Grinding and polishing are two important manufacturing processes. Grinding uses abrasives to remove material, and polishing uses them to smooth surfaces. Grinding probably ranks as the earliest of all manufacturing processes. Its use goes back to prehistoric times, when ancient people shaped stone tools by rubbing them against hard, rough stones or other kinds of abrasive materials.
Grinding
Grinding tools.
Most grinding is done by abrasive wheels that rotate at high speed, or by power-driven cloth or paper belts coated with an abrasive.
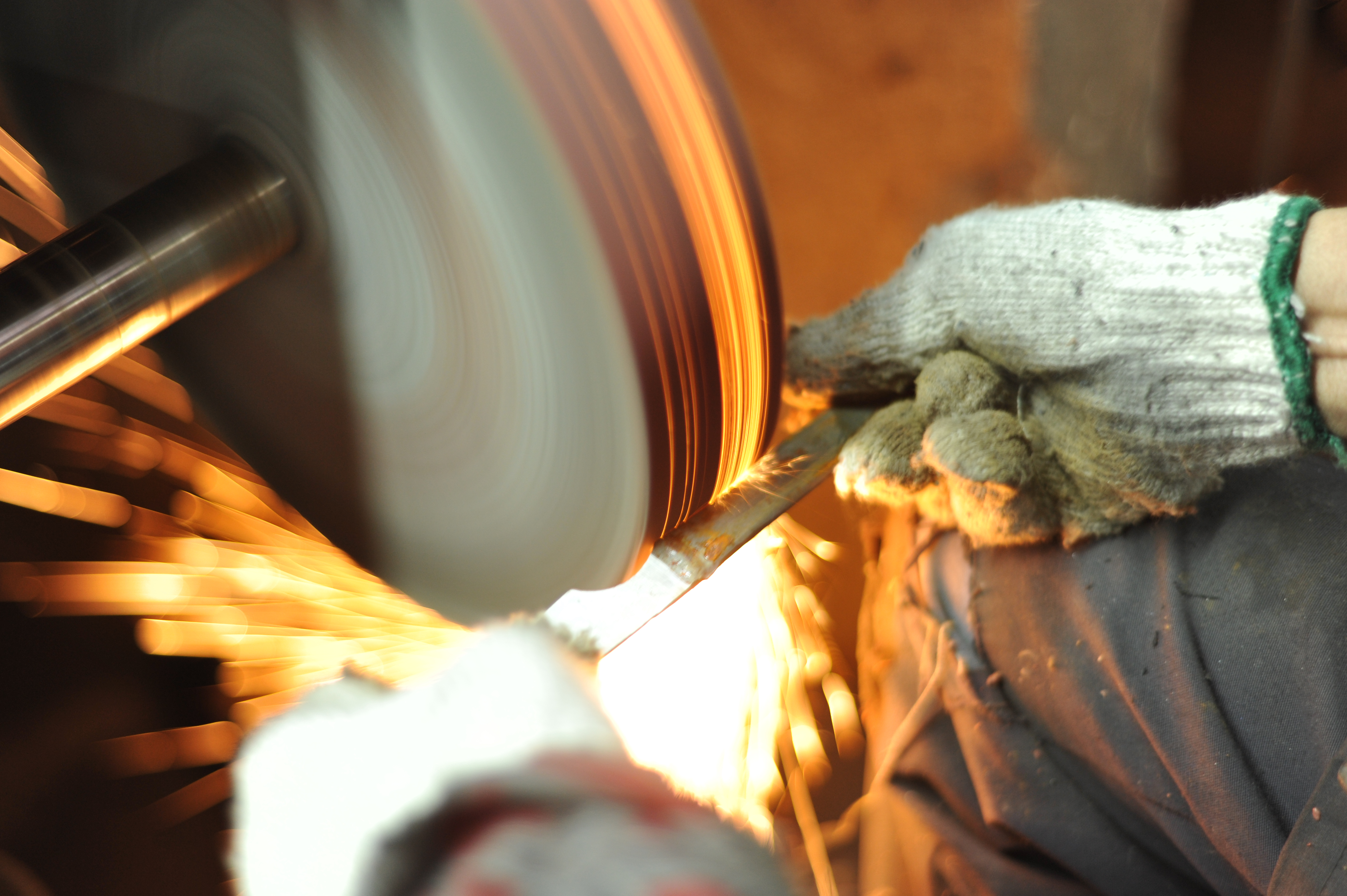
Grinding wheels
are available in many sizes and with a wide range of abrasive grains from coarse to fine. Manufacturers use coarse wheels for rough grinding, medium wheels for general sharpening and grinding, and fine wheels for finished grinding on products that must have an extremely smooth surface.
The most common abrasives are silicon carbide, used for grinding hard, brittle materials such as cast iron; and aluminum oxide, a tougher abrasive used for tool steel and wrought iron. Various cementing materials bond the abrasive grains together into a wheel. In most wheels, the bonding material is clay. The clay is mixed with the abrasive grains and heated so that it becomes glasslike. Water and high temperatures do not affect it. Other bonding materials include common water glass (sodium silicate), plastic resins, and rubber.
Grinding belts
use the same abrasives as wheels, as well as such natural abrasives as crushed garnet and flint. Belts grind metals, glass, and ceramics.
Grinding methods.
The chief grinding methods include (1) offhand grinding, (2) surface grinding, (3) cylindrical grinding, and (4) abrasive wheel cutting.
Offhand grinding
is the simplest method of grinding. The worker holds the material against the rotating wheel or belt. If the work is too large to be held conveniently, the worker may use a small motor-driven grinder and leave the material stationary. Manufacturers use offhand grinding chiefly to sharpen such hand tools as chisels, knives, and drills, and to remove roughness and projections from metal castings.
Surface grinding
produces a smooth, accurate flat surface on machine parts, tools, and dies. Surface grinding machines may have the axis of the wheel either horizontal or vertical to the surface of the work. In the horizontal type of surface grinder, the work is attached to a table that moves back and forth at a right angle to the axis of the wheel. The vertical type uses a cup-shaped wheel. This type often has a large, rotating table to which the work is attached. The table rotates slowly so that the finished work may be removed and the new work attached in a single continuous operation.
Cylindrical grinding
is used to finish accurately the outer surface of shafts, pistons, and other cylindrical machine parts. This is called external grinding. Manufacturers also use internal cylindrical grinding to finish such parts as the insides of automobile cylinders. Cylindrical grinding can be done on a lathe or on a special grinding machine, usually one with a grinding wheel.
Abrasive wheel cutting
uses a narrow grinding wheel, usually bonded with rubber. The wheel rotates at a high speed. A cooling liquid keeps the work and the tool from overheating. Abrasive wheels do fast, smooth work in cutting steel shafts and bars.
Polishing
Polishing, also called buffing, is usually done with wheels made of cloth, felt, or leather coated with a fine abrasive such as a fine grade of silicon carbide or aluminum oxide. For finer work, wheels coated with jewelers’ rouge, a fine ferric-oxide powder, or tripoli, a type of silica, may be used.
In some polishing, manufacturers use abrasive belts or a special polishing wheel made of soft rubber with abrasive grains molded in it. The rubber wears away just fast enough to prevent the wheel from becoming clogged or glazed on the surface. Most polishing on irregularly shaped pieces is done by hand. For big jobs, such as finishing stainless-steel sheets, manufacturers use large, high-speed machines.