Lead is a heavy, bluish-gray element. It was one of the first metals used by human beings. Compared with other metals, lead has a low melting point. It is soft and can be easily shaped. Because of these properties, people have used lead for thousands of years. They used the metal to make coins, vessels, pottery, and projectiles. Today, the main use of lead is in lead-acid storage batteries. Such batteries provide power for the electrical systems of automobiles, airplanes, and many other vehicles. See Battery (Lead-acid batteries).
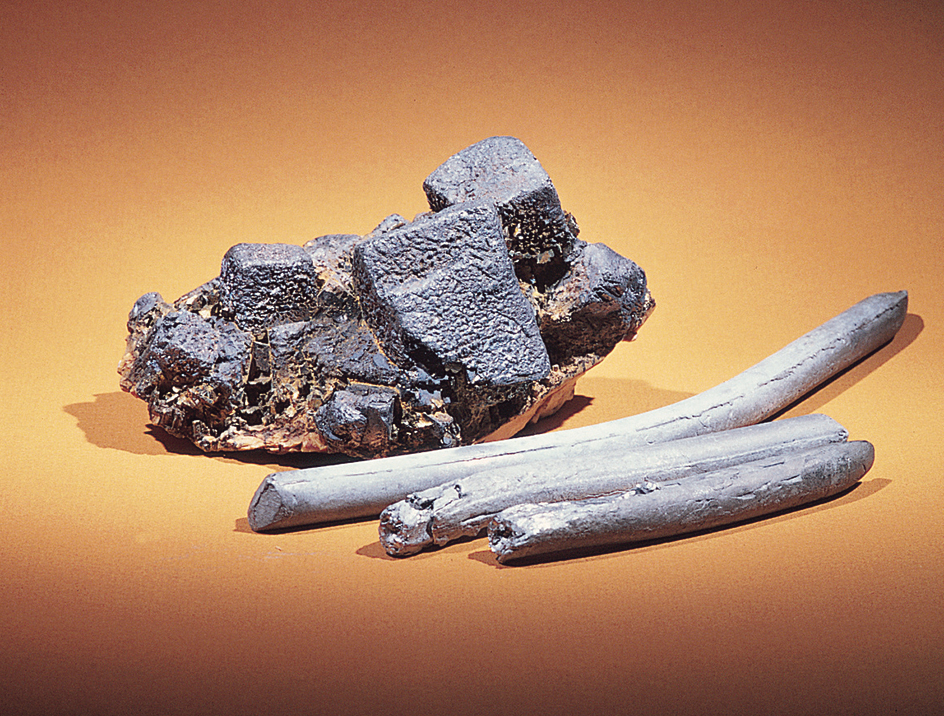
In the past, lead was widely used in paints and gasoline. Because of the impact of lead on human health and the environment, people became concerned about the use of lead. The human body can absorb lead, resulting in lead poisoning under certain circumstances. Lead poisoning may occur among workers in plants where large quantities of lead fumes or dust are generated and where exposures are long-term.
Lead poisoning can also occur in children who eat chips of lead-based paint that have flaked from painted surfaces in older homes. Today, lead use in paints and gasoline has been greatly reduced. This effort has stopped the input of lead into the environment in most industrialized nations. Lead is still released into the environment in many less developed countries.
Lead produced from mined ore is called primary lead. The world’s annual production of primary lead is about 5 million tons (4.5 million metric tons). An additional 6 1/2 million tons (5.9 million metric tons) are produced from recycling, mainly from lead-acid storage batteries. The process typically used to recover lead from batteries includes draining the acid, shredding the batteries, and melting and refining the lead components.
China is the leading producer of lead. Other major producers include Australia, India, Mexico, Peru, Russia, and the United States. The United States uses about 1.8 million tons (1.6 million metric tons) of lead each year. Most of it is produced by recycling. Most of the lead mined in the United States comes from Missouri and Alaska. Southeastern Missouri is a center of lead mining and refining. Alaska partially processes the lead ore, then ships the resulting concentrates for final processing. The processing takes place mainly in Canada. In Canada, New Brunswick and British Columbia are major producers.
Properties.
Lead has an atomic number (number of protons in its nucleus) of 82. Its relative atomic mass is 207.2. An element’s relative atomic mass equals its mass (amount of matter) divided by 1/12 of the mass of carbon 12, the most abundant form of carbon. For information on the position of lead on the periodic table, see the article Periodic table.
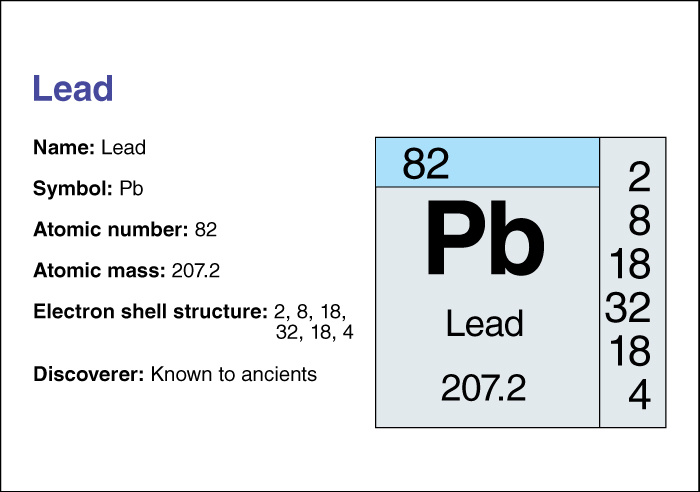
The melting point of lead is 327.5 °C. The metal boils at 1749 °C. Lead is also one of the heaviest elements. It has a density of 11.4 grams per cubic centimeter. Pure lead is soft and has little strength. These properties make it unsuitable for most applications. To make lead stronger, lead producers often alloy (mix) it with antimony and tin to form lead alloys. Lead occurs naturally as lead sulfide (also known as galena). Galena is a mineral with brilliant silver luster.
Lead is soft. It can be easily pressed or hammered into thin sheets. Its low melting point makes it easy to recover from ores and scrap. These properties, along with corrosion resistance, made lead useful in roofing and pipes for many centuries. The Latin word for lead is plumbum. The term plumbing comes from that word. Today, however, most pipes used in plumbing are made from materials other than lead. Lead resists corrosion by water and some acids, particularly sulfuric acid. Its corrosion resistance makes it useful in chemical industries.
Uses.
Over 90 percent of the lead produced in the United States is used in lead-acid batteries. Such batteries are reliable, cheap sources of energy. Other types of batteries can also be used in automobiles. Because they are more expensive than lead-acid batteries, however, they are not widely used.
Lead alloys have a variety of uses. Many manufacturers use a lead-tin alloy called solder to join metal surfaces. Lead alloys are used in radiation shields. Such shields provide protection in hospitals, nuclear reactors, and other facilities that use X rays and radioactive materials. Machinery manufacturers may use lead in alloys called babbitt metals. Babbitt metals often consist of lead mixed with antimony, tin, and other metals. Manufacturers also use lead alloys to make bearings. Bearings reduce friction between moving parts. There are also several commercially important lead compounds. These compounds are used in ceramics, glasses, rubber products, insecticides, and explosives. See Babbitt metals; Solder.
Production.
Typically, mining companies will develop a lead deposit in Earth’s crust if the deposit’s lead content is at least 3 percent. Most deposits of galena and other lead ores contain some copper, gold, silver, and zinc. Nearly all lead ores are found underground. They are extracted using explosives and mechanical equipment.
After mining, the lead ore is processed by crushing. The crushed ore is then ground in water to a particle size less than 100 micrometers (0.1 millimeter). Grinding frees the particles of galena from the other mineral particles.
The particles are then separated in a process called froth flotation. In this process, surfaces of galena particles are chemically activated so that they can attach to air bubbles. The bubbles are passed through the water-and-mineral mixture that was produced by grinding. The bubbles carrying the attached galena particles rise to the surface. There, they form a froth or concentrate that contains 75 to 80 percent lead.
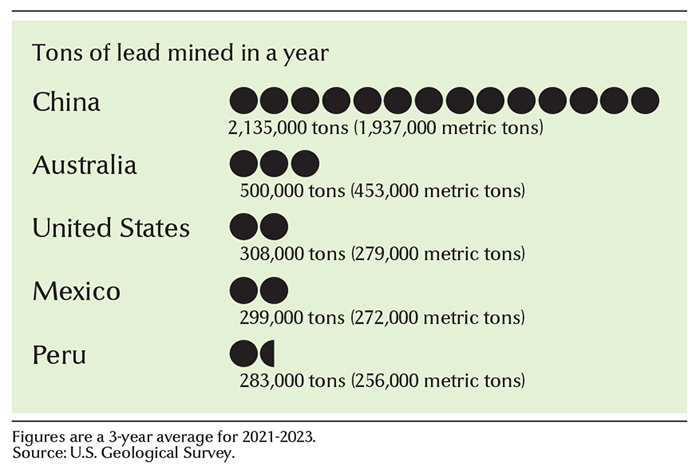
Next, the froth goes to a thickening tank. The solid particles settle to the bottom of the tank, forming a thick sludge. The sludge is then treated by a vacuum filter process. In this process, most of the water is sucked through a cloth, leaving a dry concentrate. The concentrate goes to a smelter for further processing. Zinc and copper metals can also be recovered in this fashion.
The unwanted minerals are discharged as a waste or tailings. The tailings are usually discarded into carefully controlled and monitored surface areas called tailing ponds. Sometimes, tailings are used to fill sections of the mine from which the ore was removed.
The lead sulfide concentrate is first sintered (fused by heating without melting) to burn off the sulfur. The sulfur combines with oxygen to escape as sulfur dioxide gas. This gas is typically converted into sulfuric acid. The lead in the concentrate also combines with oxygen to produce lead oxide in a porous form known as sinter.
The sinter is then smelted with carbon in a blast furnace. During smelting, air is blown into the furnace. The heat enables chemical reactions to occur, reducing the lead oxide to metallic lead. The lead metal is then tapped from the bottom of the blast furnace. Waste products, called slag, are tapped separately.
The crude lead metal produced in the blast furnace is called bullion. This metal contains impurities, such as copper, silver, and gold. In the refining process, these impurities are removed and saved for other uses. Several different refining processes are used. Typically, lead is refined by the control of temperature and the addition of zinc. These processes cause the impurities to float, as solids or liquids, on top of the dense, molten lead metal. The impurities can then be skimmed from the surface. The refined product that results is about 99.9 percent lead. Refined lead may be cast in large masses called ingots or in smaller masses called pigs. Ingots weigh 1 ton (0.9 metric ton). Pigs weigh 100 pounds (45 kilograms).
The recycling of lead has become important in many countries. Today, much of the lead used in the United States is recycled. The United States has limited reserves of lead ore. Unless additional reserves are found, recycling and importing will assume greater importance.