Automation is the use of machines to perform tasks that require decision making. Automation is used for a wide variety of jobs that are too complex or dangerous for people to do, for repetitive tasks that many people would find boring, and for work that would be extremely costly if done by people.
Uses of automation.
Automated systems can make decisions that are beyond the capacity of people to make. For example, many cities use automated systems to coordinate their lights to smooth the flow of traffic. Sensors in the pavement determine the number and speed of vehicles on the street and send the data to a computer. The computer decides how to time each traffic light in the area and sends signals to the traffic lights.
Automated systems can also make decisions more quickly than people can. For example, high-speed military aircraft sometimes fly at very low altitudes to avoid detection by enemy radar. To avoid hitting obstacles, these aircraft use automated guidance systems that can react much faster than a pilot can.
Repetitive, simple jobs can be boring for people to do for long periods of time. Automated machinery is well suited to these routine tasks, such as assembling, inspecting, and packaging manufactured products.
Automated machinery can operate in environments that are unsafe for people. Automated systems are used for repairing underwater pipelines at high pressures. Automobiles are painted by robots using spray paint that would harm people.
Automated systems can do some jobs more quickly and cheaply than people can. In many stores, checkout clerks use an optical scanner to read bar codes printed on product packaging. The scanner sends signals to the store’s computer, which relays price and product information to the cash register. The computer records the sale, keeping a tally of how much of each item remains in stock. It can even place orders to restock items. The use of automation also allows companies to save money they otherwise would have to spend to make hazardous work areas safe for human workers. In addition, a manufacturing robot may be able to perform different tasks by having its program changed, allowing one robot to do the work of several single-task machines.
How automation works.
An automated system has devices called sensors that pick up information about the results of the machine’s operation. Sensors may also sense certain environmental conditions that affect the machine’s performance. Information “read” by the sensors is fed directly back to the system, enabling the machine to adjust its operation as needed. Such a system of self-regulation is called feedback.
Feedback is what makes automation different from mechanization (the use of machinery to replace human workers or work animals). A mechanized industrial robot, for example, does not use feedback and therefore cannot adapt its operation to changing conditions.
The basic elements of feedback can be illustrated by an automated home heating system, which maintains a certain room temperature using input and output. The input is the thermostat setting—that is, the desired room temperature. The output is the actual temperature. The input tells the system what the output should be. An automated system needs sensors to measure output. The heating system’s sensor is a thermometer that measures room temperature. Sensors in other systems measure such variables as pressure, size, and weight.
Automated systems compare the actual output with the desired output through devices called comparators. In a heating system, the thermostat acts as the comparator. It compares the thermometer reading with the temperature for which the thermostat has been set. If the actual output of the system differs from the desired output, the comparator sends an error signal to a controller. The controller decides how to correct the error in output. The thermostat in a heating system functions as a controller as well as a comparator. In some feedback systems, the controller may be a computer.
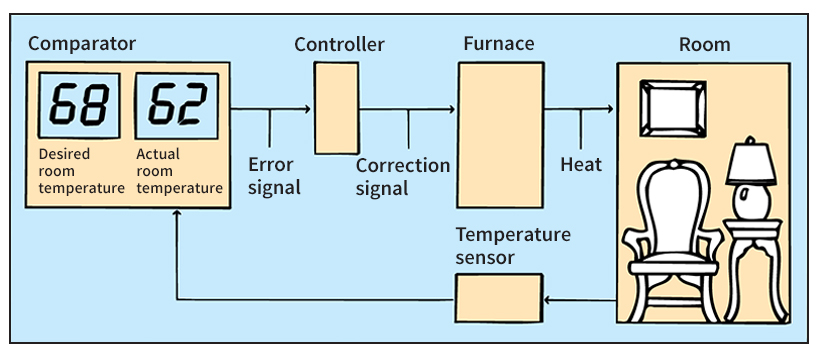
The part of any automated system that is controlled by feedback and changes the output is called the process. The controller directs the process to correct the output. In a home heating system, the process is the furnace. The thermostat switches the furnace on to raise the room temperature or shuts it off to lower the temperature.
History of automation.
The first industrial application of automation was a flyball governor, a device that regulated the speed of a steam engine. James Watt, a Scottish engineer, constructed this device in 1787.
In the 1900’s, automated controls were applied to many processes. Automated steering systems controlled by gyroscopes were first used in ships in the 1920’s and came into regular use in airplanes in the 1930’s (see Automatic flight control system (AFCS) ). Also at this time, the quality of telephone signals was improved by using amplifiers controlled by feedback. Automated controls used in chemical production and petroleum refining date from the early 1900’s. World War II (1939-1945) further stimulated the development of automation. Automatically aimed antiaircraft guns, using radar and electronics equipment, were introduced in 1944.
The first industrial robot was used in 1961. It was controlled by a computer and worked in an automobile assembly plant. Many robots are now used in the electronics industry and in the production of automobiles, airplanes, and heavy construction machinery. Since the late 1970’s, the use of computers to run machines has greatly stimulated development.
Automation and jobs.
Many people expect an increase in automation to cause unemployment as workers are replaced by machines. However, while the use of automation eliminates low-skill jobs, it increases the demand for highly skilled workers. Many skilled people are needed to design, build, and maintain automated systems. In addition, automation may enable manufacturers to lower prices and increase sales. As sales increase, employment may rise.