Cast and casting. Casting is a method of shaping an object by pouring a liquid into a mold and letting it become solid. The shaped object is called either a cast or a casting. Casting is used to make thousands of articles, including tools, machine parts, toys, and art objects such as statues. The Egyptians cast bronze in molds more than 3,500 years ago. Today, different iron, steel and aluminum alloys (mixtures) are used in casting, as are ceramics, plastics, and numerous other materials.
Patterns for casting.
Before materials are cast, workers make a wood, plastic, or metal pattern of the article to be cast. These patterns are later used to make the molds from which the actual castings are made. Patterns may be made in a number of ways, depending on the size of the article and on how many times the mold will be used. In most cases, the same pattern is used for production of multiple molds. It is designed to be removed from the mold cavity. A match-plate pattern is made by splitting the pattern in two halves. When the object is extremely large and when only a few pieces of the object will be needed, a loose pattern—that is, a solid or one-piece pattern, is used.
Types of molds.
Metal alloys can be cast in a mold used only once, or in a permanent mold used multiple times. A single use mold called a green sand mold is a packed mixture of sand, clay, and water. Dry sand molds are made with chemical binders and produce smoother casting surfaces. Permanent molds made from metal are used multiple times for special casting processes.
How castings are made.
Metal is often cast in a sand mold. If an object, such as an iron dumbbell, is to be cast from a split pattern, one half of the pattern is placed on a board, with its flat side down. The board is surrounded by two loose-fitting wooden or metal boxes. Together, these boxes make up a flask. Damp sand is packed firmly around the pattern to fill the space between the pattern and the sides of the flask. The board is removed, and the other half of the pattern is fitted to the first half. Sand is then packed around it.
The top half of the flask with its sand is called the cope. The bottom half is called the drag. The cope and the drag of the mold are fitted together after the pattern has been removed from the sand. A small opening called a gate is formed to each end of the cope so the metal can be poured into the mold. A cavity can be made in a casting by suspending a hard sand object called a core in the mold. When the metal is poured into the mold, it cools quickly and forms a solid. The sand is then broken away.
Other types of casting.
In centrifugal casting, molds are rotated rapidly while the metal is being poured. The centrifugal force of the rotation forces the metal to the inner surface of the mold. This process is used for pipe production.
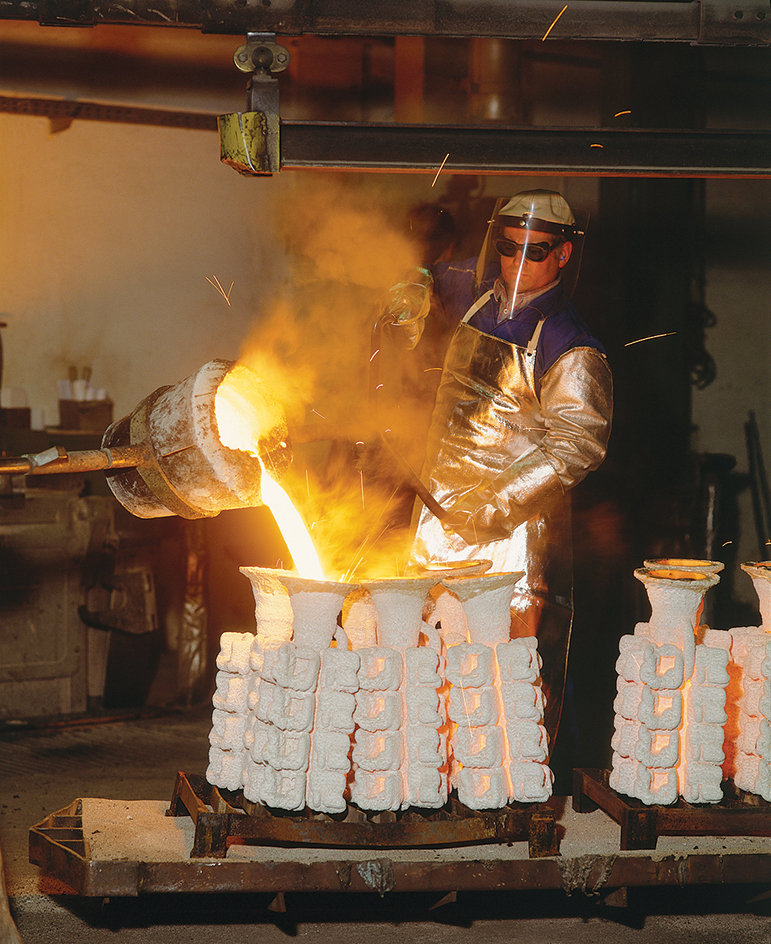
Two processes are used to make precision castings: (1) die casting, and (2) investment casting. In die casting, the melted metal is forced into a permanent metal mold called the die, and the castings are removed when they cool. A machine can perform the entire process. In investment casting, a ceramic slurry is applied around disposable wax patterns assembled in a cluster called a tree. Multiple layers of the ceramic coats are applied in a form called stucco. The wax patterns are melted with hot, high-pressure steam and removed. The ceramic mold is fired and can then be used for pouring.