Copper has been one of the most useful metals for over 7,000 years. Today, the uses of this reddish-orange metal range from house gutters to electronic guidance systems for space rockets.

Copper is the best low-cost conductor of electric current. As a result, the electrical industry uses about 60 percent of the copper produced, chiefly in the form of wire. Copper wire carries most of the electric current inside homes, factories, and offices. Large amounts of copper wire are used in telephone systems, as well as in television sets, motors, and generators.
Combined with other metals, copper forms such alloys as brass and bronze (see Brass ; Bronze ). Copper and its alloys can be made into thousands of useful and ornamental articles. In the home, copper serves as a basic material for locks, pipe, plumbing fixtures, doorknobs, and drawer pulls. Other commonly used copper products include lamps, pots, pans, roofing, and jewelry.
Chemical compounds of copper help improve soil and destroy harmful insects. Copper compounds in paint serve as pigments and help protect materials against corrosion. Also, copper in small amounts is vital to all plant and animal life.
In ancient times, one of the chief sources of copper for the peoples near the Mediterranean Sea was the island of Cyprus. As a result, the metal became known as Cyprian metal. Both the word copper and the chemical symbol for the element, Cu, come from cuprum, the Roman name for Cyprian metal.
Properties of copper
Copper has an atomic number (number of protons in its nucleus) of 29. Its relative atomic mass is 63.546. An element’s relative atomic mass equals its mass (amount of matter) divided by 1/12 of the mass of carbon 12, the most abundant form of carbon. Copper melts at 1083.4 °C and boils at 2567 °C. At 20 °C, it has a density of about 8.96 grams per cubic centimeter. Chemists classify copper as a transition metal . For information on the position of copper on the periodic table, see the article Periodic Table .
The physical properties of copper make the metal valuable to industry. These properties include (1) conductivity, (2) malleability, (3) ductility, and (4) resistance to corrosion.
Conductivity.
Copper is perhaps best known for its ability to conduct electric current. Silver is the only better conductor, but silver is too expensive for common use. Copper alloys do not conduct current nearly as well as pure copper.
Impurities in refined copper greatly reduce electrical conductivity. For example, as little as 5/100 percent arsenic cuts the conductivity of copper by 15 percent. Copper is also an excellent conductor of heat. This property makes it useful in cooking utensils, radiators, and refrigerators.
Malleability.
Pure copper is highly malleable (easy to shape). It does not crack when hammered, stamped, forged, or spun into unusual shapes. Copper can be worked (shaped) either hot or cold. It can be rolled into sheets less than 1/500 inch (0.05 millimeter) thick. Cold rolling changes the physical properties of copper and increases its strength.
Ductility.
Copper possesses great ductility, the ability to be drawn into thin wires without breaking. For example, copper rod that is 7/16 inches (1 centimeter) in diameter can be heated, rolled, and drawn into a wire that is thinner than a human hair.
Resistance to corrosion.
Copper is quite resistant to corrosion. It will not rust. In damp air, it turns from reddish-orange to reddish-brown. After long exposure, copper becomes coated with a green film called patina, which protects it against further corrosion.
Other properties.
Cold-rolled copper has a tensile strength from 50,000 to 70,000 pounds per square inch (3,500 to 4,900 kilograms per square centimeter, or 350 to 490 megapascals). A material’s tensile strength is the maximum stress it can withstand before breaking. Copper keeps its strength and toughness up to about 400 °F (204 °C).
Copper ores
Seven kinds of ores provide most of the world’s copper. These ores also may contain other metals, such as lead, zinc, gold, cobalt, platinum, and nickel. Copper ores usually contain less than 4 percent copper. Some ores may yield as little as 0.2 percent of copper.
The chief copper ores are sulfides (sulfur compounds). They include bornite, chalcocite, and chalcopyrite. Oxidized ores, such as azurite, cuprite, and malachite, also yield valuable amounts of copper. Almost pure copper, called native copper, rarely occurs in nature. Native copper supplies only a small percentage of the world’s total copper production.
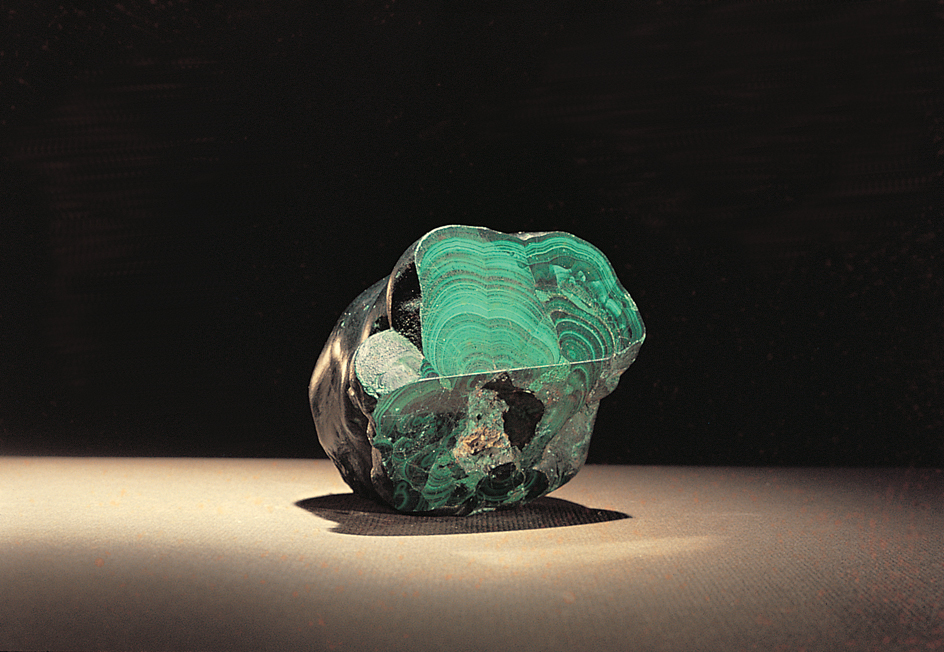
Sources of copper
About 22 million tons (20 million metric tons) of copper are mined each year throughout the world. Every continent has copper deposits. Much of the world’s copper comes from the mountain ranges extending from Alaska to the tip of South America.
In some places, miners dig copper ore from mines far below the surface. Elsewhere, they remove it from huge open pits at the surface. In open-pit mining, large power shovels or other machines remove the ore from wide “steps” 40 to 70 feet (12 to 21 meters) high. Most of the copper mined in the United States comes from open pits.
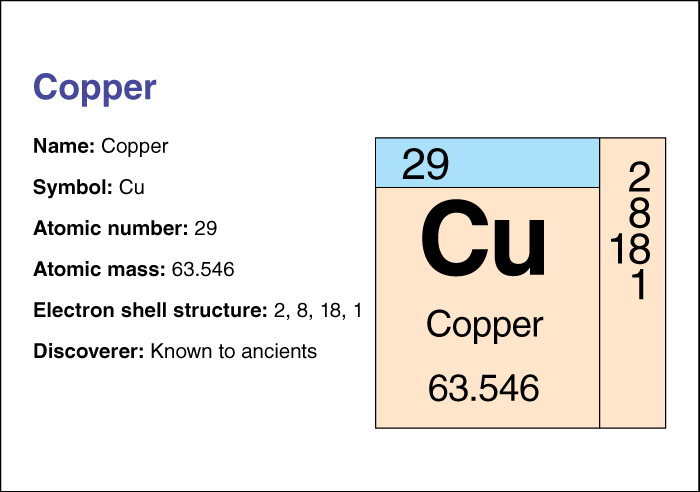
Leading producers.
Chile is the world’s leading copper-producing nation, mining about a fourth of the world’s supply. Large mines near Santiago and in the Atacama Desert provide most of Chile’s copper.
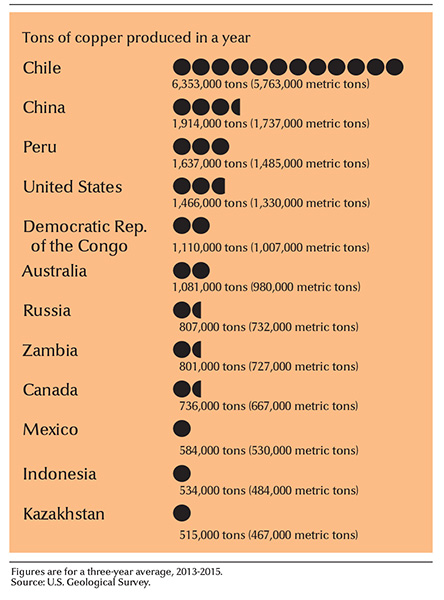
The United States, ranking fourth in world production, mines about 7 percent of the world’s copper. But it uses more copper than it mines, and it imports copper from such countries as Canada, Chile, Mexico, and Peru. Most of the copper mined in the United States comes from Arizona. The Keweenaw Peninsula in Michigan is one of the few remaining sources of native copper.
Canada is also a leading copper-producing nation. Most Canadian copper comes from British Columbia and Ontario. The area around Greater Sudbury in Ontario has the largest copper deposits in Canada. Manitoba, Newfoundland and Labrador, and Quebec also produce significant amounts of copper.
Australia, China, Peru, and Russia are also important copper producers. Large copper deposits also occur in the Democratic Republic of Congo, Indonesia, Mexico, Poland, and Zambia.
Recycling.
Copper is readily recycled from scrap wire, motors, automobile radiators, and electronic equipment. Recycled scrap supplies about one-third of the U.S. copper requirement.
Obtaining copper from the ore
At the mine, large power shovels load the copper ore, frequently in the form of big boulders, into trucks or railroad cars. These vehicles carry the ore to mills. Not all ores go through exactly the same processes. However, all the processes are designed to separate valuable minerals from the ore and waste rock, to extract copper and other metals that may be in the resulting mixture, and to purify these metals.
In a typical process, the ore is sent to the mill, where it is crushed and the waste rock removed. The resulting material is then sent to the smelter, where the metallic copper is separated from impurities. This copper may contain other metals, such as gold, silver, and nickel, that must be removed by refining.
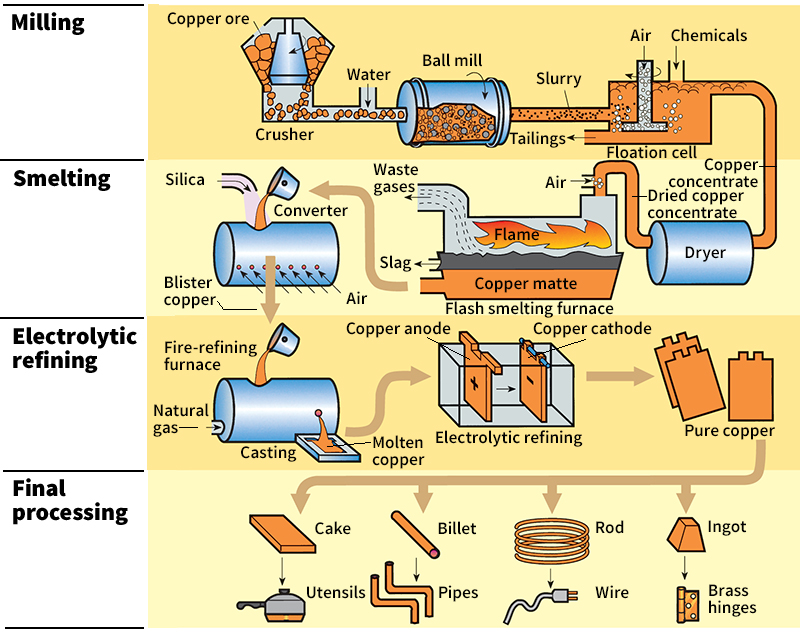
Milling
starts in a crusher, where the ore is broken into small pieces. Then water is added to the crushed ore to form a souplike mixture called slurry. The slurry passes into ball mills, which are rotating, drum-shaped cylinders partially filled with iron balls. As the cylinders rotate, the balls grind the ore into particles small enough to pass through a screen with 10,000 openings per square inch (1,600 openings per square centimeter).
The slurry next goes through a flotation process that concentrates the mineral-bearing particles. The slurry first passes into tanks called flotation cells. There, chemicals and oil are added, and the entire mixture is agitated with air to make it bubble. One chemical makes the bubbles stable. Another coats the mineral particles so that they stick to the bubbles. The bubbles rise to the top of the cell with the particles and form a froth. This froth is skimmed off and dried. The product, called copper concentrate, may contain from 15 to 33 percent copper. The waste material, called tailings, does not become attached to the bubbles. It is emptied from the lower part of the flotation cell and sent to storage ponds.
Smelting
removes most of the remaining impurities from the copper. In smelting, copper concentrate is dried, then blown with air and pure oxygen into a flash smelting furnace. Such a furnace can smelt as much as 3,000 tons (2,700 metric tons) of copper concentrate per day. In the furnace, the concentrate burns and melts, releasing some impurities in the form of sulfur dioxide gas. The molten (melted) material falls to the bottom of the furnace, where it separates into slag and copper matte. Slag, which contains iron oxide, silica, and other impurities, rises to the surface. The slag is removed. Copper matte is heavier and collects under the slag. Copper matte contains from 50 to 75 percent copper. It also contains some impurities in the form of iron sulfide and other metals.
In the next stage of the process, the molten matte goes through a converter. In the converter, blowers force air through it, and silica is added. The silica combines with the impurities, forming slag. The slag is again skimmed from the top. The new mixture is called blister copper because the surface blisters as the copper cools. Blister copper is from 97 to 99.5 percent pure.
The blister copper is refined in a fire-refining furnace. This furnace removes most of the remaining impurities, mainly oxygen. In a process called poling or reduction, natural gas is blown into the melt (furnace load) of molten copper. As the natural gas burns, oxygen and other gases are removed from the copper. The resulting copper is 99.9 percent pure.
Electrolytic refining.
Copper to be used in electrical conductors must be electrolytically refined to a purity of more than 99.9 percent. To do this, fire-refined copper is cast into cakes about 3 feet (91 centimeters) square and 2 inches (5 centimeters) thick. The cakes serve as anodes (positive poles) in the electrolytic process. For a discussion of this process, see Electrolysis .
The copper anodes are put into tanks containing a solution of copper sulfate and sulfuric acid. They are suspended alternately with cathodes (negative poles), which are thin sheets of pure copper called starter sheets. When an electric current passes through the tank, the anode bars gradually dissolve, depositing copper more than 99.99 percent pure on the cathodes. Most of the remaining impurities in the anodes settle to the bottom of the tank and form a sludge. Processors use various methods to recover gold, silver, platinum, and other metals from the sludge. After electrolysis, the copper cathodes are usually melted in a furnace and cast into various shapes and sizes, such as rods, cakes, ingots, and billets.
Leaching
is a method of dissolving metal out of ore with a chemical solvent. Leaching recovers copper from ores that do not react to the chemicals used in the flotation process. In leaching, water containing sulfuric acid or other chemicals circulates through the ore and dissolves the copper. The solution is then mixed with a kerosene solvent containing chemicals that extract the copper. The mixture separates and the copper-bearing chemicals flow into a sulfuric acid solution. This solution is put into a tank to undergo extraction-electrowinning, a process similar to electrolytic refining. The resulting copper is about 99.9 percent pure.
Making copper products
Fabricating plants, such as brass and wire mills, make semifinished forms including sheets, tubes, and wires. They make these forms from copper rods, cakes, ingots, and billets. Manufacturers of copper products buy the semifinished forms from these plants.
Copper sheets
are rolled from copper cakes that measure about 25 inches (64 centimeters) wide, 8 inches (20 centimeters) thick, and up to 72 inches (183 centimeters) long. The cakes are heated in a furnace to about 1700 °F (926 °C), then rolled on a hot mill into sheets about 1/2 inch (13 millimeters) thick. Other mills finish the sheets by rolling them to exact thicknesses. The sheets are then cut into pieces of the required size to make such products as roofing sheets and cooking utensils.
Copper tubes
are made from copper billets that vary in diameter from 3 to 9 inches (8 to 23 centimeters) and are up to 52 inches (132 centimeters) long. Workers heat the billets in a furnace, then pierce them to produce a rough pipe. The pipe shells thus formed are forced through round holes in dies (metal plates) and over other devices to produce tubes of the required size. The tubes are used to make plumbing pipes, household gas lines, and electrical conduits.
Copper wire
is produced by melting copper cathodes and casting the molten copper into a bar about 4 inches (10 centimeters) wide and 3 inches (7.5 centimeters) thick. The bar is rolled into a rod about 5/16 inch (0.8 centimeter) in diameter and then coiled into large rolls. The rod is then pulled through a wire-drawing machine. This machine reduces the rod to the desired wire size. Most copper wire is used to carry electric current.
Extruded copper.
Some copper is extruded (squeezed) through a hole in a die to form the desired shape. Copper can be extruded into rods, tubes, and other special shapes. These are made into hinges, drawer pulls, and other pieces of hardware.
History
Copper was one of the first metals known to human beings. It came into use because early peoples found it in native condition and could easily beat it into small tools, weapons, and ornaments.
Early civilizations.
Copper was probably first used about 8000 B.C. by people living along the Tigris and Euphrates rivers in the Middle East. As early as about 5000 B.C., people through the Middle East knew how to heat and hammer copper into sheets to make larger tools, weapons, and ornaments. Copper was later used by many peoples, including the Chinese and the American Indians.
About 3500 B.C., people discovered how to melt copper with arsenic to make bronze. At about that same time, they learned to smelt copper from ore. From about 3000 B.C. to about 1100 B.C., bronze made with tin instead of arsenic became important (see Bronze Age ). The process of combining zinc with copper to make brass was probably discovered sometime after 1000 B.C. The Romans started making brass coins in the 100’s B.C.
Industrial developments.
From early times until the A.D. 1800’s, ample high-grade ore was available, and methods for processing and using copper changed only slightly. By the late 1800’s, the rapid growth of electric lighting and telephone and telegraph systems had greatly increased the demand for copper, which dwindling deposits of high-grade ore could not meet. Also, most native copper deposits had been used up.
Geologists had located large ore deposits in the United States and Chile. But the copper content of the ore was so low that the ore could not be processed at a profit. About 1900, a young American mining engineer in Utah, Daniel C. Jackling, realized that low-grade ores could be processed cheaply by using mass-production methods. His process involved the use of steam shovels to strip off surface rock. Other special mass-production equipment was used for smelting and refining. New techniques for separating copper from the ore also increased the supply of available copper.