Coal is a black or brown rock that can be ignited and burned. As coal burns, it produces useful energy in the form of heat. People use this heat to warm buildings and to make or process various products. Chemicals from coal are used to make dyes, fertilizer, pharmaceuticals, and other products. However, the main use of coal is the production of electric power. The heat from burning coal is used to make steam that drives engines called turbines in electric power plants. Coal-burning plants supply about 40 percent of the world’s electric power. Much coal is also used in making steel and cement. The countries of the world use about 9 1/2 billion tons (8.6 billion metric tons) of coal a year. China uses about half of this coal. India, Indonesia, and the United States are also top producers—and users—of coal.
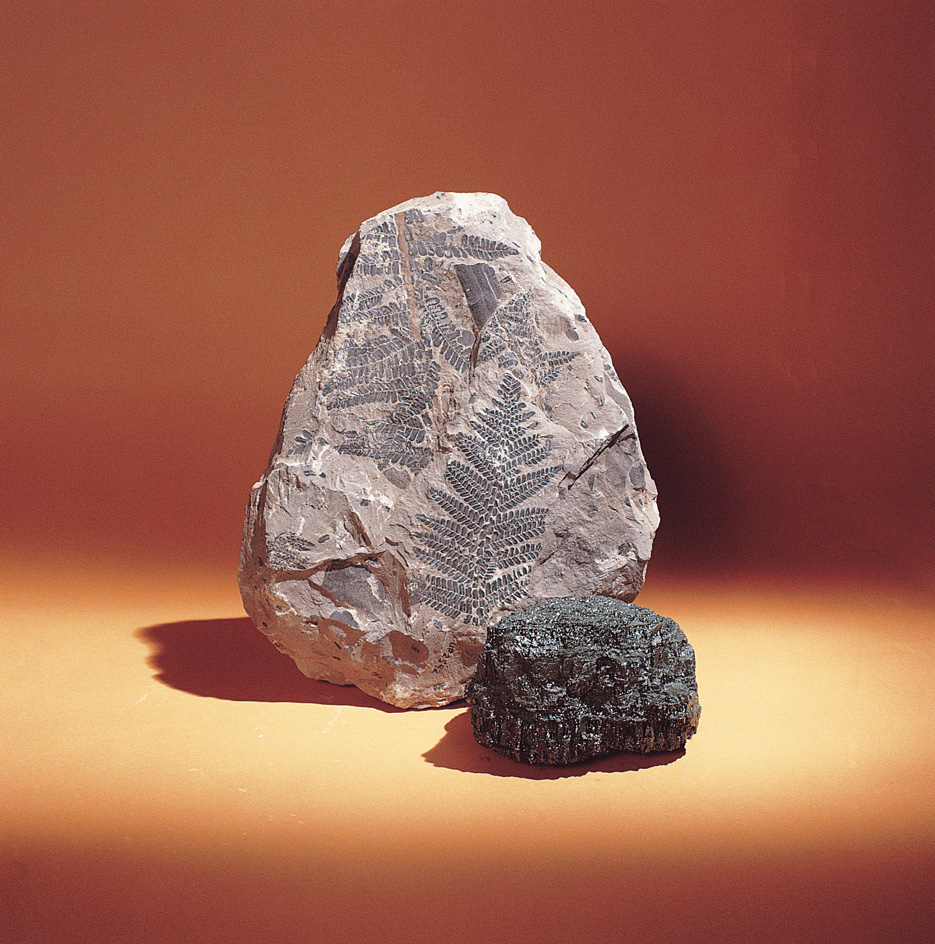
Coal formed over millions of years from partially decayed plant matter called peat. The chemical process that transforms peat to coal is called coalification. Coal consists primarily of the elements carbon, hydrogen, nitrogen, oxygen, and sulfur.
Coal was extremely important in fueling the Industrial Revolution, a period of rapid industrial development in the 1700’s and 1800’s. However, wood remained the principal fuel for many years. The change from wood to coal as the primary source of energy took place in different countries at different times, influenced by the availability and cost of these fuels. Some less developed countries still rely heavily on wood as their primary source of fuel. In much of the world, however, petroleum, natural gas, and coal have become the leading sources of energy.
People are rapidly using up the world’s supplies of petroleum and natural gas that can be removed from the earth economically. New drilling technologies have extended the supply of available oil and natural gas. But experts estimate these resources will not last much longer than a hundred years at present rates of use. The world’s supply of coal will likely last longer than other fossil fuels. But coal has long been a major cause of air pollution, and many people are concerned about the effects of coal combustion on the environment. Liquids derived from coal can substitute for gas or oil as transportation fuels. But such fuels are costly to produce.
In the past, few jobs were harder or more dangerous than that of an underground coal miner. During the 1800’s, many miners had to work underground 10 or more hours a day, six days a week. Picks were almost the only equipment they had to break the coal loose. The miners shoveled the coal into wagons. In many cases, children as young as 10 years of age hauled the coal from the mines. Women worked as loaders and haulers. Over the years, thousands of men, women, and children were killed in mine accidents. Thousands more died of lung diseases from breathing coal dust.
Today, in industrialized countries, machines do most of the work in coal mines. Mine safety has been improved, work hours have been shortened, and child labor is prohibited. However, coal mining is still dangerous and poorly regulated in many of the less developed regions of the world.
This article discusses the composition of coal, the uses of coal, how coal was formed, where coal is found, and how it is mined. It also discusses the cleaning and shipping of coal, the coal industry, and the history of the use of coal.
The composition of coal
Coal is referred to as a fossil fuel because it formed from the remains of living things. Petroleum and natural gas are also fossil fuels. The composition of coal varies more than that of oil or gas. It varies from one coal seam (deposit) to another, and even within an individual seam.
Coal is a sedimentary rock that formed when sediments (loose pieces of minerals and rock) and plant remains settled to the bottom of bodies of water and hardened. It is often referred to as a mineral. But unlike a true mineral, coal has no fixed chemical formula. By weight, it contains at least 50 percent organic matter and no more than 50 percent inorganic matter. The principal chemical elements in coal are carbon, hydrogen, nitrogen, oxygen, and sulfur—elements found in all living organisms. Much of the hydrogen and carbon are combined in molecules called hydrocarbons, which give coal its ability to burn and produce useful heat. The inorganic matter, or mineral matter, in coal commonly includes calcite, clay, marcasite, pyrite, and quartz. When coal is burned, the minerals become ash, a powderlike residue. The coal industry refers to ash-producing substances in coal as “ash” even before the coal is burned.
Other components of coal are known as major elements, minor elements, and trace elements. They occur in small quantities primarily in the mineral matter. The major elements include aluminum, calcium, iron, and silicon. Minor elements may include chlorine, magnesium, potassium, sodium, and titanium. The trace elements include arsenic, lead, mercury, and selenium. The trace elements occur in extremely small amounts—usually measured in parts per thousand, parts per million, or parts per billion.
Coal also contains moisture and gases that accumulate in its pores and that stick to the coal itself. The gases are mainly carbon dioxide and the hydrocarbon methane.
Occasionally, a mineral called calcium carbonate—dissolved in water—seeps into peat and saturates it. Such peat, called petrified peat, preserves many parts of its original plants. Compacted and coalified petrified peat occurs in coal seams in the form of coal balls.
How composition affects value.
The composition of coal is important in determining the coal’s suitability for certain applications. It also determines the value of coal in the marketplace. Heating value, sulfur content, moisture content, and ash are measured when grading coal for commercial purposes. Heating value refers to the amount of heat that is produced by a given amount of coal when it is burned. It is usually reported in British thermal units (Btu’s) per pound or in kilojoules per kilogram. A Btu is equal to 251.996 calories or 1,054.35 joules. In general, the higher the heating value, the more valuable the coal. Moisture and ash tend to reduce the value of coal, because moisture reduces heating value and ash may contain substances that corrode boilers or equipment, or build up inside them. It is also costly to dispose of ash. Government regulations in the United States and other countries control sulfur emissions from coal burning. For this reason, higher sulfur content may also render a coal less valuable.
Analyzing coal composition.
Coal scientists use a variety of tests to measure the quantities of the components of coal to judge its suitability and value. The most basic tests are two types of chemical analysis—proximate analysis and ultimate analysis. Proximate analysis indicates the quantity of ash, moisture, volatile matter, and fixed-carbon in a coal sample. Volatile matter is material, other than moisture, that is given off when coal is heated to a specific high temperature in the absence of oxygen. The remaining solid material contains fixed-carbon, which will burn if heated in the presence of oxygen, and ash, which will not burn. Proximate analysis is a basic test to judge coal quality. Scientists use ultimate analysis, also called elemental analysis, to determine the amounts of carbon, hydrogen, oxygen, nitrogen, and sulfur in a sample of coal. Using the results of this analysis, they can calculate the heating value of the coal in the sample.
Some scientists use coal petrography, the observation of coal under a microscope, to study composition. For example, they may examine a polished pellet of finely ground coal under high magnification to observe structures in the organic material of coal. These structures, called macerals, are the “building blocks” of coal. There are three basic groups of macerals: (1) vitrinites, (2) liptinites, also called exinites, and (3) inertinites. Vitrinites developed from woody plant tissues; liptinites, from algae, spores, and the resinous and waxy parts of plants; and inertinites, from charred and decomposed plant material. Scientists may also view a thin slice of coal called a thin section under a high-magnification microscope. Such observation reveals many details about the organic and inorganic makeup of the coal.
Study of the mineral matter in coal helps scientists identify pollutants and predict how the ash will behave during combustion. Ash can foul furnaces, leading to damage and costly repairs. Laboratory scientists must carefully identify and measure the mineral in coal. They use such tools of physics as electron microscopy and X-ray diffraction to perform this work (see Diffraction (Uses of diffraction); Electron microscope). The trace elements in coal can pollute the air or foul or corrode equipment during combustion. Geologists chemically test coal before it is used, to identify and measure the quantities of these elements.
In another method of analysis, powdered coal is placed in a strong acid or alkali solution. Much of the coal dissolves, leaving a residue of microscopic fossilized pollen and spores that survived the coalification process. These fossils are valuable in identifying types of plants and geological periods associated with the coal.
Coal rank.
Coal is usually assigned a rank based on how much the organic matter was altered during coalification. As rank increases, the carbon content and heating value of the coal also increases. The four ranks of coal, from the lowest to the highest, are (1) lignites, or brown coals; (2) subbituminous coals; (3) bituminous coals; and (4) anthracites. The lowest-ranking lignites have a carbon content of only about 30 percent. The highest-ranking anthracites contain about 98 percent carbon. Many properties of coal change with rank.
The uses of coal
Coal as a fuel.
Coal is a useful fuel because it is abundant and has a relatively high heating value. Sulfur, a major impurity in coal, limits coal’s usefulness as a fuel. Most of the sulfur in burning coal combines with oxygen and forms a gas called sulfur dioxide, which contributes to air pollution. To prevent serious air pollution, the burning of medium- and high-sulfur coals in a power plant requires scrubbers, pollution control devices that absorb sulfur dioxide fumes as they pass through the plant’s smokestacks. Other air pollutants in coal include various forms of nitrogen oxides, mercury, and extremely fine particulate matter. Widely used control technologies can prevent the emission of almost all of these pollutants. However, burning coal also produces carbon dioxide, a greenhouse gas that contributes to global warming. Greenhouse gases trap heat near Earth’s surface. Global warming is an observed rise in Earth’s average temperature. Technologies to capture carbon dioxide from coal plants are expensive and rarely used.
Different systems are used in different countries to classify coal by sulfur content. The system used by the U.S. Environmental Protection Agency (EPA) classifies coal according to the weight of sulfur in a sample that can produce 1 million Btu’s of heat. Such a sample is low-sulfur coal if it produces 0.60 pound (0.272 kilogram) or less of sulfur, medium-sulfur coal if its sulfur content is 0.61 to 1.67 pounds (0.277 to 0.757 kilogram), and high-sulfur coal if it produces 1.68 pounds (0.762 kilogram) or more of sulfur.
Some of the ash produced by burning pulverized coal may escape into the air. This so-called fly ash also contributes to air pollution. Devices called electrostatic precipitators can trap fly ash in the power plant before it escapes into the air. In some regions, the amount of fly ash and other particles from power plants is strictly monitored and regulated to reduce air pollution.
Electric power production.
Most electric power plants fueled by coal are steam-turbine plants. They use high-pressure steam to generate electric power. The steam turns the fanlike blades of turbines, which drive the generators that produce electric power. See Electric generator; Electric power; Turbine.
Bituminous coal is the preferred fuel for electric power production in many countries, including the United States, because it is plentiful and has a high heating value. However, much bituminous coal has medium or high sulfur content. In many countries, more and more power plants are burning at least some low-sulfur subbituminous coal and lignite to meet government air pollution standards. These coals must be handled carefully because they are more likely than other types to ignite spontaneously in stockpiles, freeze in railcars, and dry out, break up, and produce much coal dust. Modern handling techniques have improved control over these problems.
Other uses of coal as a fuel.
In parts of Asia and Europe, coal is widely used for heating homes and other buildings. In the United States and many other countries, natural gas and fuel oil have almost entirely replaced coal as a domestic heating fuel. However, the price of oil and natural gas has caused some factories and other commercial buildings to turn to coal. Anthracite is the cleanest-burning coal, but it is expensive and in limited supply. And subbituminous coals and lignites have such a low heating value that large amounts must be burned to heat effectively. Thus, bituminous coals are the kinds most widely used for domestic heating.
In the past, coal provided heat for the manufacture of a wide variety of products, including glass and canned foods. Since the early 1900’s, manufacturers in many parts of the world have come to use natural gas in making most of these products. Coal is used mainly by the steel and cement industries. But some other industries have switched back to coal to reduce fuel costs.
Coal as a raw material.
Many substances made from coal serve as raw materials in manufacturing. Coke—a hard, foamlike mass of nearly pure carbon—is the most widely used of these substances. It is made by heating bituminous coal to about 2000 °F (1100 °C) in an airtight oven. The lack of oxygen prevents the coal from burning. The heat changes some of the coal into gases. The remaining solid matter is coke. It takes about 11/2 tons (1.4 metric tons) of bituminous coal to produce 1 ton (0.9 metric ton) of coke. For an illustration of the coke-making process, see Coke .
The coal used to make coke is called coking coal. It requires specific characteristics, such as low sulfur and ash content. Only certain types of bituminous coals have all the necessary characteristics.
Coke is used primarily to make iron and steel. Most coking plants are a part of steel mills. The mills burn coke with iron ore and limestone to change the ore into the pig iron required to make steel. It takes about 900 pounds (400 kilograms) of coke to produce 1 ton (0.9 metric ton) of pig iron. For a description of the role of coke in iron production, see Iron and steel (How iron is made).
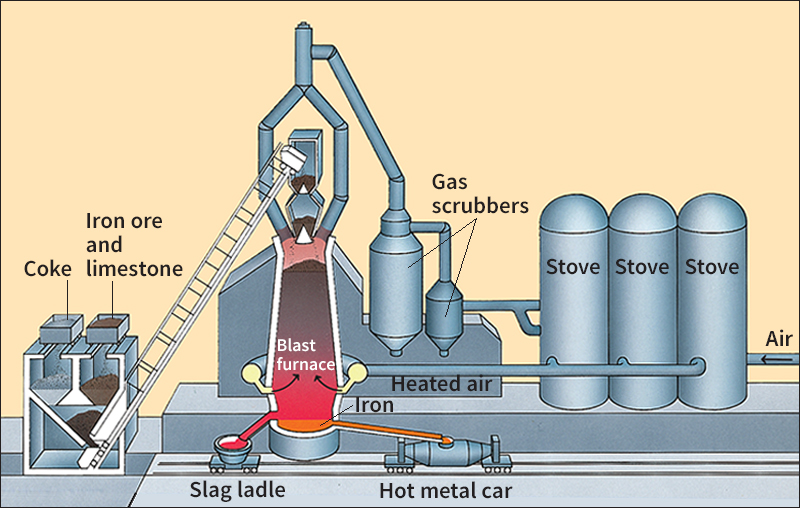
The coke-making process is called carbonization. Some of the gases produced during carbonization turn into liquid ammonia and coal tar as they cool. Through further processing, some of the remaining gases change into light oil. Manufacturers use the ammonia, coal tar, and light oil to make such products as dyes, fertilizers, and pharmaceuticals. Coal tar is also used for roofing and for road surfacing.
Some of the gas produced during carbonization does not become liquid. This coal gas, or coke oven gas, burns like natural gas. But coal gas has a lower heating value and, unlike natural gas, gives off large amounts of soot as it burns. Coal gas is used chiefly at the plants in which it is produced. Coal gas provides heat for the coke-making and steel-making processes.
Gas can be produced from coal directly, without carbonization, by various gasification methods. The simplest such method involves burning coal in the presence of forced air or steam. The resulting gas, like coke oven gas, has a low heating value and produces soot. It is used chiefly in certain manufacturing processes. Coal can be used to make high-energy gas, gasoline, and fuel oil. But the present methods of producing these fuels from coal are costly and complex. The section “The coal industry” discusses how researchers are working to develop cheaper and simpler methods.
Coal combustion products
are coal components that remain after burning. Such products, including ash, scrubber sludge, and other materials, were once considered waste materials. They were often expensive to handle and took up valuable space in landfills. Today, millions of tons of these products are sold in the world each year. They are used to make asphalt, cement and concrete, road materials, soil stabilizers, wallboard, and other products. Industries that make these items often build facilities near power plants so that they can use the materials generated by coal combustion.
How coal was formed
The formation of coal is a geologic process that takes millions of years. It begins with the accumulation of dead plant material under extremely wet conditions. The ideal setting is a humid swamp. There, constant rainfall and a high water table keep the plant material water-logged, limiting normal decay. Under those conditions, thick deposits of dead plant material can build up. The partial decay of plant material produces peat.
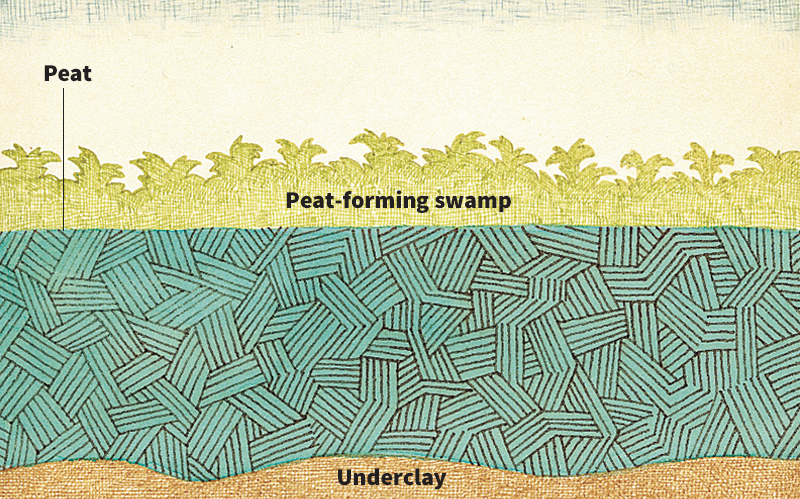
The next step in the formation of coal is for the land surface upon which peat accumulates to gradually sink. Such sediments as sand and mud bury the peat as the surface sinks. The buried peat is preserved from decay and erosion, and so it can be transformed into coal.
The last step, coalification, changes peat by concentrating carbon and hydrogen and expelling such by-products as carbon dioxide, methane, and water. The rate at which peat changes to coal depends on temperature and pressure. Higher temperatures and pressures result in faster coalification. Lower temperatures and pressures produce slower coalification.
The interior of Earth is hot, and heat flows constantly from the interior to Earth’s surface. Temperatures at the boiling point of water, 212 °F (100 °C), are found a few thousand feet or meters beneath the surface. This temperature is high enough to cause the transformation of peat to coal over a long time. It generally takes from 3 to 10 feet of peat to produce a 1-foot thickness of coal, or 3 to 10 meters of peat to produce 1 meter of coal.
Much coal formed during the Carboniferous Period, from about 360 million to 300 million years ago. Coal formed during this period is found in North America, Europe, and Asia. Various trees grew in Carboniferous swamps and produced huge amounts of peat-forming matter after they died. Another important time for the formation of coal ranged from the Cretaceous Period to the Miocene Epoch, from about 145 million to 23 million years ago. The thick subbituminous coals of the Powder River Basin in Wyoming and Montana and the lignite coal of the U.S. Gulf Coast were formed during this period. The swamps that formed these coals had plants similar to modern cypress and tupelo trees.
Peat is accumulating on Earth today in conditions similar to those that produced coal. High-quality peat deposits as thick as 50 feet (15 meters) occur in the swamps of Indonesia. These deposits cover thousands of square miles or square kilometers, and receive 5 to 10 feet (1.5 to 3 meters) of rainfall each year. This peat could eventually develop into coal, but the process could take as long as 1 million years.
The coal seams, or coal beds, mined today range in thickness from a few inches or centimeters to more than 400 feet (120 meters). The thickest seams are of subbituminous coal and lignite. Many coal deposits consist of two or more seams separated by layers of rock. These formations were produced as new coal-forming swamps developed over buried ones. Each new swamp became buried and developed into a separate seam.
Most coal beds lie nearly parallel to Earth’s surface. But some have been tilted by movements of underground rock layers and lie at an angle to the surface. Most of the deepest beds consist of anthracites or bituminous coals. Over a long period, geologic forces can push coal upward from deep beneath the surface. In addition, erosion can expose coal at the surface.
Where coal is found
Coal is found on every continent. Deposits occur as far north as the Arctic and as far south as Antarctica. Some coal deposits occur off ocean coastlines. However, underwater deposits are not considered valuable because they are difficult to mine.
Coal is typically found in bowl-shaped geologic features known as coal basins or sedimentary basins. Coal basins vary greatly in size, depth, age, number, and thickness of seams. The Appalachian Basin in the eastern United States, for example, is about 1,000 miles (1,600 kilometers) long and 150 miles (240 kilometers) wide. Its coal seams range from outcroppings that occur at the surface to seams that reach depths exceeding 5,000 feet (1,500 meters). The quality and rank of the coal varies within a coal basin.
Coal deposits that can be mined profitably are called coal reserves. In most cases, a coal seam must be at least 24 inches (61 centimeters) thick for mining engineers to class it as a reserve. Most estimates of coal reserves include only tested deposits.
Estimating coal reserves.
To estimate coal reserves, mining engineers drill into the ground in suspected coal-bearing areas. Using a special drill bit, they cut cylindrical samples of sediment and rock called cores. After a drill cuts through a coal seam, geologists and engineers can use the resulting cores to determine the depth and thickness of the seam. Laboratory scientists can analyze core samples to determine the coal’s composition and suitability for use.
Mining engineers use a formula based on coal rank and quality to calculate the tons of coal reserves beneath a given land area. According to the formula used for bituminous coal, for example, a bed yields about 1,800 tons for each foot of coal thickness per acre, or about 13,000 metric tons per meter of thickness per hectare. By drilling a number of test holes, and applying the proper formula, geologists and engineers can estimate the size and potential value of a particular deposit. A large area of tested reserves is called a coal field.
The world’s coal reserves.
No complete estimate exists for the total amount of coal that lies beneath Earth’s surface. The world’s proved recoverable reserves of coal total about 1 trillion tons (0.9 trillion metric tons). This figure represents the amount of coal that can be recovered from known deposits with current technology. The major proved recoverable reserves are in Australia, China, Germany, India, Kazakhstan, Russia, South Africa, Ukraine, and the United States. Australia, China, and Russia have large deposits of bituminous, subbituminous, and lignite coals. Australia’s largest deposits lie in the eastern part of the country. Central China has that country’s largest deposits. Russia’s main deposits lie in the central and western parts of the country. South Africa has large deposits of bituminous coal in the northeastern part of the country.
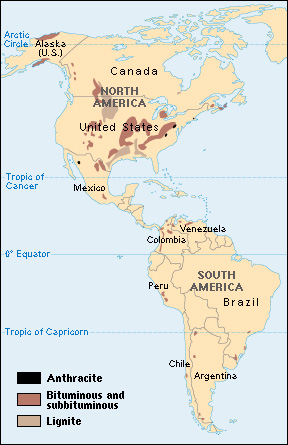
About half of all U.S. coal reserves lie in the eastern half of the nation, from the Appalachian Highlands to the eastern edge of the Great Plains. The rest are in the western part of the country, especially in the Rocky Mountain States and the northern Great Plains. Many geologists believe that Alaska may have huge coal reserves. But the state’s potential reserves have not been fully assessed. The reserves in the eastern United States include nearly all the nation’s anthracite deposits and most of its bituminous coal deposits. The western reserves include almost all the subbituminous coal and lignite. Canada’s coal reserves consist chiefly of bituminous coal in western Canada. Canada also possesses large deposits of subbituminous coal and lignite. The largest coal reserves are in Alberta and British Columbia.
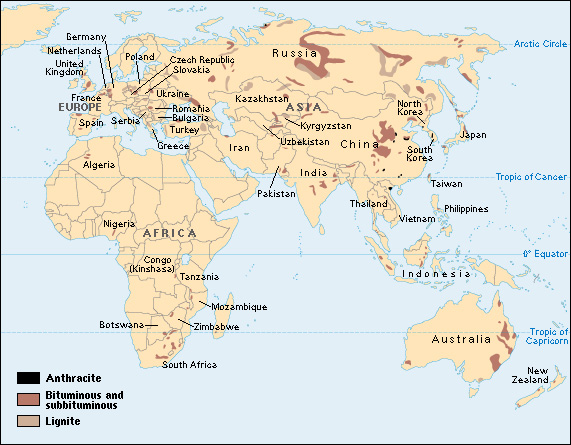
Surface mining
About 40 percent of the coal mined in the world, and about 65 percent of the coal mined in the United States, comes from surface mines. Surface mining involves removing the overburden, the soil and rock that lie over a coal deposit. After this material has been removed, the coal can easily be dug up and hauled away. Surface mining is usually limited to deposits within 100 to 200 feet (30 to 60 meters) of the surface. The more overburden that must be removed, the more difficult and costly surface mining becomes.
Nearly all surface mining is strip mining—that is, mining by first stripping away the overburden. Many coal seams are exposed on the sides of hills or mountains. In some cases, these seams can be mined without removing any overburden. Miners use machines called augers to dig out the coal. This method of surface mining is known as auger mining.
Surface mining requires fewer miners than does underground mining. Strip miners are chiefly heavy-machine operators. Unlike underground miners, they have little need for traditional mining skills.
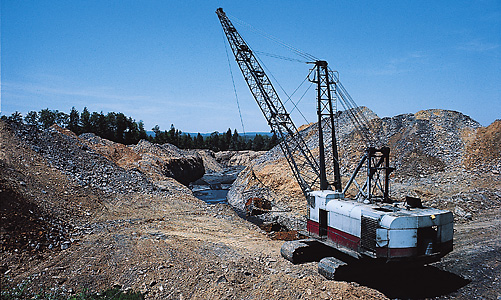
Strip mining
depends on powerful machines that dig up the overburden and pile it out of the line of work. The dug-up overburden is called spoil. In time, a strip mine and its spoil may cover an enormous area. The digging up of vast areas of land has raised serious environmental concerns. As a result, some governments require that all new strip-mined land be reclaimed—that is, returned as close as possible to its original condition. Strip mining thus involves methods of (1) mining the coal and (2) reclaiming the land.
Mining the coal.
Most strip mines follow the same basic steps to produce coal. First, bulldozers or loaders clear and level the vegetation and soil above the mining area. Many small holes are then drilled through the rocky overburden to the coal bed. Each hole is loaded with explosives. The explosives are set off, shattering the rock in the overburden. Giant power shovels or other earthmoving machines then clear away the broken rock. Some of these earth movers are as tall as a 20-story building and can remove more than 3,500 tons (3,200 metric tons) of overburden per hour. After a fairly large area of coal is exposed, explosives may be used to loosen the coal itself. Coal-digging machines then scoop up the coal and load it into trucks. The trucks carry the coal from the mine.
Although most strip mines follow the same basic steps, strip-mining methods vary according to whether the land is flat or hilly. Strip mining can thus be classed as either (1) area mining or (2) contour mining. Area mining is practiced where the land is fairly level. Contour mining is practiced in hilly or mountainous country. It involves mining on the contour—that is, around hillsides.
In area mining, an earthmover digs up all the broken overburden from a long, narrow strip of land along the edge of the coal field. The resulting deep ditch is referred to as a cut. As the earthmover digs the cut, it piles the spoils along the side of the cut that is away from the mining area. The spoil pile forms a ridge called a spoil bank. After the cut is completed, the coal is dug, loaded into trucks, and hauled away. The earthmover then digs an identical cut alongside the first one. It piles the spoils from this cut into the first cut. This process is repeated over and over across the width of the coal field until all of the coal has been mined. The spoil banks form a series of long, parallel ridges on the land that can later be leveled.
If a coal seam lies near the top of a hill, an earthmover may simply remove the hilltop and so expose the coal. This type of mining is called mountain top removal. It is practiced primarily in the eastern United States. It can be efficient because it may enable the removal of several coal seams at once. Some people oppose its use because it produces dramatic changes to the landscape.
In contour mining, an earthmover removes the overburden immediately above the point where a seam outcrops (is exposed) all around a hill. The resulting cut forms a wide ledge on the hillside. The spoils may be stored temporarily on the hillside or used to fill in the cuts. After the exposed coal has been mined and hauled away, the earthmover may advance up the slope and dig another cut immediately above the first one. But the depth of the overburden increases sharply with the rise of the slope. After one or two cuts, the overburden may be too great for a coal company to remove profitably. If the seam is thick enough, a company may create an underground mine to remove the rest of the coal. Workers may also use other surface mining techniques—auger mining or highwall mining—to recover as much coal as possible without removing any overburden.
Reclaiming the land.
The chief environmental problems that strip mining can cause result from burying fertile soil under piles of rock. The rocks tend to give off acids when exposed to moisture. Rainwater runs down the bare slopes, carrying acids and mud with it. The runoff from the slopes may wash away fertile soil in surrounding areas and pollute streams and rivers with acids and mud.
The first step in reclaiming strip-mined land is to scrape and preserve the topsoil from the area to be mined. Topsoil is roughly 4 to 10 inches (10 to 25 centimeters) deep. This step must be done before strip mining starts. After mining is completed, the spoil banks created by area mining can be leveled by bulldozing. The spoils from contour mining can be used to fill in the cuts in the hillsides. As much topsoil as possible should then be returned to its original position so that the area can be replanted. Much reclaimed land is turned into farms or recreation areas.
Auger mining
is another surface mining technique. A coal auger is shaped like an enormous corkscrew. It bores into the side of a coal outcrop on a slope and twists out the coal in chunks. Contour mines often use augers when the overburden in a slope is too great to remove. An auger can penetrate the outcrop and recover coal that could not otherwise be mined. Some augers can bore 200 feet (60 meters) or more into a hillside.
Highwall mining
is a new application similar to augur mining. Instead of drilling with an augur, workers use machines called continuous miners to dig parallel tunnels into the slope. The tunnels may extend 1,000 feet (300 meters). The machines are operated remotely. Thus, highwall mining is still considered surface mining, since no workers actually enter the tunnels.
Underground mining
Underground mining involves digging tunnels into a coal deposit. Miners must go into the tunnels to remove the coal. Most coal deposits deeper than 200 feet (60 meters) are mined underground. Underground mining is more hazardous to workers than surface mining. The miners may be injured or killed by cave-ins, falling rocks, explosions, and poisonous gases. To prevent such disasters, every step in underground coal mining must be designed to safeguard the workers.
Underground mining generally requires more human labor than surface mining does. But even so, underground mines are highly mechanized. Machines do all the digging, loading, and hauling in nearly all the mines. In industrialized nations, few mines are nonmechanized.
In most cases, miners begin an underground mine by digging two access passages from the surface to the coal bed. One passage will serve as an entrance and exit for the miners and their equipment. The other will be used to haul out the coal. Both passages will also serve to circulate air in and out of the mine. As the mining progresses, the workers dig tunnels from the access passages into the coal seam.
Underground mines can be divided into three main groups according to the angle at which the access passages are dug into the ground. The three groups are (1) shaft mines, (2) slope mines, and (3) drift mines. Some mines have two or all three types of passages.
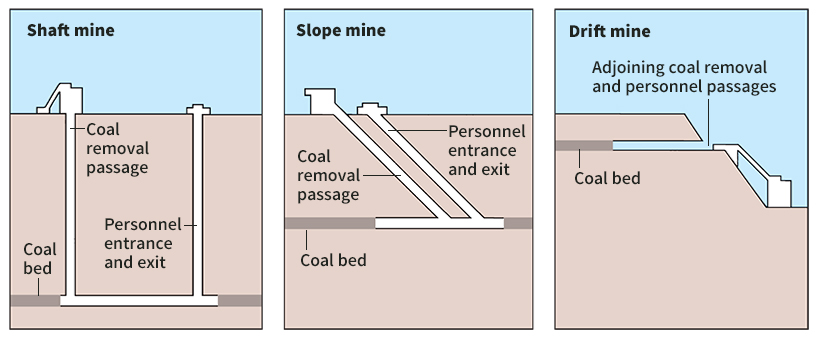
In a shaft mine, the access passages run straight down from the surface to the coal seam. The entrance and exit shaft must have a hoist. Most mines under more than 700 feet (210 meters) of cover are shaft mines. In a slope mine, the access passages are dug on a slant. They may follow a slanting seam or slant down through the cover to reach the seam. Drift mines are used to mine seams of coal that outcrop in hills or mountains. The access passages for these mines are dug into a seam where the coal bed outcrops on a slope.
Two main systems of underground mining are used: (1) the room-and-pillar system and (2) the longwall system. Each system has its own set of mining techniques. Either system may be used in a shaft, slope, or drift mine. The room-and-pillar system is by far the more common system of underground mining in the United States. The longwall system is more widely used elsewhere, especially in European countries.
The room-and-pillar system
involves initially leaving pillars of coal standing in a mine to support the overburden. Miners may begin a room-and-pillar mine by digging three or more long, parallel tunnels into the coal seam from the access passages. These tunnels are called main entries. In most cases, the ribs (walls) of coal separating the main entries are 40 to 80 feet (12 to 24 meters) wide. Cuts are made through each wall every 40 to 80 feet. The cuts form square or rectangular pillars of coal that measure 40 to 80 feet on each side. The coal dug in building the entries is hauled to the surface.
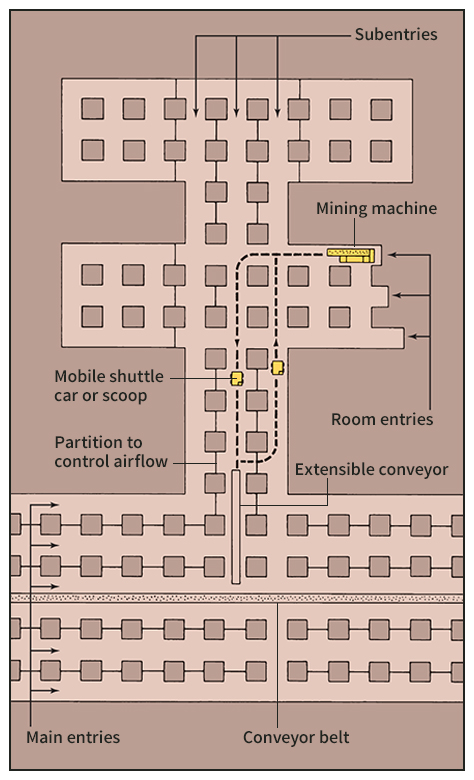
The pillars help support the overburden in the main entries. But in addition, the entry roofs must be bolted to hold them in place. To bolt the roof, the miners first drill holes 3 to 6 feet (0.9 to 1.8 meters) or more into the roof. They then anchor a long metal bolt into each hole and fasten the free end of each bolt to the roof. The bolts bind together the separate layers of rock just above the roof to help prevent them from falling. The miners must also support the roof in all other parts of the mine as those parts are developed. For safety, miners can only work under a supported roof.
A conveyor belt or a railroad track is built in one of the main entries to carry the coal to the access passages. A railroad may also transport the miners along the main entries. At least two main entries serve chiefly to circulate air through the mine. The mine may also need such facilities as water drainage ditches, gas drainage pipes, compressed air pipes, water pipes, and electric power cables. These facilities are built into the main entries and later extended to other parts of the mine.
After the main entries have been constructed, the miners dig sets of subentries at right angles from the main entries into the coal seam. Each set of subentries consists of three or more parallel tunnels, which serve the same purposes as the main entries. Cuts are made through the walls separating these tunnels, forming pillars like those between the main entries. At various points along each set of subentries, the miners dig room entries at right angles into the seam. They then begin to dig rooms into the seam from the room entries.
As the miners enlarge a room, they leave pillars of coal to support the overburden. A room is mined only a certain distance into the seam. When this distance is reached, the miners may remove the pillars. The room roof collapses as the pillars are removed, and so they must be removed in retreat—that is, from the back of the room toward the front. The miners’ exit from the room thus remains open as the roof falls. Pillars are also sometimes removed from entries. Like room pillars, they must only be removed in retreat to protect the miners.
All room-and-pillar mining involves leaving some pillars in place. Room-and-pillar mines differ, however, in their mining methods. Mechanized room-and-pillar mines use two main methods: (1) continuous mining, and (2) the conventional mechanized method.
Continuous mining
uses machines called continuous miners to gouge the coal from the coal face, the coal exposed on the surface of a wall. One worker operating a continuous miner can produce about 2 tons (1.8 metric tons) of coal per hour. The machine automatically loads the coal onto shuttle cars or a conveyor belt, which carries it to the railroad or conveyor in the main entries.
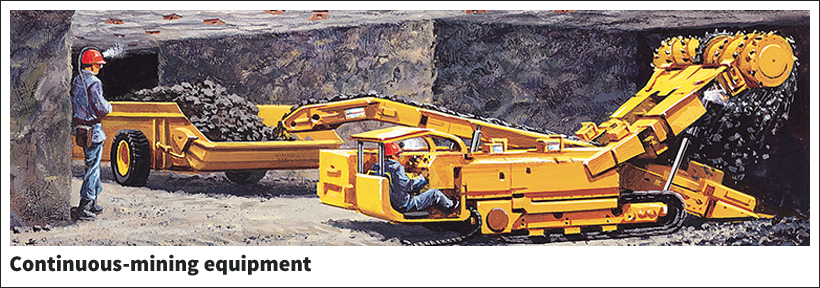
A continuous miner can usually dig and load coal much faster than the coal can be hauled out of a mine. The machine can work faster than the haulage, roof-bolting, ventilation, construction, and drainage systems can be completed. As a result, a continuous miner must frequently be stopped to allow the other mine systems to catch up.
The conventional mechanized method
was more widely practiced during the 1930’s and 1940’s than it is today. During the 1930’s, it largely replaced the earlier method of digging coal by hand. Since about 1950, continuous mining has increasingly replaced the conventional method.
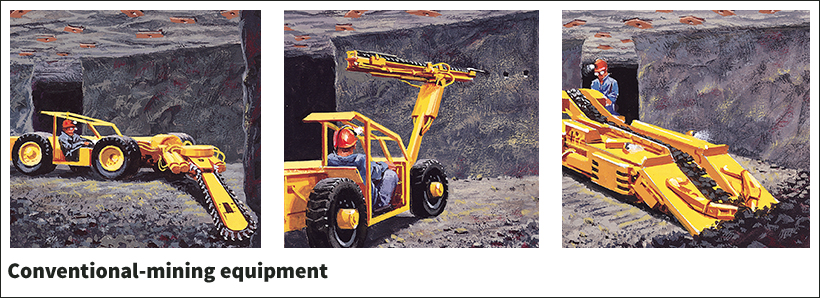
The conventional mechanized method involves five steps: (1) A machine that resembles a chain saw cuts a long, deep slit, usually along the base of the coal face. (2) Another machine drills a number of holes into the face. (3) Each hole is loaded with explosives. The explosives are set off, shattering the coal. The deep slit along the base causes the broken coal to fall to the floor. (4) A machine loads the coal onto shuttle cars, scoops, or a conveyor. (5) Miners bolt the roof exposed by the blast.
A separate crew of miners carries out each of the five steps. After a crew has completed its job on a particular face, the next crew moves in. The miners can thus work five faces of coal at a time. But there are frequent pauses in production as the crews change places.
The longwall system
of underground mining involves digging main tunnels or entries like those in a room-and-pillar mine. However, the coal is mined from one long face, called a longwall, rather than from many short faces in a number of rooms.
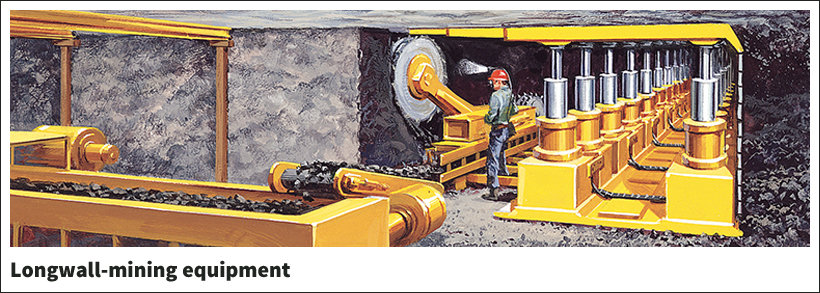
A longwall face is about 300 to 700 feet (90 to 210 meters) long. The miners move a powerful cutting machine back and forth across the face, plowing or shearing off the coal. The coal falls onto a conveyor belt. Movable steel props support the roof over the length of the immediate work area. As the miners work the machine farther into the seam, the roof supporters are advanced. The roof behind the miners is allowed to fall. After a face has been dug out 4,000 to 6,000 feet (1,200 to 1,800 meters) into the seam, a new face is developed and mined. This process is repeated until as much coal as possible has been removed from the seam.
The longwall system originated in Europe. Underground mines in Europe are much deeper, on the average, than those in the United States. The pressure of the overburden becomes intense in an extremely deep mine. Longwall mining relieves the pressure by allowing the roof to cave in throughout most of a mine. In a European longwall mine, the roof remains in place only over the main entries, over the longwall face, and over two tunnels leading to the face. The mines can thus recover up to 90 percent of the coal in a seam.
Mine safety laws in some countries, including the United States, require longwall mines to have fully developed subentries as well as main entries. Such longwall mines include some of the main features of room-and-pillar mines. One kind of longwall mining is called the retreating longwall system. This type of mining uses the room-and-pillar system to reach and expose the long coal face. Longwall equipment then mines the coal. These mines are much more productive than room-and-pillar mines because less coal is left in place.
Some mines have adopted a variation of the longwall method called shortwall mining. A shortwall face is only about 150 to 200 feet (45 to 60 meters) long, and it is mined with continuous-mining machines rather than with longwall equipment. This system, which was developed in Australia, is suited to coal seams whose structure prevents them from being divided into long faces.
Cleaning and shipping coal
Some coal is shipped to buyers exactly as it comes from the mine, without any processing. In the coal industry, such coal is called run-of-mine coal. It ranges in size from fine particles to large chunks.
The two largest users of coal, the electric power and coking industries, have definite quality requirements for the coal they buy. Much run-of-mine coal does not meet these requirements because it is the incorrect size or contains unacceptable amounts of impurities. As a result, mining companies sort their coal according to size. They also clean the coal to remove impurities.
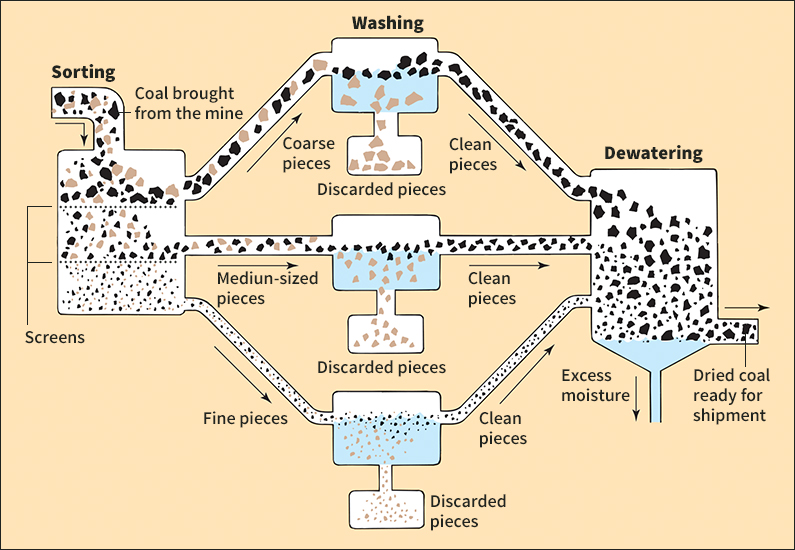
Cleaning coal.
Mining companies clean impurities from coal in preparation plants. Most large coal mines have a preparation plant on the mine property. Machines and other equipment are used to remove the impurities. They perform work referred to as coal processing, beneficiation, coal preparation, or coal cleaning.
Ash and sulfur are the chief impurities in coal. Run-of-mine coal may also contain pieces of rock or clay. These materials must be removed in addition to the impurities. Most mineral impurities in coal are denser than pure coal. Thus, they can be separated from run-of-mine coal by placing them in a special fluid medium. The process is somewhat similar to washing lettuce in a large bowl of water. The lettuce leaves are less dense than the water, so they float to the surface. The dirt on the vegetables, on the other hand, is denser than water, so it sinks to the bottom. The entire coal-cleaning process involves three main steps: (1) sorting, (2) washing, and (3) dewatering.
Sorting.
Large pieces of pure coal may settle to the bottom of a solution faster than small pieces that have many impurities. Therefore, the pieces must first be sorted according to size. In many preparation plants, a screening device sorts the coal into three sizes—coarse, medium, and fine. Large chunks are crushed and then sorted into the three main batches according to size.
Washing.
The typical preparation plant uses water or dense fluids—commonly, a suspension of ultrafine magnetite and water—as a medium to separate the impurities from coal. Each batch of sorted coal is piped into a separate washing device, where it is mixed with the medium. The devices separate the coal from the denser impurities. The heaviest pieces—those containing the largest amounts of impurities—sink into a refuse bin. The lighter, purer pieces float to the surface of the medium. Washing removes much ash and sulfur from coal. But only small amounts of organic sulfur, which is closely bound in the carbonaceous part of the coal, can be removed.
Dewatering.
The washing leaves the coal dripping wet. If this excess moisture is not removed, the heating value of the coal will be greatly reduced. Preparation plants use vibrating screens and spinning devices called centrifuges to dewater coal after it is washed. They may also dry the coal with hot-air blowers.
In most cases, the separate batches of coal are mixed together again either before or after dewatering. The resulting mixture of various sizes of coal is shipped chiefly to electric power companies and coking plants. All coking plants and many power companies grind coal to a powder before they use it. They therefore accept shipments of mixed sizes. Some coal users require coal of a uniform size. Preparation plants that supply these users leave the cleaned coal in separate batches.
Shipping coal.
Most coal shipments within a country are carried by rail, barge, or truck. A particular shipment may travel by two or all three of these means. Huge cargo ships transport coal across oceans, between coastal ports, and on large inland waterways.
Barges provide the cheapest way of shipping coal within a country. But they can operate only between river or coastal ports. Trucks are the least costly means of moving small shipments of coal short distances by land. Much coal, however, must be shipped long distances over land to reach buyers. Railroads offer the most economical means of making such shipments.
Many large shipments of coal are delivered to electric power companies and coking plants by unit trains. A unit train normally carries only one kind of freight and travels nonstop from its loading point to its destination. A 100-car unit train may carry 10,000 tons (9,000 metric tons) or more of coal.
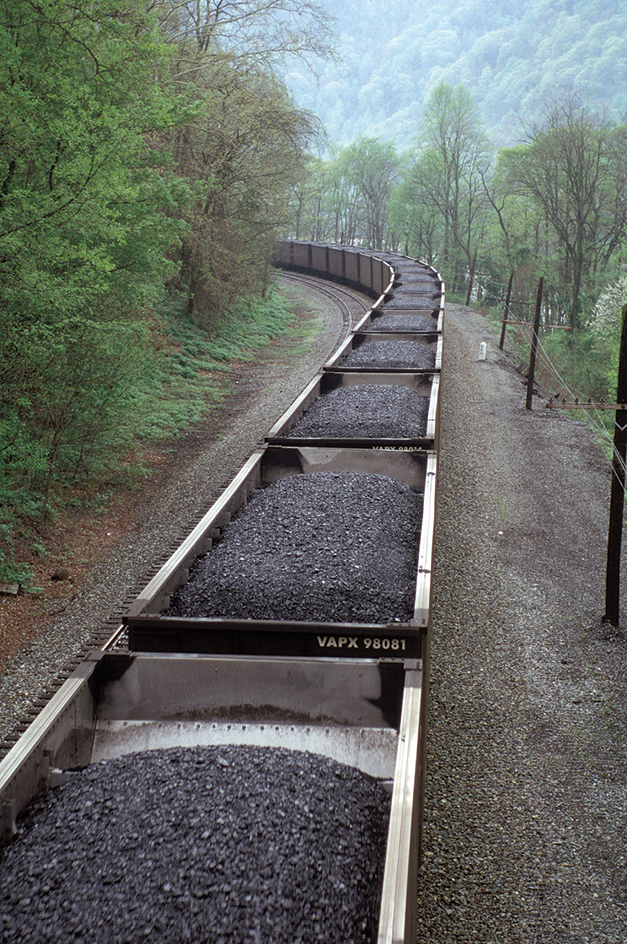
Coal can even flow through pipes from mines to power plants. In the United States, for example, a 273-mile (439-kilometer) underground pipeline carries coal from a mine in Arizona to a power plant in Nevada. The coal is crushed and mixed with water to form a slurry (soupy substance) that can be pumped through the pipeline.
In the past, nearly all coal shipments consisted of anthracite, bituminous coal, or subbituminous coal. It costs the same to ship a given amount of any rank of coal. Lignite, having a low heating value, could not formerly compete with the higher-ranking coals in distant markets. It was used chiefly by power plants built in the lignite fields. Conveyor belts or small railways carried the coal from the mines to the plants. Today, a growing need for low-sulfur coal and improvements in coal preparation technology have increased demand for lignite. Some lignite is shipped by rail from mines to power plants hundreds of miles or kilometers away.
The coal industry
In most countries, the central government owns all or nearly all the coal mines. The major exceptions are Australia, Canada, Germany, South Africa, and the United States. In these countries, all or nearly all the coal mines are privately owned. But the central government regulates certain aspects of the coal industry in these nations.
Australia and Indonesia are the leading coal exporters in the world. The other leading exporters include Canada, Colombia, Kazakhstan, the Netherlands, Russia, South Africa, and the United States. China, India, Japan, and South Korea are the world’s leading coal importers.
Coal producers.
Some coal mines are owned and operated by large coal-mining companies. Others are owned by oil companies, railroads, ore-mining firms, steel companies, or electric utilities. In addition, there are many small firms that own and operate one or two mines. However, the small corporations together produce a much smaller amount of coal than the large corporations do. Steel companies and electric utilities that own coal mines produce coal chiefly for their own use. Their mines are known as captive mines.
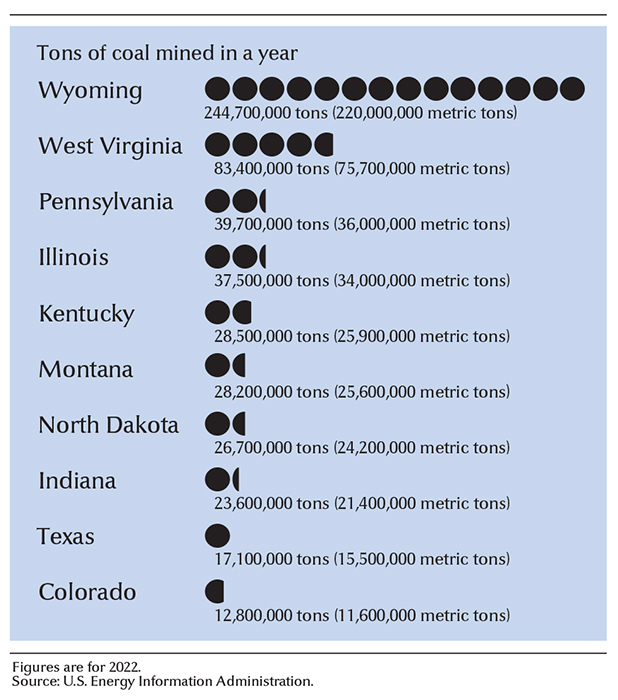
In some countries, the coal industry is represented by a coal union or organization. These organizations seek to increase efficiency within the industry, to encourage favorable legislation, and to inform the public about the industry. Some organizations representing the coal industry also represent the petroleum industry or other heavy industries. In the United States, the National Mining Association (NMA) works to promote the interests of coal producers. The NMA is jointly sponsored by operators of coal, metal, and mineral mines, and the firms that supply them with equipment, technical advice, and transportation.
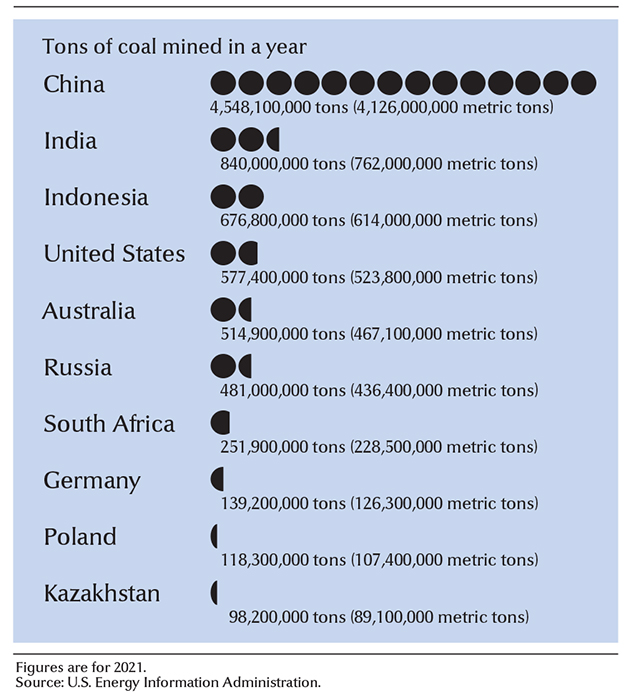
Mineworkers.
Most large coal-mining companies have a full-time staff of professional workers, including engineers, geologists, lawyers, and business experts. They also employ electricians, mechanics, and construction workers. Skilled miners, however, provide the labor on which the industry depends. Underground mining requires more miners than does surface mining.
Mechanization has helped miners become more productive. For example, each coal miner in the United States produced, on the average, about 7 tons (6.4 metric tons) of coal daily in 1950. Today, the production rate averages about 50 tons (45 metric tons) per miner per day. On the average, a strip miner produces about three times as much coal as does an underground miner.
Increased mechanization has also made miners’ jobs more specialized. The job of most miners is to operate a certain type of machine, such as a continuous miner or a power shovel. A beginning miner must work as an apprentice for a specified period to qualify for a particular job. In some countries, mine supervisors must be licensed by the government. In the United States, for example, state departments of mining issue licenses. Generally, the licenses are granted to miners who have two to five years’ experience and who pass a written examination. Most mining engineering jobs call for a college degree in engineering. If the job is directly related to mine safety, it may also require an engineering license. Some mining engineering jobs require only an engineering license.
Until the late 1800’s, coal miners lived and worked under miserable conditions. The mines were dangerously unsafe, and the miners earned barely enough to live on. Many miners banded together in labor unions that called strikes in protest. In the United States, for example, the United Mine Workers of America (UMW), a major industrial trade union, was organized in 1890. Since the early 1900’s, mineworkers’ lives have greatly improved in the industrialized countries.
Mine safety.
In the early days of underground coal mining, accidents killed or disabled thousands of miners every year. Governments have since introduced regulations that set minimum health and safety standards for employers and employees alike. Death rates have fallen dramatically. Many coal companies give every new miner a course in mine safety. In some countries, the government requires a safety course. In addition, coal miners are required to carry a self-rescuer device that provides breathable air in case of fires, explosions, or other mine emergencies. Mine safety involves four main types of problems: (1) accidents involving machinery, (2) roof and rib failures, (3) accumulations of gases, and (4) concentrations of coal dust.
Accidents involving machinery
kill or injure more coal miners in a typical year than any other kind of mining accident. Most strip mine accidents involve machinery. The machines in underground mines must often operate in cramped, dimly lit spaces. Thus, the miners must be doubly alert to prevent accidents.
Roof and rib failures
can be prevented in many cases if a mining company carries out a scientific roof support plan. In some countries, a government organization must approve this plan before mining can begin. Mining engineers make a roof support plan after studying all the rock formations surrounding the coal bed. The plan deals with such matters as the number of pillars that must be left standing, entry widths, mine geometry, and the number of roof bolts that must be used.
Accumulations of gases.
Certain gases that occur in underground coal mines can become a serious hazard if they accumulate. Methane and carbon monoxide are especially dangerous. Methane is an explosive gas that occurs naturally in coal seams. It is harmless in small amounts. However, a mixture of 5 to 15 percent methane in the air can cause a violent explosion. Carbon monoxide is a poisonous gas produced by the partial combustion of such fuels as coal and oil. Blasting in an underground mine may produce dangerous levels of carbon monoxide if the mine is not properly ventilated.
The air vents in a mine normally prevent harmful gases from accumulating. A powerful fan at the surface circulates fresh air through the mine. The circulating air forces polluted air to the surface. As an added precaution against methane, some countries have laws that require all underground mines to have automatic methane detectors. A mine is required to shut down temporarily if a detector shows a methane accumulation above a specific level.
Concentrations of coal dust.
Anyone who breathes large amounts of coal dust over a period of years may develop a disease called pneumoconiosis or black lung (see Black lung ). The disease interferes with breathing and may eventually cause death. Thousands of coal miners have been victims of the disease. In addition, high concentrations of coal dust are explosive. A mixture of coal dust and methane is especially dangerous.
Proper ventilation removes much of the coal dust from the air in a mine. But mines also use other dust control measures. In the United States, for example, federal law requires that underground mines be rockdusted. In this process, the miners spray powdered limestone on all exposed surfaces in the mine entries. The limestone dilutes and coats the coal dust and so lessens the chance of an explosion. Mines use water sprays to hold down the dust along a face that is being mined.
Government regulation.
National or regional governments typically set and enforce safety standards for coal mines. Government agencies regulate mine ventilation, coal dust concentrations, roof supports, and mining equipment. The regulation of coal dust has helped reduce the occurrence of black lung among miners. In some nations, benefits programs provide financial and medical benefits to miners disabled by black lung. Other government agencies may regulate environmental aspects of coal-mining activities. In some countries, dishonest individuals or companies illegally operate secret mines to avoid regulation. Such mines are typically far more dangerous for workers than those operating under government safety regulations.
Coal research
has become increasingly important. Government agencies, environmental organizations, mining companies, and power companies often sponsor such research. The goals of most coal research are (1) to find ways to burn more coal without increasing air pollution, including greenhouse gas emissions,and (2) to develop economical methods of converting coal into liquid fuels and natural gas. In addition, some research seeks to find beneficial uses for the ash produced from coal combustion.
Pollution control.
Most industrialized nations regulate coal-burning power plants to reduce emissions of sulfur dioxide, nitrogen oxide, mercury, and fine particulate matter. In some countries, the burning of high- and medium-sulfur coal is regulated. These coals are sometimes left in reserve, to be used when better sulfur dioxide pollution controls are developed, and low-sulfur coal is burned instead. In the United States, the Environmental Protection Agency enforces air pollution control requirements set forth in the Clean Air Act of 1970 and its amendments. These requirements help protect public health and the environment by establishing air quality standards. The EPA also regulates carbon dioxide emissions based on the Clean Air Act.
New processes for producing power can make coal use more efficient and safer for the environment. In one such process, called fluidized-bed combustion, crushed coal is burned in a bed of limestone. The limestone captures sulfur from the coal and so prevents sulfur dioxide from forming. The heat from the burning coal boils water that is circulated through the bed in metal coils. The boiling water produces steam, which may be used to produce electric power. Coal researchers are also developing ways to capture and store carbon dioxide released by burning coal. Such technologies, known as carbon capture, utilization, and storage (CCUS), are currently too expensive to be widely used commercially.
Coal conversion.
To turn coal into a high-energy fuel, the hydrogen content of the coal must be increased. Bituminous coals have the highest hydrogen content of the four ranks of coal. On average, they consist of about 5 percent hydrogen. The hydrogen must be increased to about 12 percent to produce a high-energy liquid fuel and to about 25 percent to produce manufactured gas. The process of converting coal into a liquid fuel is called coal hydrogenation or liquefaction. In the most common coal hydrogenation method, a mixture of pulverized coal and oil is treated with hydrogen gas at high temperatures and under great pressure. The hydrogen gradually combines with the carbon molecules, forming a liquid fuel. This process can produce such high-energy fuels as gasoline and fuel oil.
Coal can easily be turned into low-energy gas by the carbonization and gasification methods described in the section “The uses of coal.” Low-energy gas can also be produced from unmined coal. This process, called underground gasification, involves digging two widely spaced wells from ground level to the base of a coal seam. The coal at the bottom of one well is ignited. Air is blown down the second well. The air seeps through pores in the seam, and the fire moves toward it. After a passage has been burned between the two wells, the air current forces the gases up the first well. Compared with natural gas, low-energy gas made from coal has limited uses. Low-energy gas must be enriched with hydrogen for its heating value to equal that of natural gas.
The present methods of obtaining high-energy fuels from coal cost too much for commercial use. Hydrogen is expensive to produce. In addition, most fuels made from coal contain unacceptable amounts of sulfur and ash. Researchers seek to develop cheaper methods of coal conversion. Coal research programs often rely heavily on government funding.
History of coal use
No one knows where or when people discovered that coal can be burned to provide heat. The discovery may have been made independently in various parts of the world during prehistoric times. The Chinese were the first people to develop a coal industry. By the A.D. 300’s, they were mining coal from surface deposits and using it to heat buildings and smelt metals. Coal had become the leading fuel in China by the 1000’s.
Commercial coal mining developed more slowly in Europe. During the 1200’s, a number of commercial mines were started in England and in what is now Belgium. The coal was dug from open pits and was used mainly for smelting and forging metals. But most Europeans regarded coal as a dirty fuel and objected to its use. Wood, and charcoal made from wood, were the preferred fuels in Europe until the 1600’s. During the 1600’s, a severe shortage of wood occurred in western Europe. Many western European countries, but especially England, sharply increased their coal output to relieve the fuel shortage.
Developments in England.
During the 1500’s, English factories burned huge quantities of charcoal in making such products as bricks, glass, salt, and soap. The wood shortage in the 1600’s forced most English factories to switch to coal. By the late 1600’s, England produced about 80 percent of the world’s annual coal output. It led in coal production for the next 200 years.
Charcoal had also been widely used in England as a fuel for drying malt, the chief ingredient in beer. Brewers tried using coal for this process. But the gases it produced were absorbed by the malt and so spoiled the flavor of the beer. The brewers found, however, that the undesirable gases could be eliminated if they preheated the coal in an airtight oven. They thus developed the process for making coke. In 1709, an English ironmaker named Abraham Darby succeeded in using coke to smelt iron. Coke then gradually replaced charcoal as the preferred fuel for ironmaking.
The spread of the new ironmaking process became part of a much larger development in England—the Industrial Revolution. The revolution consisted chiefly of a huge increase in factory production. The increase was made possible by the development of the steam engine in England during the 1700’s. Steam engines provided the power to run factory machinery. But they required a plentiful supply of energy. Coal was the only fuel available to meet this need.
During the 1800’s, the Industrial Revolution spread from England to other parts of the world. It succeeded chiefly in countries that had an abundance of coal. Coal thus played a key role in the growth of industry in Europe and North America.
Developments in North America.
The North American Indians used coal long before the first European settlers arrived. For example, the Pueblo Indians in what is now the southwestern United States dug coal from hillsides and used it in the baking of pottery. European explorers and settlers discovered coal in eastern North America during the last half of the 1600’s. In the 1700’s, a few small coal mines opened in what are now Nova Scotia, Virginia, and Pennsylvania. The mines supplied coal chiefly to blacksmiths and ironmakers. Most settlers saw no advantage in using coal as long as wood was plentiful. Wood and charcoal remained the chief fuels in America until about 1880.
The Industrial Revolution spread to the United States during the first half of the 1800’s. By then, coal was essential not only to manufacturing but also to transportation. Steamships and steam-powered railroads were becoming the chief means of transportation, and they required huge amounts of coal to fire their boilers. As industry and transportation grew in the United States, so did the production and use of coal. By the late 1800’s, the United States had replaced England as the world’s leading coal producer.
The United States led in coal production until the mid-1900’s. Its demand for coal then declined as the use of petroleum and natural gas increased. The Soviet Union surpassed the United States in coal production from the late 1950’s through the late 1970’s. From the 1980’s to the late 1990’s, China usually ranked first in coal production, and the United States, the close second. However, during the 2000’s and 2010’s, China greatly increased its production of coal, far surpassing that of the United States.
A type of natural gas extracted from coal beds, called coal bed methane, has become an important energy source. The presence of natural gas in coal beds has been known since the beginning of mining. Widespread production of coal bed methane began in the 1970’s. Scientists and engineers have overcome a number of technical and environmental obstacles to enable clean and practical production of the gas.
Mining companies in most countries are required by law to reclaim strip-mined land. Much of this land is turned into farms and recreation areas. In 1977, for example, the U.S. Congress passed a law requiring mine owners to reclaim the land they use for strip mining.
Recent developments.
Because coal is cheap, abundant, and easy to transport, many power plants burn coal to generate electric power. Coal supplies a large portion of electric power in both developed and developing nations. Since 2010, for example, almost 80 percent of China’s electric power has come from burning coal. As worldwide demand for electric power has increased, so has demand for coal.
However, several factors have limited the use of coal to generate electric power, especially in the United States and other developed countries. Burning coal creates significant amounts of air pollution. Pollutants from coal-burning power plants can cause respiratory illnesses and other health problems in nearby populations. Burning coal also generates greenhouse gases, contributing to global warming. Because of concerns over the environmental impacts of burning coal, some governments heavily regulate coal-burning power plants, increasing their cost.
Coal-burning plants also face increasing competition from other energy sources. Since 2000, a mining method called hydraulic fracturing has become widespread in the United States, leading to cheaper and more abundant natural gas. Some power plants can produce electric power more cheaply—and with less pollution—from natural gas than from coal. In Europe, solar and wind power have displaced a growing number of coal-fired power plants.
A number of new applications, broadly known as clean coal technology, help make coal a cleaner and more efficient fuel source. Some applications purify the coal before it is burned, removing minerals that form air pollution. In gasification, the coal reacts with highly pressurized air or oxygen, forming a clean-burning gas. Other technologies can capture greenhouse gases from burning coal before they reach the atmosphere and contribute to global warming.