Brick is a rectangular building block made of clay, shale, or various other materials. Bricks are strong, hard, and resistant to fire and damage from the weather. They are used to build such structures as houses, commercial and public buildings, fireplaces, and furnaces.
Bricks have been used as a building material for thousands of years. At first, people produced bricks by drying hand-shaped or molded blocks of clay or mud in the sun. Today, most bricks are formed by machines and fired (baked) in large kilns (ovens).
Kinds of bricks
Bricks are divided into two general groups: (1) building bricks, and (2) refractory bricks. Typical building bricks measure 21/4 inches (5.7 centimeters) thick, 33/4 inches (9.5 centimeters) wide, and 8 inches (20 centimeters) long. Refractory bricks are available in various sizes. Most are slightly larger than building bricks.
Building bricks.
The highest-quality and most attractive building bricks are called face bricks. These bricks are used in highly visible areas of structures, such as the interior or exterior walls of houses. Face bricks come in a variety of colors and surface textures, and they are extremely uniform in shape and size. Most are made from high-grade fire clay or low-grade shale. Warped, off-color, and other slightly defective bricks are called common bricks. Common bricks are used in less visible places than are face bricks.
Refractory bricks,
also called refractories, can withstand temperatures between 2000 and 4000 °F (1100 and 2200 °C). They are also highly resistant to chemical damage, physical wear, and thermal cycling (rapid changes in temperature). Refractories are used in a wide variety of structures, including fireplaces and industrial furnaces. Thin refractories were used on the outside of the United States space shuttles to provide protection against high temperatures.
Refractories vary in composition according to their use. The main types are made from such raw materials as alumina, carbon, chrome ore, dolomite, fire clay, magnesite, silica, and zircon.
How bricks are made
The methods used to make bricks vary according to the raw material being used, the intended use of the brick, and other factors. However, the commercial production of bricks generally involves four basic steps: (1) preparing the raw material, (2) forming bricks, (3) drying bricks, and (4) firing bricks.
Preparing the raw material
includes grinding or crushing it, removing its impurities, and letting it dry. The material is then stored in bins until it is mixed into brickmaking batches.
Forming bricks.
There are three main processes used to form bricks: (1) stiff-mud, (2) soft-mud, and (3) dry-press.
The stiff-mud process
is used to form by far the majority of building bricks produced in the United States. In this procedure, the ground brickmaking material is mixed with water to form a stiff mud. A machine presses air out of the mud and shapes the material into a long ribbon by forcing it through an adjustable opening in a process known as extrusion. The ribbon is cut into bricks by wires rotating on a machine called a brick cutter. The bricks can then be stacked for oven drying.
Before they are dried, many stiff-mud face bricks receive surface treatments to vary their texture and appearance. The bricks may be gouged, rubbed, or scraped, or they may be sprayed with chemical solutions that affect the surface. In addition, stiff-mud bricks are often made with holes in them. The holes make the bricks lighter and save on raw materials. The holes also provide additional space for mortar, the substance used in bricklaying to bind the bricks together.
The soft-mud process
is used to produce all handmade and some machine-made bricks. In this method, the brickmaking material is mixed with more water than in the stiff-mud process. The soft mud thus produced is easily molded into bricks. Soft-mud bricks must be hardened by air drying before they can be stacked for oven drying. This step creates extra work and makes the soft-mud process slower than other brickmaking methods. In the United States, the soft-mud process is used mainly to produce specially shaped bricks that cannot be formed by other methods.
The dry-press process
is used to form most refractory bricks. In this process, a dry or damp brick mix is placed into a steel mold box and compressed into brick form by a hydraulic (water-powered) ram. The ram may exert as much as 15,000 pounds per square inch (1,050 kilograms per square centimeter) of pressure on the mix. The resulting bricks are quite dense.
Drying bricks
helps prevent them from developing cracks or other structural defects during firing. Most bricks are dried in tunnel ovens. These ovens can reach temperatures as high as 400 °F (204 °C). The bricks are stacked in layers on cars that move through the ovens. Drying time and temperature vary, depending chiefly on how much moisture the bricks contain.
Firing bricks
at high temperature causes their particles to bond together, forming a strong, hard block. Most bricks are fired in tunnel kilns. The kilns generally range from 7 to 28 feet (2.1 to 8.5 meters) in width and 250 to 440 feet (76 to 134 meters) in length. They are fueled by gas, oil, or such solid fuels as sawdust or coal. They reach temperatures of 1800 to 2400 °F (1000 to 1300 °C) for firing building bricks and 3400 °F (1900 °C) for firing refractories.
In tunnel kiln firing, bricks are stacked on cars that move through the kiln. The ends of the kiln are not as hot as the middle. The bricks therefore are gradually heated to a maximum temperature in the middle of the kiln, and then they cool as they proceed out of the kiln. Different kinds of bricks are fired at different temperatures and for varying lengths of time, depending primarily on their grade and composition.
Some bricks are fired in periodic or shuttle kilns. These kilns can reach the same temperatures as tunnel kilns, but they fire only one batch of bricks at a time. In some areas, bricks are put in the sun to bake. Such bricks are called sun-dried or sun-baked bricks or adobe (see Adobe ).
Bricklaying
Bricks are usually laid horizontally in layers called courses. The bricks are bound together with mortar, which forms joints between them. In general, courses are arranged so that vertical joints do not fall directly above one another. Staggering the vertical joints distributes the weight and pressure of the bricks over a large area. A structure that is made of bricks is called brickwork or brick masonry.
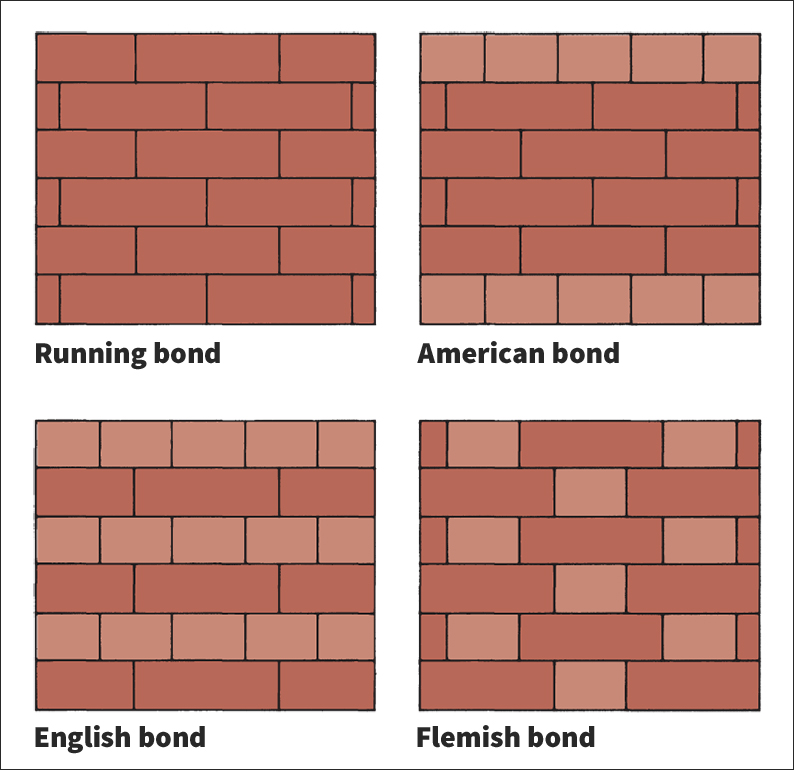
Bonds.
Bricks laid with their short ends exposed are called headers. Those laid with their long sides exposed are called stretchers. Headers and stretchers are arranged to form different bonds (patterns). The most commonly used bonds include running, American, English, and Flemish. In running bond, all the bricks are stretchers. American bond typically has four to six stretcher courses laid between single header courses. English bond consists of courses of headers alternating with courses of stretchers. The joints of every other course of English bond line up vertically. In Flemish bond, each course is made up of alternating headers and stretchers, with the headers centered on the stretchers above and below.
Mortar
is used to hold both building and refractory brick structures together. However, the composition of the mortar differs with the type of brick and with structural needs.
Mortar that is used to bind building bricks is composed of portland cement, lime, sand, and water. The mortar holds the bricks in position and makes a strong, tight wall that can resist moisture. The thickness of mortar joints between building bricks ranges from 1/4 to 1/2 inch (6.4 to 13 millimeters). Bricklayers form the joints by smoothing mortar on the bricks with a wedge-shaped tool called a trowel.
Mortar used to bind refractory bricks must be able to withstand the same high temperatures, chemical reactions, and wear as the bricks themselves. Refractory mortar consists of calcium aluminate cement, water, and a finely ground hard material similar in composition to the bricks being joined. Mortar joints between refractory bricks are no thicker than 1/16 inch (1.5 millimeters). Extremely thin joints are made by dipping the bricks into soupy mortar and then pressing them together.
History
Brick is the oldest manufactured building material. Sun-dried bricks were being made in the Middle East by 6000 B.C. Fired bricks were being produced in the same region by 3500 B.C. Brickmaking technology was later spread to much of Europe by the Romans.
Brickmaking declined in England during the Middle Ages (about the A.D. 400’s through the 1400’s) due to changes in architectural styles and availability of wood, stone, and other building materials. But the brickmaking industry grew following the Great London Fire of 1666. Many of the buildings in the city had been made of wood and were therefore destroyed by the fire. When the city was rebuilt, many of the new buildings were constructed of brick.
In what is now the United States, the Indians of the Southwest built houses of adobe long before the arrival of European settlers. The commercial production of bricks in America began in the 1600’s.
Brick was used to pave streets and sidewalks until the 1900’s, when it was largely replaced by concrete for paving. Today, building bricks remain important construction and decorative materials. Refractory bricks play an important role in many industrial procedures, including the production of aluminum, cement, glass, iron, paper, petroleum, and steel.