Wool is a fiber that comes from the fleece of sheep and some other animals. It makes durable fabrics used in manufacturing blankets, clothing, rugs, and other items. Wool fabrics clean easily, and they resist wrinkles and hold their shape well. Wool also absorbs moisture and insulates against both cold and heat. All these features make wool popular for coats, sweaters, gloves, socks, and other clothing.
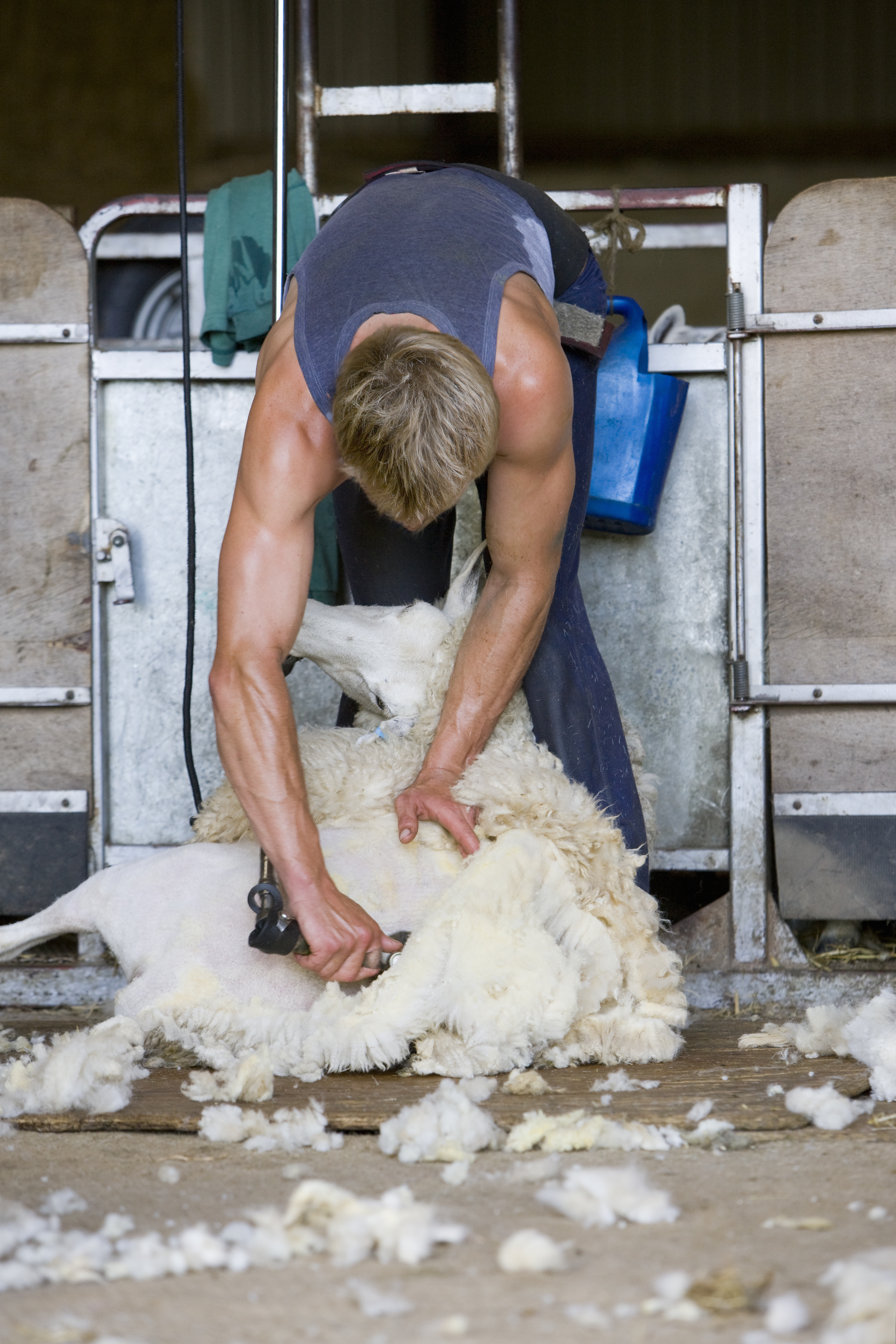
Wool fibers are nearly cylindrical in shape. Overlapping scales on the surface make the fibers mat and interlock under heat, moisture, and pressure. This property of wool fibers is called felting. Felting increases the strength and durability of wool fabrics. It also enables wool to be made into felt.
The guidelines of the United States Federal Trade Commission (FTC) define wool as the fiber from the fleece of sheep. Wool also includes such fibers as alpaca, from alpacas; camel’s hair; cashmere, from Cashmere goats; mohair, from Angora goats; and vicuna, from vicunas.
Worldwide production of raw wool totals about 4 billion pounds (1.75 billion kilograms) annually. The leading wool-producing nations are Australia and China. Every state in the United States produces some wool. California, Colorado, Utah, and Wyoming rank among the leading producers.
Sources of wool.
Almost all wool comes from sheep. These animals—and their wool—are classified into five groups, depending on the quality of the fleece. The five classifications of wool, listed here in order of quality, are (1) fine wool, (2) crossbred wool, (3) medium wool, (4) long wool, and (5) coarse wool, or carpet wool.

Fine-wooled sheep
include the Merino and breeds with Merino ancestry, such as the Debouillet and the Rambouillet. These types of sheep produce the finest wool, which makes high-quality clothing.
Crossbred-wooled sheep,
such as the Columbia and Corriedale are crossbreeds of fine- and long-wooled breeds. Their wool is used for rugged clothing.
Medium-wooled sheep
provide wool used in making industrial and upholstery fabrics. Cheviot, Dorset, Hampshire, Oxford, Polypay, Shropshire, Southdown, and Suffolk sheep are in this group.
Long-wooled sheep
include the Cotswold, Leicester, Lincoln, and Romney. They produce wool used for carpets and industrial fabrics.
Coarse-wooled sheep
include the Karakul and Scottish Blackface. The wool of these animals is used mostly for carpets and handicraft yarns.
Types of wool
are determined by the quality of a sheep’s fleece. The quality depends on the age and physical condition of the animal and by the climate in which it lives. An oily substance called yolk covers the fleece of a healthy sheep. Yolk consists of wool grease and suint (dried perspiration). It protects the sheep from rain and keeps the fleece from becoming matted.
Young sheep produce the best wool. The softest and finest wool, called lamb’s wool, comes from 6- to 12-month-old sheep.
Sheep that have been slaughtered for their meat provide pulled wool, sometimes called skin wool or slipe wool. Dead wool comes from sheep that have died or are seriously ill. Fleeces soiled by manure or dirt are called tag locks in the United States and stain pieces in England and Australia.
In the United States, FTC guidelines classify wool into two categories. Virgin wool, also called new wool, has never been spun into yarn or made into felt. Some fabrics are made of fibers that have been reclaimed from previously spun or woven wool. Recycled wool is the name given to these products. Fabrics made from recycled wool are sometimes called shoddy.
Processing of wool
involves four major steps: (1) shearing, (2) sorting and grading, (3) making yarn, and (4) making fabric.
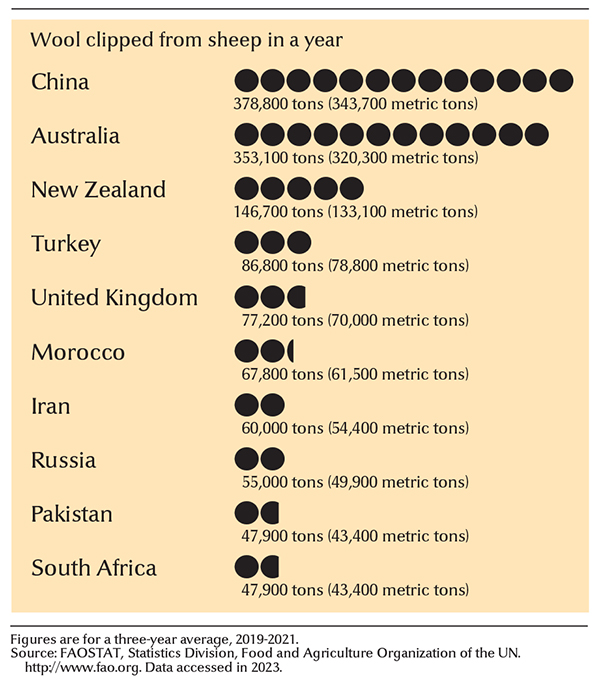
Shearing.
Most sheep shearers use power shears, and experts can clip 100 or more animals a day. They remove the fleece in one piece so the various parts can be easily identified for sorting and grading. Different parts of a fleece vary in quality. For example, the best wool comes from the shoulders and sides of the sheep, while the poorest comes from the belly areas.
During the 1990’s, researchers in Australia began to use a process that eliminates much of the hard work involved in shearing and produces higher quality wool. The process, known commercially as Bioclip, involves injecting sheep with a protein that causes them to naturally shed their fleece. This process must be further refined before it can gain widespread use.
In most parts of the world, sheep ranchers shear their animals once a year, in spring or early summer. But in some regions, the fleeces may be cut off twice yearly, with the second shearing occurring in the autumn.
Sorting and grading.
Workers remove any stained, damaged, or inferior wool from each fleece and sort the rest of the wool according to the quality of the fibers. Wool fibers are judged not only on the basis of their strength, but also by their (1) fineness (diameter), 2) length, (3) crimp (waviness), and (4) color.
There are three methods of grading wool. The blood method involves comparing the fineness of the wool fibers with the fineness of Merino wool. The count method involves counting the number of hanks—that is, 560-yard (512-meter) lengths of worsted yarn—that can be spun from one pound of wool fiber. The most precise method involves measuring the diameter of the fibers in units called microns. A micron equals 0.001 millimeter (1/25,400 inch).
Fiber length is important in determining what processes will be used to make yarn and fabric. Carding length fibers, also called clothing length fibers, measure less than 11/2 inches (3.8 centimeters) long. French combing length fibers range from 11/2 to 21/2 inches (3.8 to 6.4 centimeters) in length. Combing length fibers are more than 21/2 inches (6.4 centimeters) long.
The natural crimp of wool provides the fibers with elasticity. This property enables wool fabrics to hold their shape after being stretched or twisted. The best wool fibers have many evenly spaced waves.
The color of most wool ranges from white to dark ivory. White wool is the most desirable because manufacturers may have to bleach darker wool before it can be dyed.
Making yarn.
Woolen mills scour the wool with detergents to remove the yolk and such impurities as dust and sand. Wool grease from the yolk is processed into lanolin, a substance used in hand creams and cosmetics.
After the wool dries, machines card it. The carding process involves passing the wool through rollers that have thin wire teeth. The teeth untangle the fibers and arrange them into a flat sheet called a web. The carding machines then form the web into narrow ropes known as slivers.
After carding, the processes used in making yarn vary slightly, depending on the length of the fibers. Carding length fibers are used in making woolen yarn. Combing length and French combing length fibers are made into worsted yarn. The processes used for the two kinds of yarn are similar. But worsted slivers go through an additional step called combing, which removes impurities and short fibers.
After carding or combing, machines stretch and slightly twist the slivers to form thinner strands called rovings. Spinning machines then twist the rovings into yarn. Woolen yarn is bulky and fuzzy, with fibers that lie in different directions. Worsted yarn is smooth and highly twisted, and its fibers lie parallel.
Making fabric.
Wool manufacturers knit or weave yarn into a variety of fabrics. They use woolen yarns in making flannel, homespun, melton, Saxony, Shetland, and tweed fabrics. Worsted yarns make such fabrics as broadcloth, crepe, gabardine, serge, sharkskin, twill, and whipcord. Almost all wool fabrics except felt are made from yarn (see Felt ).
Wool may be dyed at various stages of the manufacturing process. Dyeing that takes place before the fibers are spun is called stock dyeing or top dyeing. Dyeing that occurs after the fibers have been spun into yarn is called yarn dyeing, package dyeing, or skein dyeing. If the dyeing takes place after the fabric has been woven, it is known as piece dyeing. Most fabrics with fancy designs are stock dyed or yarn dyed. Piece dyeing is used for solid-colored fabrics. See Dye.
All wool fabrics undergo finishing processes to give them the desired appearance and feel. The finishing of fabrics made of woolen yarn begins with fulling. This process involves wetting the fabric thoroughly with water and then passing it through rollers. Fulling makes the fibers interlock and mat together. It shrinks the material and gives it additional strength and thickness. Worsteds go through a process called crabbing, in which the fabric passes through boiling water and then cold water. This procedure strengthens the fabric.
Some wool fabrics tend to shrink when dry-cleaned. To prevent such shrinkage, some manufacturers pre-shrink the fabric. One popular process, called London Shrinking, uses water and pressure to shrink the fabric. After the various finishing processes, manufacturers cut and sew the fabric into clothing and other products.
History.
About 10,000 years ago, people in central Asia began to raise sheep for food and clothing. The art of spinning wool into yarn developed about 4000 B.C. and encouraged trade among the nations in the region of the Mediterranean Sea.
The first wool factory in England was established about A.D. 50 in Winchester by the Romans. The wool industry soon played a major part in England’s economy. By 1660, the export of wool fabrics accounted for about two-thirds of England’s foreign trade.
Merino sheep originated in Spain. In the early 1500’s, explorers from Spain brought sheep to what is now the United States. England discouraged the wool industry’s growth in the American Colonies so that the colonists would have to rely on English goods. But colonists smuggled sheep from England. By the 1700’s, spinning and weaving were flourishing in the United States. The British began breeding Merinos in the late 1700’s. In 1797, they brought a small flock of Merinos to Australia, laying the foundation for that country’s Merino sheep industry.
In the 1800’s, many pioneers brought sheep with them while traveling to the western United States. As a result, the production of wool and wool fabrics spread to nearly all parts of the United States.