers are generally produced in a web (continuous sheet). One bonding method is called chemical bonding. It involves the addition of an adhesive or solvent. In thermal bonding, heat softens some of the fibers. This enables them to fuse to other fibers. A form of mechanical bonding called needlepunching uses hooked needles. The needles create physical tangles among the fibers. Webs may also be stitched together.
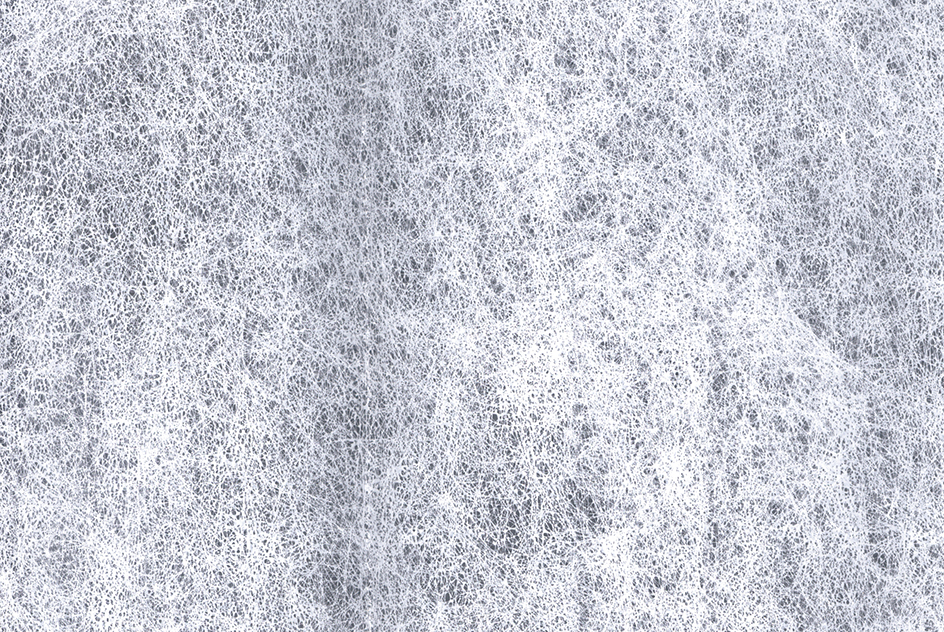
Nonwovens are sometimes classified as either disposable or durable. Disposables are used only once. They are used in such things as disposable diapers and surgical gowns. Durable nonwovens are more versatile than wovens and knits. Typical durable nonwovens include window shades and many blankets and carpets.
Certain nonwovens known as geotextiles help reinforce soil and protect against erosion. These nonwovens may be durable textiles that last for many years. Or they may be biodegradable mats that hold grass or flower seeds in place. The mats gradually break down when the seedlings begin to grow.
How textiles are produced
Designing a fabric.
Most fabric designers work for companies that manufacture fabrics for clothing or other consumer products. Designers create new patterns. They also decide what fibers and methods of construction to use in various fabrics. Fabrics must be designed so that manufacturers can produce them economically on standard textile machinery, such as looms, knitting machines, and tufting machines. A design must also appeal to consumers.
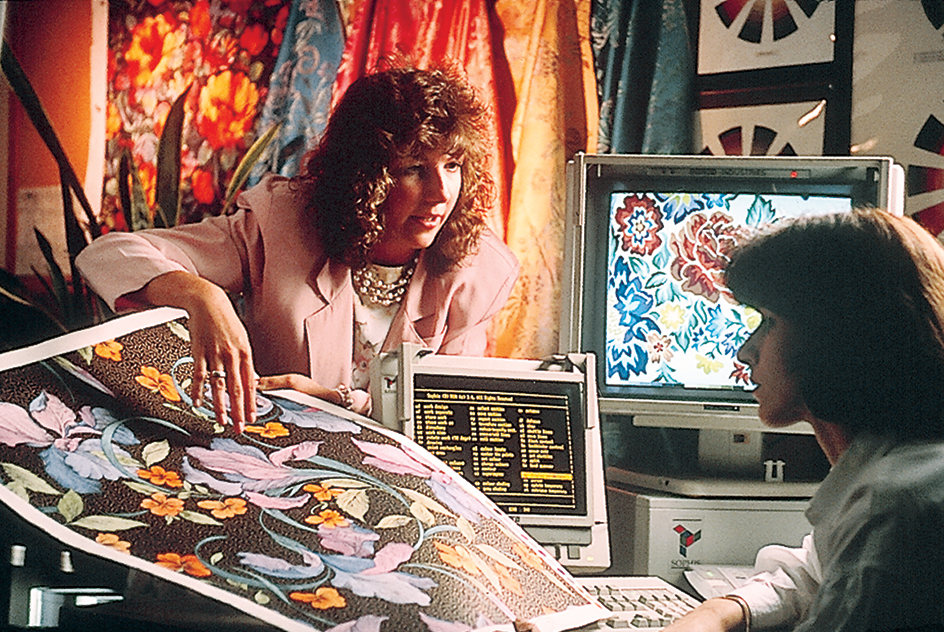
Making the yarn.
Yarn can be manufactured in various ways. Fiber companies may draw together 15 to 100 filaments to make multifilament yarn. Or they may use a single filament to make monofilament yarn. Some filament yarns can be heat-set to form stretch yarns. These include filament yarns made from nylon and polyester. In one method of heat-setting, manufacturers tightly twist the yarn and heat it. After the yarn is untwisted, it tends to snap back like a spring. Such yarn is used in double-knit and stretch-woven fabrics. Other treatments can be applied to filament yarns to give them a bulky texture.
Filaments may also be cut into staple lengths measuring 1 to 3 inches (2.5 to 7.6 centimeters) long. Staple fibers cut from filaments produce yarn that is softer and less lustrous than filament yarn. Yarn producers can also mix together natural fibers and manufactured fibers of staple length. Doing so produces blended yarns. These yarns have the characteristics of each of the fibers used in their construction. For example, yarn produced from cotton and polyester is absorbent because it contains cotton. It is also wrinkle resistant because it contains polyester.
Yarn made from natural fibers or manufactured fibers of staple length is called staple yarn or spun yarn. All staple yarns are manufactured in much the same way. It does not matter whether they are blended or consist of only one kind of fiber. The fibers arrive at the mill in bales. Workers feed the bales into a series of opening machines. These machines break up the large masses of fibers. They also remove some of the impurities. In addition, they mix the fibers together. A carding machine then removes smaller impurities and short fibers. It arranges the remaining fibers into a loose rope. This rope is called a sliver << SLY vuhr >> . Next, as many as eight slivers at a time are drawn together into another sliver. This sliver is then formed into a thin strand called a roving. The roving is twisted on a spinning frame to form yarn. Some spinning frames produce yarn directly from slivers. Different kinds of fibers may be blended when the bales are opened, when the slivers are drawn together, or when the roving is spun.
After the yarn has been manufactured, it is wound onto large spools. Sometimes, two or more strands of yarn are twisted together for added strength. Each strand of such yarn is referred to as a ply. Three-ply yarn, for example, consists of three strands. After the yarn has been spooled, it is ready to be made into fabric.
Making the fabric
begins when workers place the spools of yarn on a rack called a creel. The creel feeds the yarns onto a beam (roller) that is placed on a loom or a knitting machine. For a discussion of how looms and knitting machines make cloth, see the previous section, “Kinds of textiles.”
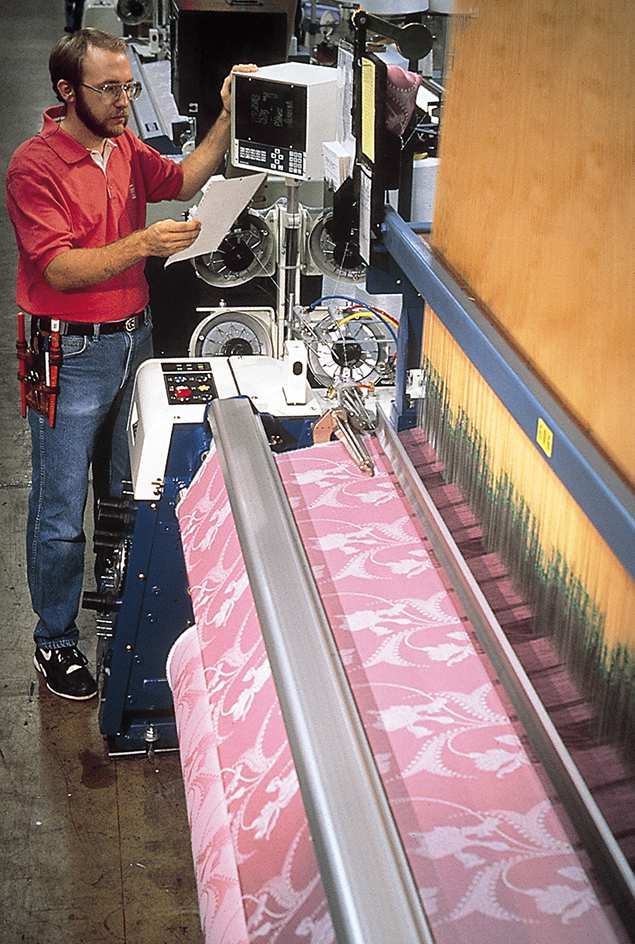
Manufacturers produce fabrics in various lengths and widths. For example, woven fabrics made for clothing manufacturers are usually produced in widths of 36 to 60 inches (91 to 152 centimeters). Most woven narrow goods measure 1/2 to 3 inches (1.3 to 7.6 centimeters) wide. Narrow goods are used for such products as clothing labels and gauze bandages.
A knitting mill usually specializes in one of four kinds of products. They are piece goods, hosiery; underwear; or outerwear. Piece goods are uncut fabric on the bolt. Outerwear includes such garments as dresses, shirts, slacks, and sweaters. Most fabric in widths of 80 to 168 inches (203 to 427 centimeters) is sold to clothing manufacturers. Fabrics made in the shape of tubes are used for the bodies of sport shirts and T-shirts. Such fabric can also be cut and sewed together like flat-knitted fabrics to make garments.
Finishing the fabric.
Fabrics that come directly from a loom or knitting machine are called pronounced greige, << gray >> , goods. This term means that the fabric has not received any finishing treatments. It is thus unsuitable for most purposes.
Almost all greige goods are washed to remove dirt, grease, and other unwanted substances. Many fabrics are also bleached. Bleaching whitens them or prepares them for dyeing or printing. Cotton fabrics may be treated with sodium hydroxide (also called caustic soda, or lye) before dyeing. This process is called mercerization It increases the luster of the fabric. It also makes the fabric stronger. In addition, mercerization enhances the fabric’s ability to hold dye.
Some greige goods are made from dyed yarn. Such cloth may have brilliant colors and highly detailed designs. But most textiles are dyed a single color after the yarn has been made into cloth. Some dyeing machines pull the fabric through a dyebath. Other machines force the dye into the cloth by means of pressure.
Designs are printed on fabrics by any of several methods. Roller printing uses rollers with designs deeply engraved on their surface. Dye is applied to the rollers. Then it is wiped off the surface. The dye that remains in the engraved design is then transferred onto the cloth by the rollers. Screen printing is similar to using a stencil to form a design. Dye is pressed onto the cloth through a pattern on a screen. One common method is called rotary screen printing In it, porous rollers hold the dye. The rollers are covered with cylindrical screens. The rollers force the dye into the fabric through patterns on the screens. Another process is called heat transfer printing. In heat transfer, the design is printed on paper with special ink. Then it is ironed onto the fabric. When the paper is peeled off, it leaves the design on the fabric. Some fabrics are dyed and then printed. In digital inkjet printing, a computer directs tiny nozzles to spray patterns of ink directly on fabrics or onto heat transfers.
After the fabric has been dyed or printed, it may be dried and stretched on a machine called a tenter frame. Fabrics made from heat-set fibers may also be treated by this device. Such treatment helps the fabric resist shrinking. A patented process called Sanforizing preshrinks fabric. Preshrinking prevents fabric from shrinking or stretching in home laundering. Other finishing treatments help fabrics resist wrinkling, fading, flames, water, stains, static electricity, bacteria, mildew, and moths. Other special finishes increase absorbency or reflect heat or light. One finish enables a fabric to change thickness in response to temperature changes.
The final step in manufacturing cloth is ironing it between heavy rollers. This process is called calendering. The fabrics are then rolled onto bolts for shipment to clothing makers and other customers.
The textile industry
Textile manufacturers worldwide produce more than 200 billion pounds (90 billion kilograms) of textile fiber annually. Tens of millions of people are employed in the production of textiles throughout the world. In some less developed countries, workers weave fabrics of natural fibers by hand. In industrial nations, manufacturers work with both natural and manufactured fibers. They apply modern technology to produce high-quality products quickly and inexpensively. Textiles are important as both imports and exports in many countries.
In the United States and Canada.
The United States textile industry is concentrated in the Southern States, especially Georgia, North Carolina, and South Carolina. The U.S. government requires the textile industry to observe certain federal laws designed to protect consumers and give them information about the textiles they buy. The Wool Products Labeling Act of 1939 provides that all garments made of wool have a label telling the amount and kind of wool used. The Flammable Fabrics Act of 1953 prohibits the sale of fabrics that burn rapidly. The Textile Fiber Products Identification Act of 1960 requires that all textile items have a label listing the fibers from which they are made. The Federal Trade Commission (FTC) requires that most finished textile products have a permanent label giving instructions for the care of the item.
Canada’s Textile Labelling Act requires a label on all clothing to show the fiber content by percentage. The Competition Bureau enforces the law.
In Africa,
several nations have modern textile manufacturing plants. But many people also weave textiles by hand. In some countries, textile production ranks among the leading manufacturing activities. These countries include Botswana, Egypt, Ethiopia, Ghana, Kenya, Nigeria, and South Africa. Textiles are a chief export of Mauritius. Some peoples of Ghana and Togo weave a ceremonial fabric called Kente cloth. It is used in social and religious activities. In Northern Africa, many people weave fabric by hand as a form of Islamic art (see Islamic art ).
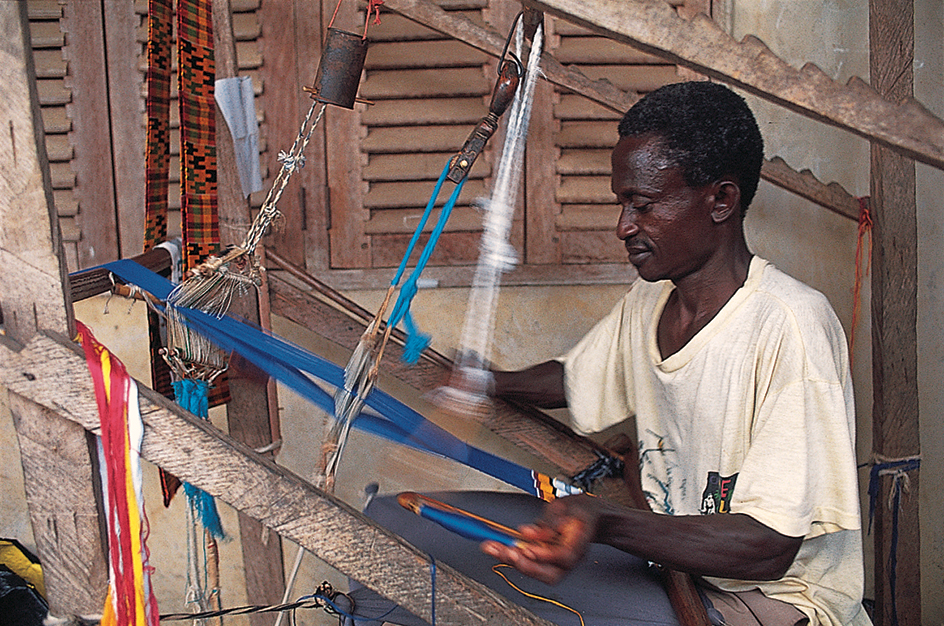
In Asia,
manufacturers operate many large, modern textile plants. China is the world’s leading producer of textiles. India is a leading producer of cotton fabrics. The textile industry is important to the economies of other Asian countries as well. They include Bangladesh, Indonesia, Japan, Malaysia, Pakistan, South Korea, Sri Lanka, and Vietnam.
In Australia and New Zealand,
textile production is modern and highly mechanized. Most textile factories are controlled by a few large firms. Australia’s government protects the textile and clothing industries against cheap imports.
In Europe,
textile production is highly mechanized. Germany, Italy, and Switzerland are leading exporters of textile machinery. European textile manufacturers have long been major innovators in the textile industry. They have developed many new fabrics and processes.
In Latin America,
textile production is important to the economies of most countries. Brazil is one of the leading producers of cotton fabrics. Textiles are a chief manufactured product of Bolivia, Chile, Colombia, Costa Rica, El Salvador, Haiti, Honduras, Nicaragua, and Paraguay.
History
Prehistoric and ancient times.
No one knows when people first made textiles. Impressions of cloth on pottery, as well as prehistoric weaving tools, indicate that people knew how to weave at least 27,000 years ago. The oldest known textile is a fragment of linen. It was found in what is now southern Turkey. The fragment dates from between 8000 and 7000 B.C. Evidence of woolen textiles comes from the same area. It dates from about 6000 B.C. In Egypt, people wove flax into linen wrappings about 5000 B.C. Archaeologists have found Egyptian mummies from the 2500’s B.C. wrapped in linen as well made as that produced today.
Cotton was grown in the Indus River Valley in what are now Pakistan and western India by about 3000 B.C. Cotton may also have been used for textiles in the Americas by this time. The Chinese began to cultivate silkworms about 2700 B.C. They developed special looms for silk filaments.
The ancient Greeks used chiefly woolen textiles. They also used some linen. In the 300’s B.C., the army of Alexander the Great brought cotton goods from what is now Pakistan to Europe. The ancient Romans developed an enormous trade in textiles. They imported woolens from Britain, Gaul, and Spain. They imported linen from Egypt, cottons from India, and silks from China and Persia.
During the Middle Ages,
from about the A.D. 400’s through the 1400’s, the textile industry gradually developed in Europe. As the textile industry expanded, production techniques improved. The spinning wheel came into use by the 1200’s. The production of woolens centered in England; northern Italy; and Flanders. Flanders was a region that covered parts of present-day Belgium, France, and the Netherlands. Italy became the silk center of Europe. The invention of a machine to unwind silk from cocoons led to further expansion of Italy’s silk industry.
In the large towns of Europe, associations of weavers and other craftworkers regulated textile production. These associations were called guilds. They established prices and standards of quality for all products made by their members. But the cottage industry, also called the domestic system, produced most textiles during the Middle Ages. Under this system, merchants delivered raw materials to workers in their homes in rural areas. The merchants later collected the work. They paid the workers by the piece.
The Industrial Revolution.
Important developments in textile production continued after the Middle Ages. For example, an English clergyman named William Lee invented a machine for knitting hosiery in 1589. During the 1600’s, textile workers in the Netherlands developed improved methods of dyeing and finishing cloth. But the greatest advances in the textile industry occurred during the Industrial Revolution. The Industrial Revolution was a period of rapid industrialization. It began in England in the 1700’s. In fact, the Industrial Revolution was largely a “textile revolution” created by a flood of English inventions that increased the production of yarns and fabrics.
In 1733, John Kay, an engineer, invented the fly shuttle (also called the flying shuttle). This device enabled weavers to pass the filling through the warp yarns mechanically instead of by hand. About 1764, a weaver named James Hargreaves invented the spinning jenny. It was the first machine that could spin more than one yarn at a time. In 1769, Richard Arkwright, a former barber, patented the water frame. It was a spinning machine that ran on water power. A weaver named Samuel Crompton introduced the spinning mule in 1779. This machine combined the features of the spinning jenny and the water frame. It gradually replaced them both. Edmund Cartwright, an Anglican clergyman, patented the first power loom in 1785.
In the United States, the New England region became the center of the textile industry. In 1790, an English textile worker named Samuel Slater built the first successful water-powered machines for spinning cotton in the United States. The machines were installed in a mill in Pawtucket, Rhode Island.
The production of cotton textiles in New England grew rapidly after the American inventor Eli Whitney developed his cotton gin in 1793. Before Whitney’s invention, workers had to remove cotton fibers from the seed by hand. This slow process could not meet the textile mills’ demand for cotton. Whitney’s gin separated the fibers far faster than workers could by hand. As a result, textile mills received ever-increasing supplies of cotton. During the 1920’s and 1930’s, most of these mills moved to the Southern States, nearer to the supply of cotton.
The age of modern textiles
began in 1884. In that year, Hilaire Chardonnet, a French chemist, developed the first practical manufactured fiber. This fiber, now known as rayon, was first produced in the United States in 1910 under the name artificial silk. Wallace H. Carothers, an American chemist, developed nylon in the mid-1930’s. During the 1940’s and 1950’s, polyester, acrylic, and other manufactured fibers were introduced.
In the 1960’s, textile companies began making double-knit fabrics of textured polyester yarns. These fabrics were lighter in weight and more comfortable than double knits made of other materials. As a result, the popularity of knits increased.
Today the textile industry is modern and diversified. Computerized equipment can produce fabrics with complex patterns at tremendous speeds. Continued research and development has resulted in new processing methods. These methods enable manufacturers to maintain reasonable production costs.