House is a building that provides shelter, comfort, and protection for its inhabitants. Houses range in size from small cottages to huge mansions. Many rise two or more floors, and others spread in long, low lines across the ground. Houses vary greatly in appearance, depending on when and where they were built and what building materials were used.
Building materials
Houses are often classified according to the chief type of building material used. For example, we speak of frame (wood) houses; brick houses; and stone houses. A combination of materials may also be used. For example, a thin layer of brick or stone called veneer may be applied over wood. Prefabricated houses are built with factory-made sections assembled at the building site. Manufactured houses are built completely in factories and moved to the homesite. The kind of materials used in the construction of a house depends mainly on the size of the house, its location, its design, and the climate.
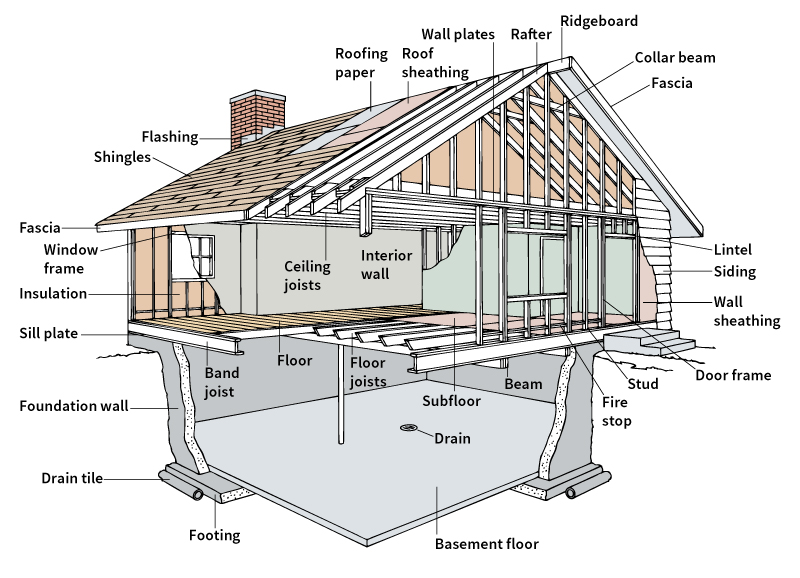
Wood
has long been a popular building material because it is usually more plentiful and cheaper than other materials. Houses are often made of fir, pine, hemlock, redwood, and spruce. Redwood and cedar often are used for the siding (outer covering), if the siding is not going to be painted. Other woods, including oak, cypress, maple, walnut, and birch, are used for such interior features as stairways, cabinets, floors, and doors.
Brick
is one of the oldest and most common building materials. Brick wears well and, like wood, is usually easy to obtain. Builders often use brick when building codes require a more fire-resistant material than wood—for example, in the construction of row houses. Bricks are available in a number of colors and finishes.
Concrete block and stone
make strong, attractive houses that are relatively cheap to maintain. Concrete blocks are made by pouring a mixture of cement, sand, water, and other materials into a mold. Builders also make houses of stone that has been taken from quarries and split into usable sizes. Because stone is an expensive building material, it is usually applied as a veneer over an inner wall of brick or concrete block.
Other materials.
Builders often cover a house’s exterior with aluminum or vinyl siding. These types of siding provide insulation, prevent rotting, and save much repainting and repairing. Window frames may be made of aluminum or vinyl, or wood clad with aluminum or vinyl for protection against the weather. Manufacturers coat nails for use in home construction with zinc, copper, nickel, or aluminum to make them rustproof.
Building a house
A person building a house must first select a lot (piece of land). The next step is to consult an architect or builder. This expert will check local zoning laws and electrical, building, and plumbing codes. Knowledge of these codes protects the homeowner in both the present and the future. For example, the building code in an area may specify how deep the foundation must be, based on soil conditions and the depth to which the ground freezes.
The architect then designs the house according to the owner’s ideas and budget. The architect must also consider the size and shape of the lot and the location of the house on the lot. The architect prepares construction drawings, which provide information on the size of the house and details of how it is to be built. These drawings are the basis of the contract between the builder and the homeowner. The architect also prepares specifications, a written description of the house materials. The drawings and specifications are used to determine the cost of the house and to obtain a building permit from the community.
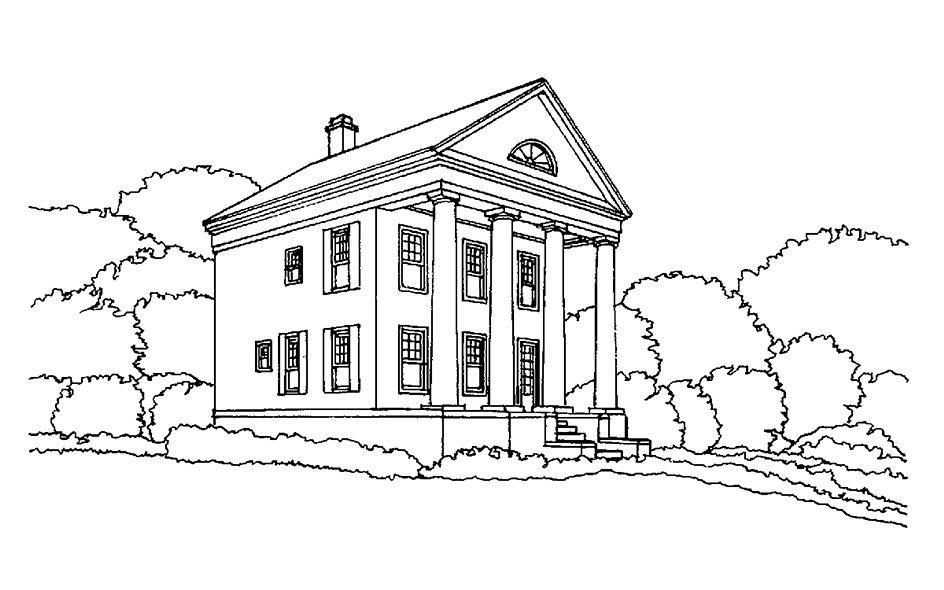
The following sections describe the steps involved in building a typical frame house.
The foundation
supports the house. First construction workers begin excavating (digging) holes or trenches for the footings, the lowest part of the foundation. The footings support each wall load. They are made by pouring concrete into wood or steel forms that workers place below the frostline, the depth to which the ground freezes. This is done so that the footings will not freeze and shift. Builders generally use concrete or concrete block for the house’s foundation. The foundation walls rest on the footings. These walls rise from 8 inches to 3 feet (20 to 90 centimeters) above the ground.
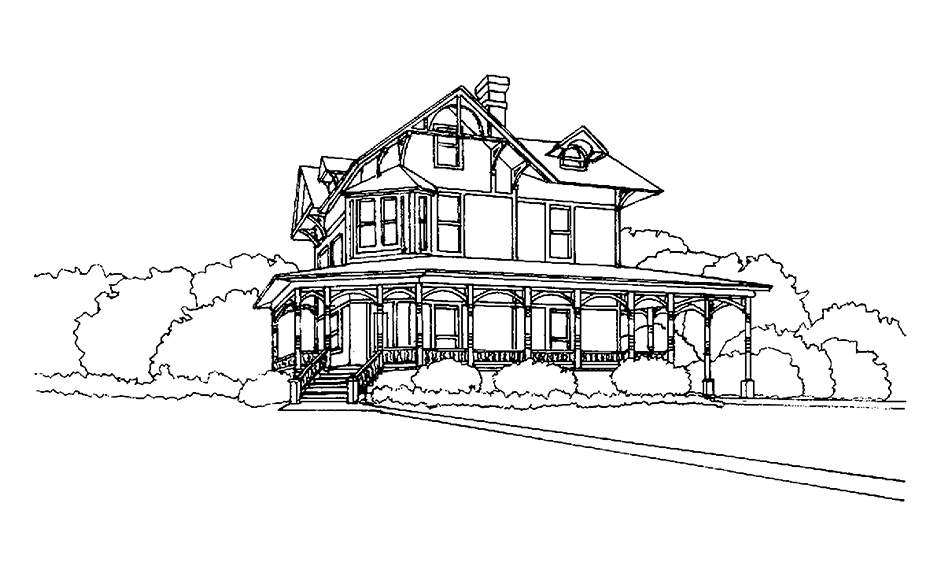
An area within the foundation below the first story is called a basement. Basements add to the cost of building a house, but they provide extra room. Many basements have separate rooms for the home’sheating unit and laundry equipment, and for storage. Some basements also have a recreation room.
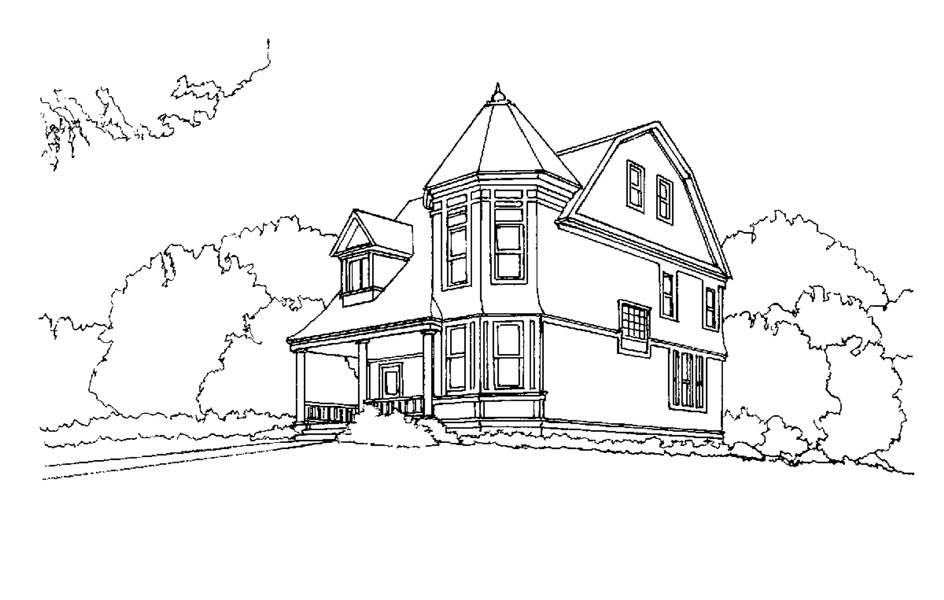
Most of the houses built today do not have basements. In many low or damp regions, houses are raised above the ground on concrete piers (supports). Sometimes a slab foundation is laid directly on the ground, especially if the earth beneath the house is hard. The ground must first be graded (leveled). Workers then spread a filler, usually stone, and cover it with a thin plastic sheet called a moisture barrier. The workers pour concrete over the moisture barrier, forming a slab about 4 inches (10 centimeters) thick. The barrier prevents moisture from coming through the slab.
The frame
is the skeleton around which the rest of the house is built. After the footings and foundation have been formed, workers bolt wooden beams called sills to the foundation. The sills support the outside walls. Floor joists, beams that support the floor, are attached to the sills about 16 inches (40 centimeters) apart. In many cases, the joists run from one sill to the sill on the opposite side of the house. In other cases, the joists run to an intermediate support beam or an interior support wall called a bearing wall. Floorboards or plywood nailed on top of the joists make the bottom layer of the floor. The structure is then solid enough to hold the wall frames.
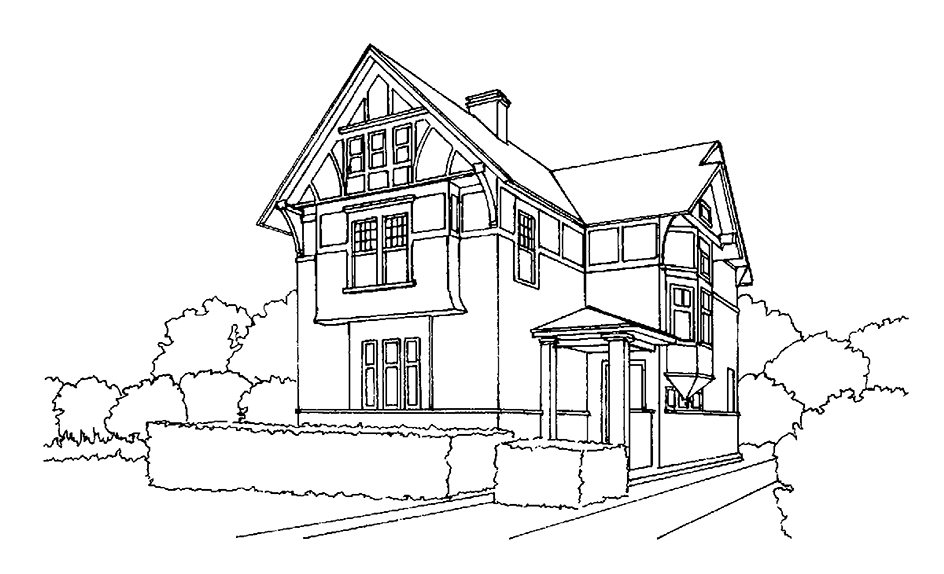
Wall frames include vertical pieces of lumber called studs and horizontal pieces called plates. Carpenters assemble and nail together each wall frame separately before attaching it to the sill. Then they lift each frame into place and brace it temporarily. When all the outside walls have been raised, they are nailed together and braced permanently.
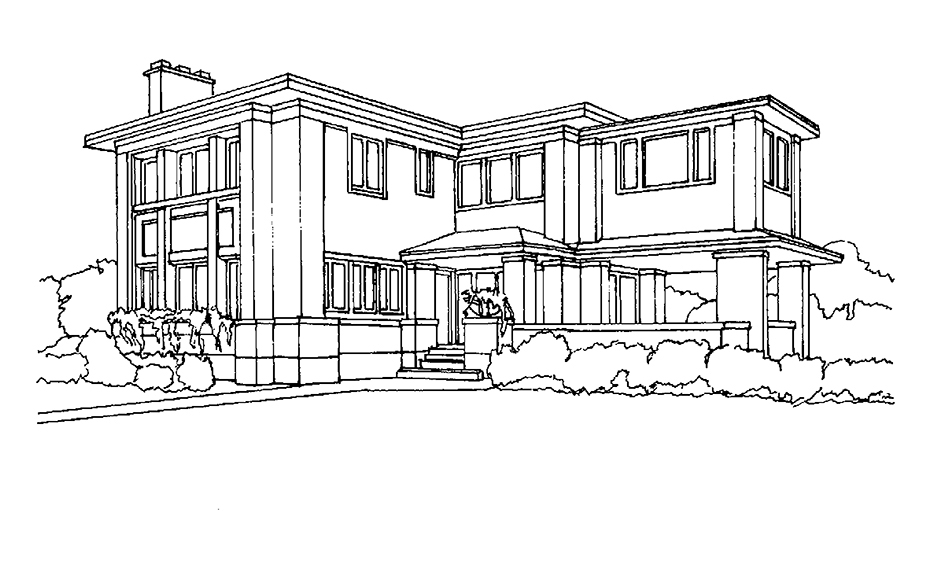
The sheathing (the inner layer of the outside walls) may be wood, fiberboard, or plywood nailed to the studs. Usually, builders cover the sheathing with waterproof paper called building paper or with a thin plastic sheet called house wrap. Then they add the siding. Siding may be aluminum, brick, stone, or wood.
The roof
seals the top of the house. Some roofs are flat, but most are slanted to shed rain and snow. Slanted roofs are often formed by pieces of lumber called rafters. Carpenters nail the bottom ends of the rafters to the plates at the top of the outside walls. The rafters slant from the plates and meet at the ridgeboard, a board placed at the ridge (top edge) of the roof, or at a similarly placed ridge beam. Rafters support the roof’s weight.
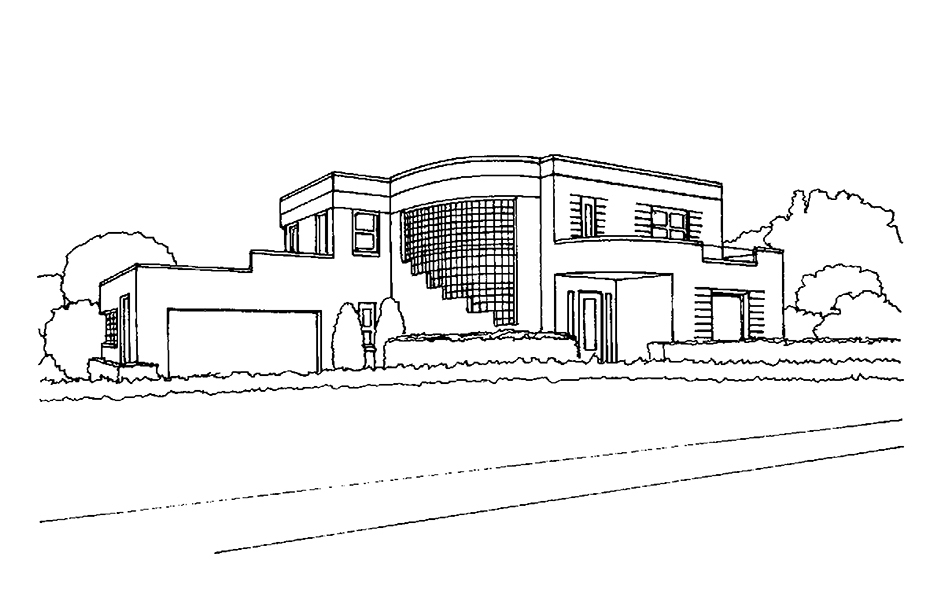
After carpenters nail sheathing to the tops of the rafters, they add heavy building paper or roofing felt to it. Then they add the final layer of asphalt, wood, or slate shingles. They usually cover flat roofs with asphalt or with a membrane roof of rubber sheet roofing. Flashing (strips of sheet metal) placed around the chimney and other roof openings prevents water leakage.
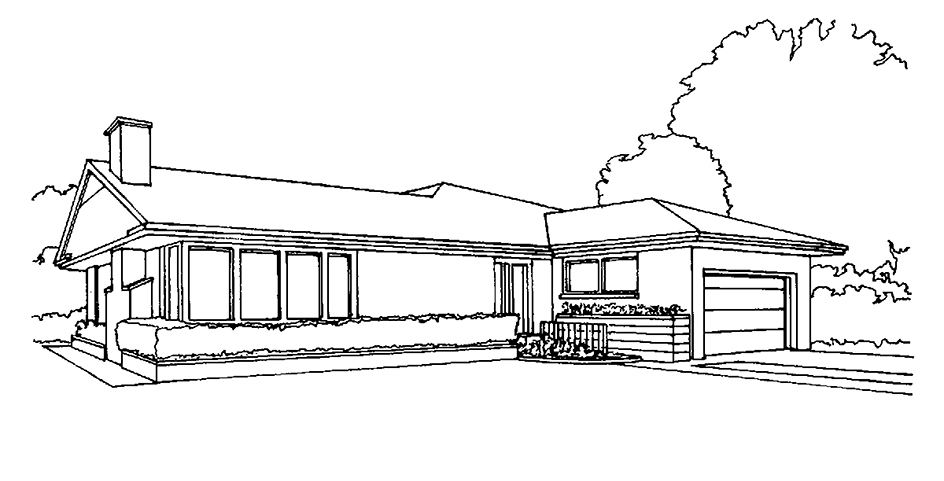
Interior construction
includes (1) floors, (2) walls, (3) windows, and (4) doors.
Floors
have a lower layer and upper layer. The lower layer, called the subfloor, usually consists of sheets of plywood that are 3/4 inch (1.9 centimeters) thick. Some subfloors may consist of boards nailed at an angle across the floor joists.
The upper layer is known as the finished floor. Finished floor coverings include wood; carpeting; linoleum; rubber; cork; and vinyl, ceramic, and stone tile. Wood flooring is often made from tongue-and-groove boards. One side of each board has a projecting piece called a tongue, and the other side has a matching slot called a groove. The tongue of one board fits snugly into the groove of another board. Carpenters drive nails through the groove side so that the nailheads do not show on the finished floor. Most finished floors are made of hardwoods, such as maple or oak, that have been finely sanded. The wood may then receive an application of wax, shellac, varnish, or plastic, or it may be covered with a carpet.
Walls.
Rooms are made by building inside walls after the outside walls have been attached to the foundation. Inside walls, also called partitions, are really small-sized frames like the outside walls. They have studs and must be supported by plates, joists, and girders.
If plaster is to be applied, the interior walls must first be covered with lath—horizontal strips of wood, metal mesh, or plasterboard. Gypsum wallboard is commonly used instead of plaster on partitions. Wood or plywood boards may also be used.
Windows.
Most parts of a window come from a lumber mill or are manufactured by window companies. Windows that open have two parts, the frame and the sash. The sash, which holds the glass, swings or slides open. The frame fits into the opening left in the structure’s frame and is nailed into place. Window frames and sashes may be made of wood, metal, or vinyl.
Doors.
Both doors and doorframes may usually be bought ready-made. Carpenters attach the doors high enough to swing over rugs or carpets. A threshold fills in the space under an outside door and provides protection against the weather.
Electrical wiring
provides lighting and furnishes outlets for lamps, washing machines, and other appliances. In some houses, electric power also provides heat. Before construction starts, the builder determines the location and type of wiring. Wires vary in size, depending on the equipment in the house and how far the current must travel. Standard wiring in the United States is designed for 110-volt current. But builders often specify heavy-duty, 220-volt wiring if large electrical appliances or an air conditioning system are installed.
Electricians install wiring after carpenters have built the frame. Wiring is done in a series of circuits. Each set of wires has several outlets. Electricians often place the wiring for a furnace on a separate circuit. This keeps the furnace running in case another circuit breaks down.
Wires become hot and can cause fires if they are overloaded, so electricians may install a protective switch called a circuit breaker for each electrical circuit. If the circuit becomes overloaded, the circuit breaker automatically cuts off the current. Instead of circuit breakers, many older houses have protective devices called fuses, which contain a wire that melts easily. If too much current passes through a circuit, the wire in the fuse melts, or “blows.” A fuse box holds all the fuses.
Plumbing.
During construction, plumbers install the pipes that will supply gas and water, and carry away waste. They install bathroom fixtures and sinks just before other workers add the finishing touches to the house. Plumbers also install traps to keep out sewer gas. The trap used for bathroom washbasins, for example, is a P-shaped pipe directly below the drain. Water settles in the lower part of the pipe and prevents sewer gas from backing up and leaking into the room. To function properly, traps must have outside ventilation. The vent or vent stack, the small pipe that projects from the roof of a house, is a ventilating pipe for sewer gas.
A cast-iron waste-disposal pipe runs from inside the house to the outside, where it connects to the citysewerage system. In areas without a city sewerage system, a septic tank near the house holds sewage until it dissolves. Water from the sewage flows through pipes into the ground. The sludge remaining in the tank must be removed at intervals.
Insulation
reduces the amount of heat or cold that passes through walls, floors, and ceilings. When the air around the house is warmer or colder than the air inside, heat passes from the warm air to the cold air. This means that in winter, the heat will pass to the outside, and the house will become cold. In summer, the heat outside passes into the house. Insulation fills the air spaces in walls, floors, and ceilings and creates dead-air space. This helps prevent heat from passing through. Insulation can save fuel costs in heating a house.
Insulation is made from many materials, including cellulose, rock wool, a glassy lava called perlite, gypsum, certain plastics, and fiberglass. Insulation comes as blankets, boards, paper, and sheathing. It is also available in a loose, crumblike form. The type of insulation used depends on the climate and on whether it insulates floors, ceilings, or walls.
Heating and air conditioning.
Most houses have central heating systems. One furnace or boiler supplies heat for the entire house. Such houses are heated by warm air, steam, or hot water. In hot-air heating, a fan connected to the furnace blows warm air through ducts (pipes) into the rooms. In steam or hot-water heating, the steam or hot water produced in a boiler passes through radiators that stand throughout the house. In radiant heating, hot-water pipes run under the floors or in the ceilings or walls.
Air-conditioning units may be used to cool houses. An air conditioner takes warm air from the house, cools it, removes moisture, and recirculates cool air. An air conditioner with a heat pump may warm cold air, add moisture, and recirculate warm air.
Interior design.
In a new house, the builder usually paints the rooms and finishes the floors as part of the contract with the homeowner. The owner generally selects, buys, and arranges the furnishings. But sometimes the owner hires a professional designer to do this job.
Landscaping
is the last step in building a house. Most builders try to keep the natural outline of the land and to preserve the trees. After the house is finished, the builder may plant seed or lay rolls of grass turf for a lawn around the house. The builder may also plant trees and shrubs. The homeowner may have a firm of landscape contractors provide landscaping. The homeown-er also may hire a landscape architect to design a garden or landscape.