Iron and steel are the world’s cheapest and most useful metals. These hard, durable metals are used in making thousands of products, from paper clips and refrigerators to automobiles and ships. Machines made of iron and steel help produce almost everything we use, including our clothes, our homes, and even our food.
The word iron can refer to both an element and a number of alloys (chemical mixtures) of iron and other elements. As an element, iron is one of the most common chemical substances in Earth’s crust, but it is almost never found in pure form there. Almost all iron occurs in ores, though some meteorites also contain iron.
Loading the player...Steel manufacturing
Iron ores are mineral or rock deposits in which geological processes have concentrated iron. Manufacturers crush and process these ores to produce high-grade iron concentrates. The concentrates are turned into metallic iron by heating them with other raw materials in huge furnaces. Most metallic iron is used to make steel, but some is made directly into iron products.
Iron is the basic material of steel, and all steel contains iron. However, the properties (characteristics) and uses of iron and steel vary widely. Steelmakers first refine liquid iron in furnaces, often along with recycled iron and steel scrap. They produce steel by alloying the purified iron with carbon and often with certain metals as well. The liquid steel is then formed into sheets, beams, rods, wire, tubing, and other shapes.
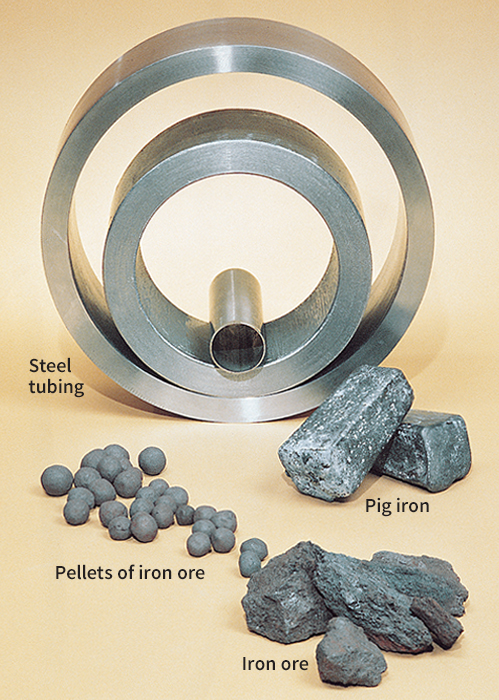
Some modern steel mills perform all the steps in steelmaking, from smelting iron ore to producing steel in useful shapes and forms. Other modern mills, called minimills, perform only the steps needed to melt scrap steel into new raw steel.
As early as 4000 B.C., people used iron from meteorites to make ornaments, weapons, tools, and utensils. The making of iron from ores developed independently in several parts of the world, including the Middle East, China, and India. The technology spread quickly to other regions. By about 1000 B.C., many civilizations had mastered the art of ironmaking. Early ironmakers sometimes produced small quantities of steel. However, steel could not be manufactured cheaply in large quantities until the second half of the 1800’s. The technology of steelmaking developed rapidly from 1850 to 1930.
Today, the production of iron and steel is one of the world’s most vital industries. Throughout the world, steelmaking plants employ about a million workers. Millions of additional workers provide machinery, raw materials, and energy to iron and steel companies, or manufacture consumer products from iron and steel.
Kinds of iron and steel
The metals called iron and steel are alloys of the element iron and at least one other element. In general, steel is any alloy of the elements iron and carbon that contains less than 2 percent carbon. Most types of steel also contain some manganese, and many kinds also include other elements. The properties of any kind of iron or steel depend largely on the chemical composition of the alloy. Heating and working (shaping) the metal can change its physical properties.
There are thousands of kinds of iron and steel. Iron can be classified as (1) pig iron, (2) cast iron, or (3) wrought iron. Steel can be grouped as (1) carbon steel, (2) alloy steel, (3) stainless steel, or (4) tool steel.
Pig iron
is the crude iron produced in a blast furnace from iron ore. Most pig iron contains 3 to 4 percent carbon and smaller amounts of other elements. The term pig iron comes from an early method of pouring liquid iron from a blast furnace into molds set around a central channel. The molds looked somewhat like a group of baby pigs around their mother. The bars of iron that formed in the molds were called pigs. Today, most pig iron is used in making steel. However, a small amount is made into cast iron or wrought iron.
Cast iron
is any iron alloy that contains from 2 to 4 percent carbon. It often contains silicon as well. Because of its high carbon content, solid cast iron cannot be hammered or welded, no matter how hot it is heated. At an elevated temperature, it simply melts. Cast iron is made into useful objects by pouring the liquid metal into molds and letting it cool and harden.
Wrought iron
is nearly pure iron, with essentially no carbon alloyed with it. It has glasslike fibers of melted sand called silicate slag mixed with the pure iron. Unlike cast iron, wrought iron is malleable—that is, it can be shaped by hammering or rolling.
Wrought iron was once used in making many products now typically made from steel. Today, manufacturers produce only small amounts of wrought iron. Most wrought iron is made into porch railings, gates, fences, and other decorative items.
Carbon steel
is the most widely used steel. The properties of carbon steel depend primarily on how much carbon it contains. Most carbon steel has a carbon content of less than 1 percent. Carbon steel can be cast, rolled, or hammered into useful shapes. It is made into a wide range of products, including structural beams, automobile bodies, kitchen appliances, and cans.
Alloy steel
contains some carbon, but its properties result chiefly from the addition of other chemical elements. These elements improve one or more of the steel’s properties. For example, manganese increases strength and toughness. Nickel provides greater toughness, especially in steels used at extremely low temperatures. Molybdenum increases hardness and resistance to corrosion. Other elements frequently used in alloy steels include chromium, titanium, tungsten, and vanadium. Many alloy steels contain more than one alloying element in addition to carbon.
Stainless steel
resists corrosion better than any other type of steel. Chromium is its chief alloying element. Most stainless steel contains between 12 and 18 percent chromium. Many stainless steels also contain nickel. Such household items as knives, flatware, and pots and pans are made of stainless steel. Various kinds of stainless steel are used in a large number of products, including automobile parts, hospital equipment, and razor blades. Equipment made from stainless steel is widely used in the dairy, food, and chemical industries.
Tool steel
is an extremely hard, wear- and heat-resistant steel used to make metalworking tools. Tool steels are produced by heat-treating certain types of high-carbon alloy steel. Most tool steels contain mixtures of chromium, manganese, molybdenum, nickel, tungsten, and vanadium. In the heat-treating process, steel is heated to a high temperature and then cooled quickly.
Sources of iron ore
The term iron ore commonly refers to any rock or mineral that contains enough iron to make it possibly worth mining. The location and characteristics of an ore deposit may at first make it undesirable as a source of iron. However, developments in transportation, mining techniques, or mineral processing may later make a deposit commercially valuable. Changes in demand for iron, or changes in government policies or world trade, can lead to the opening or closing of ore mines.
The supply of iron ore in the world remains plentiful even though the steel industry continually uses huge amounts of it. In some countries, much of the richest ore has been used up. As a result, steel companies must use lower-grade ores. They may also import ore from other countries. The leading iron ore mining countries, in order of production, are Australia, Brazil, China, India, and Russia. Most of Australia’s iron ore deposits occur in Western Australia. Brazil has large deposits of rich ores that contain up to 65 percent iron. Most of Brazil’s ore comes from the states of Minas Gerais and Pará. Most of China’s iron ore comes from large, low-grade deposits in the northeastern provinces. Other nations that have large deposits of iron ore include Kazakhstan, Sweden, and Ukraine.
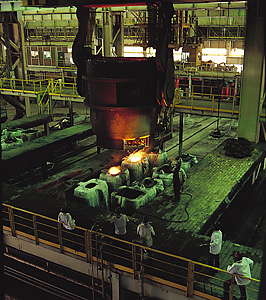
The most important iron ore deposits in North America lie near Lake Superior. The Mesabi Range in Minnesota has produced more ore than any other area in the United States. California, Michigan, and South Dakota also have major deposits. Canada’s chief deposits lie along the border between Quebec and Labrador and north of Lake Superior in Ontario.
Kinds of iron ore.
In nature, iron always occurs in chemical combination with other elements, especially oxygen, carbon, sulfur, and silicon. Iron ores thus contain chemical compounds made up of iron and one or more other elements. The principal ores from which iron is obtained include hematite, magnetite, limonite, pyrite, siderite, and taconite.
Hematite and magnetite
are the richest iron ores. They are iron oxides containing about 70 percent iron and 30 percent oxygen. Hematite is typically steel-gray, dull red, or bright red in color. Magnetite is dark gray to black and has magnetic properties that make it easy to locate and to concentrate.
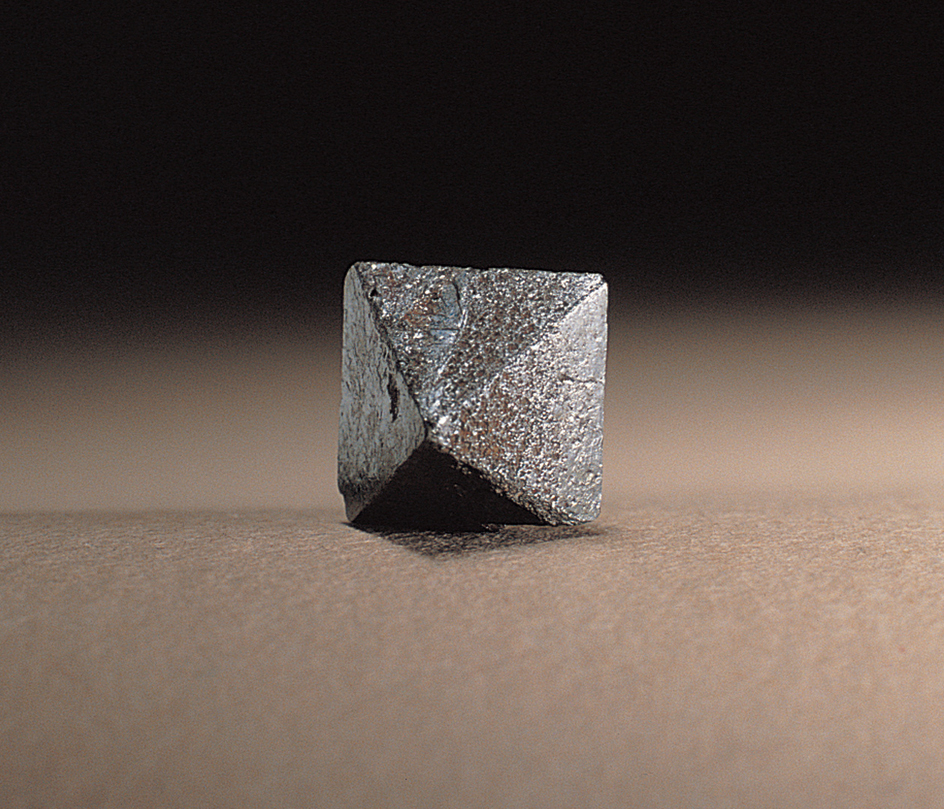
Limonite
has an iron content of about 60 percent. It is yellow-brown to black in color, and it consists of iron oxide and water.
Pyrite
is about half iron and half sulfur. It is pale yellow to brassy-yellow in color and is sometimes mistaken for gold.
Siderite
contains about 50 percent iron, plus carbon and oxygen. It occurs in a wide range of colors, including white, yellow, brown, greenish-gray, and gray. In the past, it served as an important source of iron in the United Kingdom and Germany. However, those two nations have exhausted their siderite deposits.
Taconite
is a low-grade ore that serves as a chief source of iron in North America. It may be either magnetic or nonmagnetic. Magnetic taconite is a hard, fine-grained rock. The magnetic taconite mined today typically contains 17 to 35 percent iron in the form of magnetite and 40 to 55 percent silica. Nonmagnetic taconite contains iron in the form of limonite or hematite. Taconite is typically gray in color.
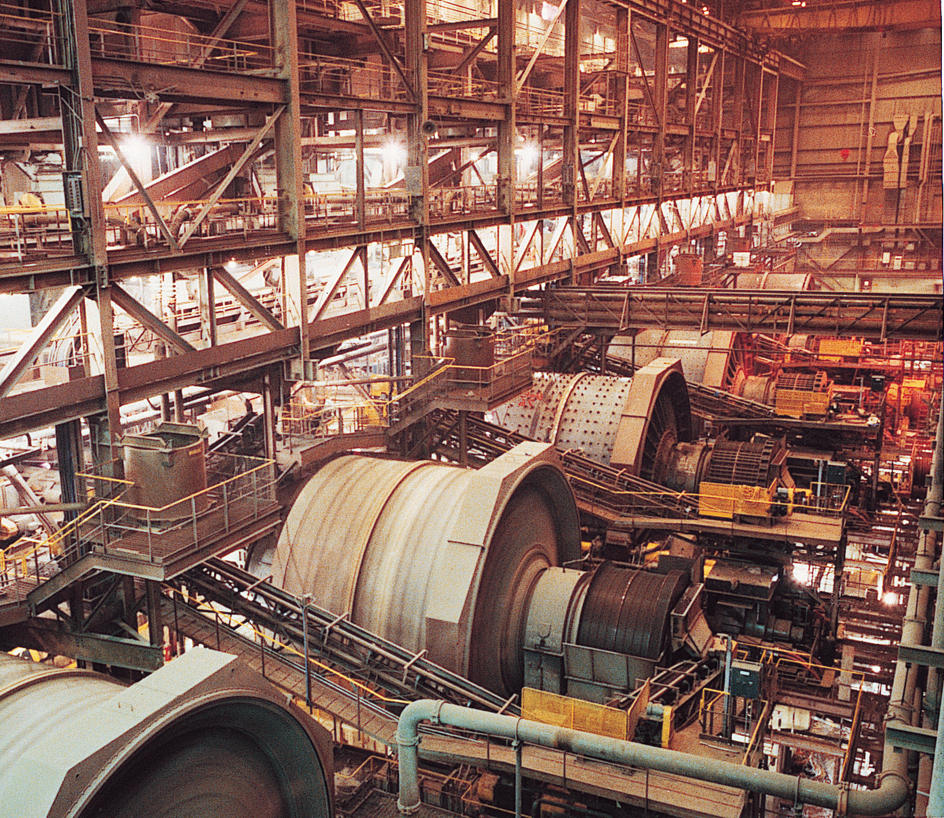
Iron ore deposits.
The world’s largest deposits of iron ores were formed by a geological process that began more than 2 billion years ago. This process began in Earth’s shallow seas. Iron compounds in the water gradually settled to the bottom of the seas. There, together with sand and silt, they formed rock. Earthquakes and the movements of Earth’s crust later raised this rock above the level of the water. In some areas, rich concentrations of ore were left behind as water trickled through the rock, interacting with and breaking down some of the other minerals in the rock.
Other iron ore deposits formed in different ways. For example, the slow cooling of molten (melted) volcanic rock produced iron ore deposits in Sweden and some other areas. Elsewhere, tiny organisms in the water caused iron oxide to form. Today, iron oxides accumulate in marshy areas and on beaches.
Mining and processing iron ore
There are two basic methods of mining iron ore, open-pit mining and underground mining. After the ore has been removed from the earth, it must be processed to make it suitable for use in making iron.
Open-pit mining
is used to dig out deposits of iron ore that lie near the surface. First, bulldozers and other earthmoving equipment remove the soil and rocks that cover the deposits. This material is called the overburden. Next, miners use explosives to break up the mass of ore. Power shovels then scoop the ore into trucks and railroad cars for delivery to a central processing station.
Most of the world’s iron ore comes from open-pit mines. The largest of these mines extend over several square miles or square kilometers and may measure more than1640 feet (500 meters) deep.
Underground mining,
also known as shaft mining, involves digging tunnels into an ore deposit. Miners then go into the tunnels to remove the ore. To mine iron ore far below the surface, they dig a shaft into the rock next to the deposit. From this shaft, the miners drill horizontal tunnels into the ore at various levels. Conveyor belts or special railroad cars transport the ore to the shaft, where it is hoisted to the surface in buckets.
Underground mining is much more expensive and hazardous than open-pit mining. Today, this method is rarely used except to mine extremely high-grade ores.
Processing.
Ores with a high iron content may need only to be crushed, screened, and washed to remove particles too small for use. However, most iron-mining nations rely heavily on taconite and other ores that require extensive processing. These ores must be broken apart so that the particles of ore can be separated from the sand and rock. The rich ore is called concentrate, and the waste materials are referred to as tailings.
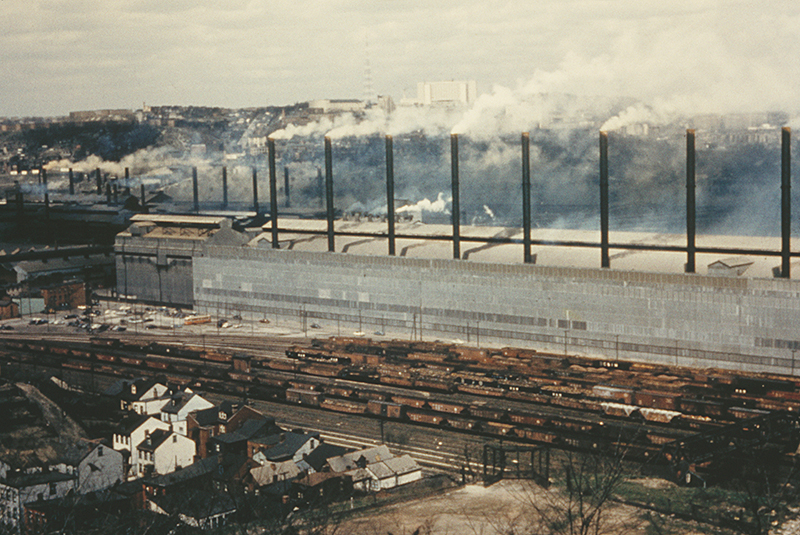
Chunks of taconite are crushed to fine powder by tumbling them with steel rods or balls in large, rotating barrels. Powerful magnets then remove particles of magnetite from the powder. If the taconite contains nonmagnetic hematite, the hematite can be converted to magnetite by roasting the ore in a furnace without oxygen. Or workers can mix the crushed taconite with a dense slurry (soupy mixture) of water holding finely ground particles of an alloy of iron and silicon. The waste particles remain suspended in the slurry. But the particles that contain iron are denser and so settle to the bottom. This concentrated iron oxide is then removed and dried.
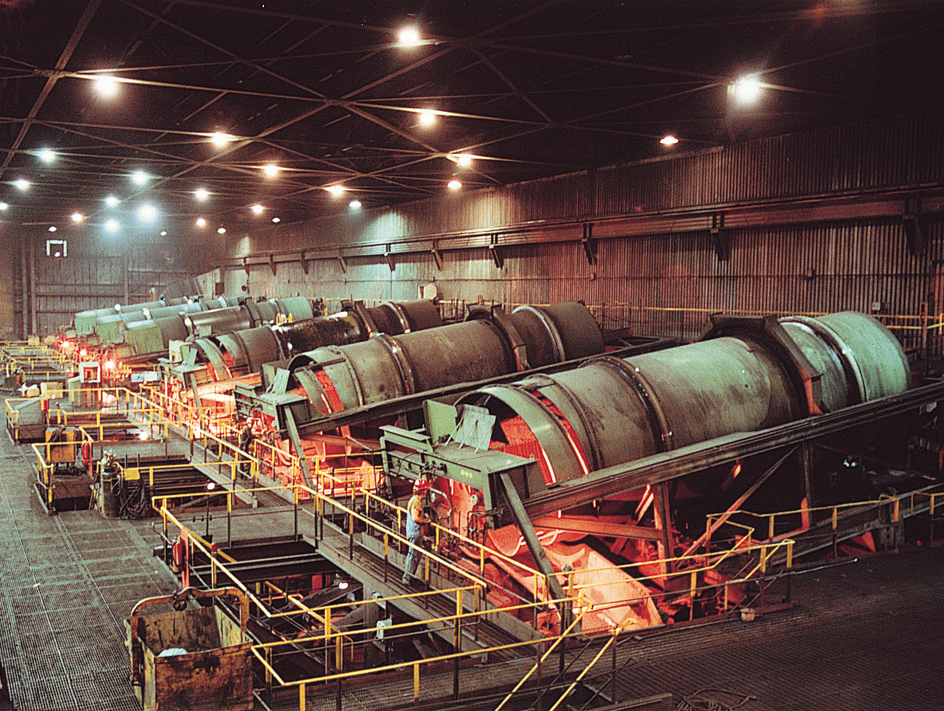
Iron oxide produced from taconite must be converted into a form suitable for shipping and for use in making iron. In the most widely used process, the concentrate is mixed with a little moist clay, which binds the concentrate so that it can be formed into pellets. The pellets, which measure 1/2 inch to 1 inch (1.25 to 2.5 centimeters) in diameter, are dried and baked to a hard finish.
Taconite produces about 2 tons (1.8 metric tons) of tailings for every 1 ton (0.9 metric ton) of iron-oxide pellets. Therefore, iron ore is processed near the mine to save the cost of transporting huge quantities of waste.
How iron is made
To convert iron oxide into metallic iron, ironmakers must remove the oxygen from the ore. This process requires heat and a reducing agent, a substance that chemically combines with the oxygen that is released.
Iron is made either in a blast furnace or by direct reduction. In a blast furnace, iron ore is combined with a reducing agent at high temperatures to produce liquid iron. In direct reduction, the temperature remains below the melting point of iron.
The blast furnace process.
A blast furnace is a huge cylinder made of steel and lined with firebrick (heat-resistant brick). Some blast furnaces stand more than 100 feet (30 meters) tall and measure over 30 feet (9 meters) wide at the base. Structures for loading raw materials and recovering waste gases are on top. Blast furnaces operate continuously until their brick lining wears out. A furnace typically functions for more than 20 years before it must be rebuilt.
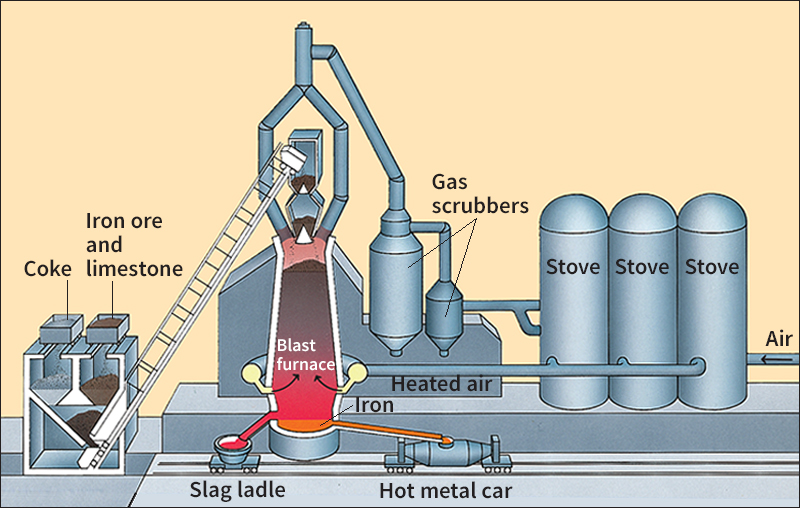
The term blast furnace comes from the blast of hot air that is constantly forced into the lower part of the furnace. This air is heated by two or more giant stoves that can be as tall as the furnace itself. The air is blown through a stove into the furnace. The production of molten iron in a blast furnace generates waste gases that are, in turn, used to fire the stoves. These gases are often mixed with natural gas for the firing. The blast of hot air enters the furnace through pipes called tuyeres at between 1600 and 2300 °F (870 and 1260 °C). While air is blown through one stove, the other stove or stoves are being heated.
In addition to iron ore, coke and limestone are raw materials used for making iron in a blast furnace. Coke is a hard substance that consists of about 90 percent carbon. It is made by heating coal in airtight ovens. Heat drives out gases and tar from the coal, and coke remains. Limestone helps remove impurities from iron ore. Many of these impurities do not usually melt at temperatures as low as the melting point of iron. But limestone, when mixed with iron ore, acts as a flux—that is, it combines with impurities in the ore and causes them to melt at lower temperatures.
The iron ore, coke, and limestone together are called the charge. Open cars carry the charge to the blast furnace up a ramp called a skip hoist. At the bottom of the ramp, each skip car is filled with a carefully weighed load of the charge. At the top of the ramp, the skip car dumps its load into the furnace. Many modern plants use a continuous conveyor belt rather than a skip hoist to load the furnace.
As the materials in the charge drop into the furnace, they contact the blast of hot air. The hot air causes the coke to burn. Oxygen in the air combines rapidly with the coke to produce carbon monoxide gas. This gas serves as the agent, removing oxygen from the ore and chemically combining with it to form carbon dioxide. The burning of coke also produces intense heat, which melts the iron. Temperatures rise above 3000 °F (1600 °C) at the bottom of the furnace. In this area, called the hearth or crucible, the molten iron forms a pool 4 to 5 feet (1.2 to 1.5 meters) deep. Impurities referred to as slag float to the top of this pool.
Waste gases rise to the top of the furnace. Devices called gas scrubbers use water to clean these gases of dust and other impurities. The gases are then burned as fuel in the stoves that heat air for the furnace.
Molten iron is typically tapped from a furnace every 3 to 5 hours. Workers burn out a plug called the iron notch, and a white-hot stream of iron rushes through the hole. The iron flows into a hot-metal car, which can hold more than 150 tons (135 metric tons) of iron.
Traditionally, slag was tapped once or twice between each tapping of iron. Workers removed it through a slag notch located above the level of the iron. The slag flowed into a slag ladle mounted on a railroad car. At many blast furnaces, slag is now removed through the same notch through which the iron is tapped. Manufacturers use slag in making portland cement, as a material called aggregate to be mixed into concrete, and as ballast to make the beds for railroad tracks.
The direct reduction process
converts the iron oxide in ore into direct-reduced iron. There are several methods of direct reduction. The main methods all use gases obtained from natural gas as agents. Each of these processes combines iron ore and reducing gases in a large furnace. Other methods use coal as the reducing agent. Direct reduction is a major method of producing iron in India, Iran, Mexico, Venezuela, and several other nations.
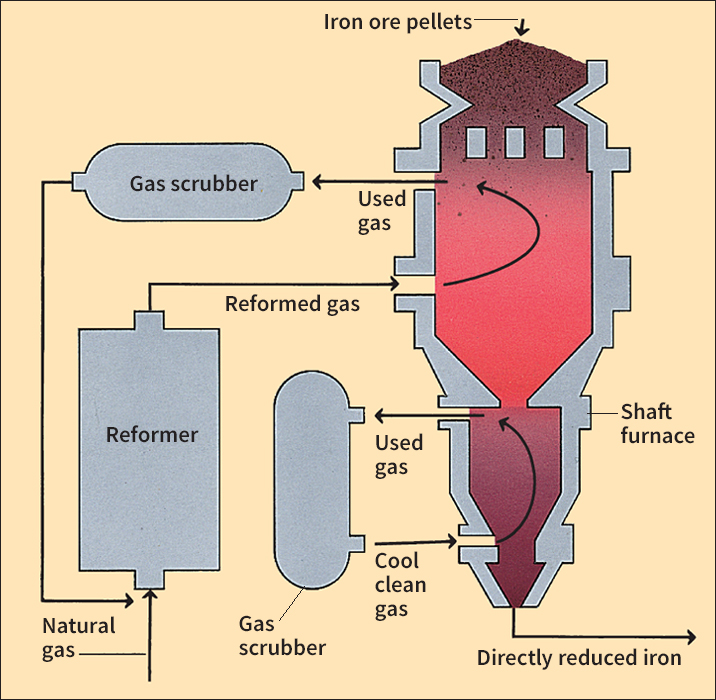
Furnaces used in direct reduction can be built much more quickly and cheaply than blast furnaces and coke ovens. Because it does not use coke ovens, direct reduction causes much less air pollution than blast furnaces do. But metallic impurities in iron ore are not removed in a direct reduction furnace as they are—by the formation of slag—in a blast furnace. Therefore, the solid iron produced in a direct reduction system must be further processed before being made into steel.
Making iron products
More than 90 percent of the iron produced in blast furnaces and nearly all direct-reduced iron is used in making steel. The rest is cast into pigs and shipped to plants called foundries, which produce cast iron and wrought iron.
Casting iron pigs.
A pig-casting machine has two conveyor belts that carry shallow molds. Workers pour molten iron from a ladle or hot-metal car into a channel that divides and flows into the molds. Water cools the iron in the molds. By the time the molds reach the end of the conveyor belt, the iron has hardened into pigs that weigh about 40 pounds (18 kilograms) each.
Making cast-iron products.
At a foundry, workers melt pig iron in a furnace called a cupola and then process it into various types of cast iron. The iron is cast in molds to manufacture such products as pipe, automobile engine blocks, and fire hydrants.
Making wrought-iron products.
To produce wrought iron, workers melt high-quality pig iron and remove most of its impurities. They pour the molten iron over a glassy mass of silicate slag. The iron and silicate form spongelike balls. These balls are placed in presses that squeeze out the excess slag and form blocks of wrought iron called blooms. The processes used to shape wrought-iron blooms into various products are the same as those used with steel blooms. For a description of these processes, see the “Shaping and finishing steel” subsection in this article.
How steel is made
Most steel is produced from molten pig iron and scrap iron or steel. Steelmakers recycle steel scrap from rolling or casting mills along with scrap recovered from recycled steel cans and junked automobiles. Steelmaking primarily involves the removal of excess carbon and other unwanted substances from these materials and the addition of other desired materials in carefully controlled amounts.
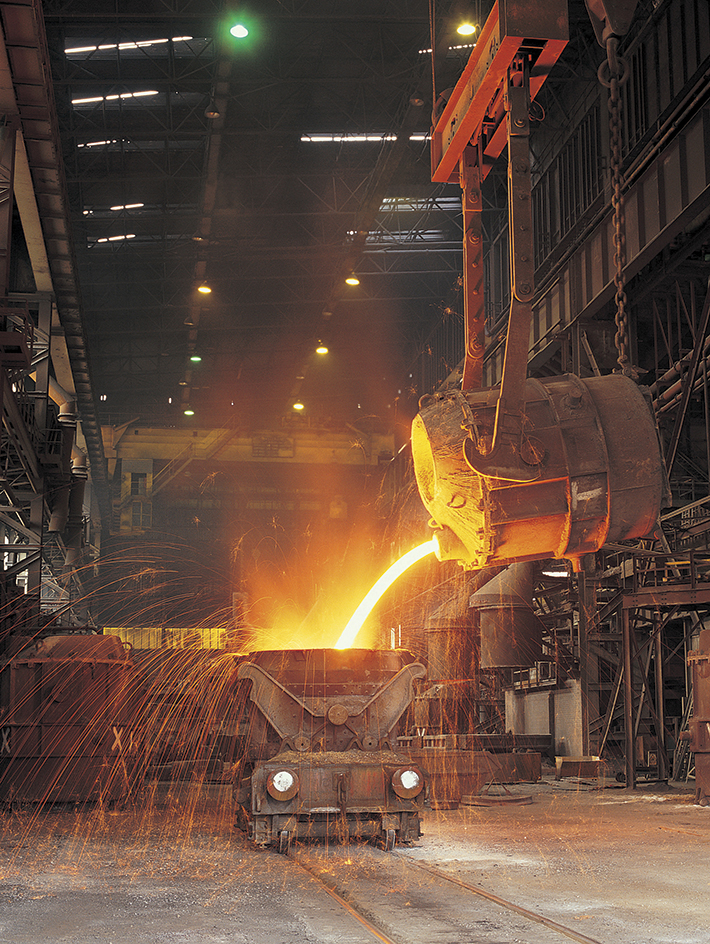
There are three chief methods of making steel: (1) the basic oxygen process, (2) the electric furnace process, and (3) the open-hearth process. In each of these processes, the materials making up the charge are placed in a furnace, where the necessary reactions are carried out to produce a batch of refined steel. The rate of steel production varies greatly among the three processes. A basic oxygen furnace produces a batch of steel in about 45 minutes. An electric furnace does the job in about four hours, and an open-hearth furnace takes about eight hours. Steelmaking furnaces range in capacity from less than 50 tons (45 metric tons) to more than 500 tons (450 metric tons).
The basic oxygen process (BOP)
produces steel by blowing oxygen at high pressure into molten iron and scrap. This method was commercially developed in Austria in 1952 and has since grown in importance throughout the world. Today, about 75 percent of the world’s steel is produced by the basic oxygen process.
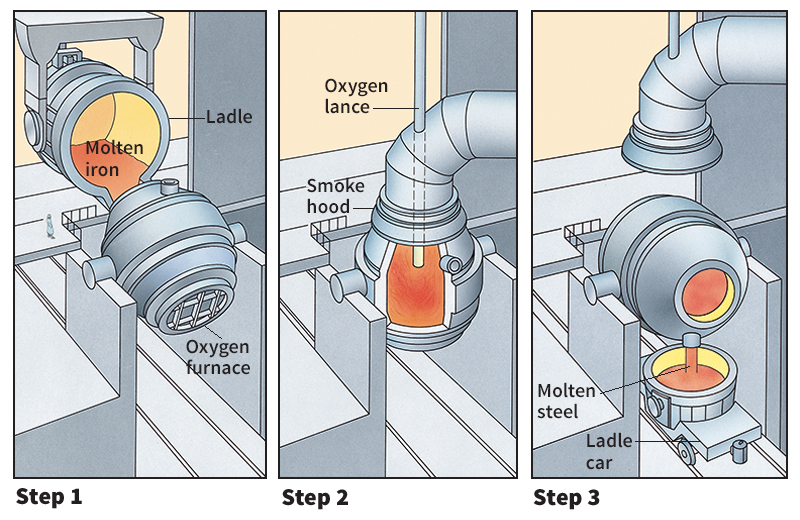
A basic oxygen furnace, usually called a BOF, is a pear-shaped steel vessel with an open top and heat-resistant lining. The furnace is mounted on pivots so it can be tilted for charging and emptying. Basic oxygen furnaces are usually operated in pairs. While one produces steel, the other is being charged.
The usual charge in a BOF consists of molten iron combined with 20 to 35 percent scrap steel. The molten iron is typically about 4 percent carbon, and it contains smaller amounts of silicon and other impurities. After tilting the furnace and adding cold scrap, workers pour in the molten iron and return the furnace to its upright position. Then they lower an oxygen lance (pipe) into the furnace to blow pure oxygen onto the charge. Typically, a blast of 22,500 to 31,500 cubic feet (640 to 900 cubic meters) of oxygen per minute is blown at supersonic speed into the metal. The oxygen penetrates into the charge and reacts rapidly with the carbon, silicon, and other impurities. These reactions generate the heat necessary for melting the scrap while also bringing about the refining process. Fluxes are then added, and a slag soon forms. A hood on top of the furnace traps the waste gases. When steel is ready to be poured, the BOF is tilted, and the molten steel flows out through a tap hole near its top. The steel flows into a ladle, to which workers can add alloying materials.
During the 1970’s, European steelmakers developed a process called Q-BOP. In this process, oxygen is blown into the charge at the bottom of the furnace. Powdered fluxes are blown in along with the oxygen. The Q stands for the German word Quell, which means fountain and refers to the manner in which the oxygen enters the charge. A Q-BOP unit stirs the charge vigorously, and it can melt larger chunks of scrap. Today, many oxygen furnaces combine top and bottom blowing.
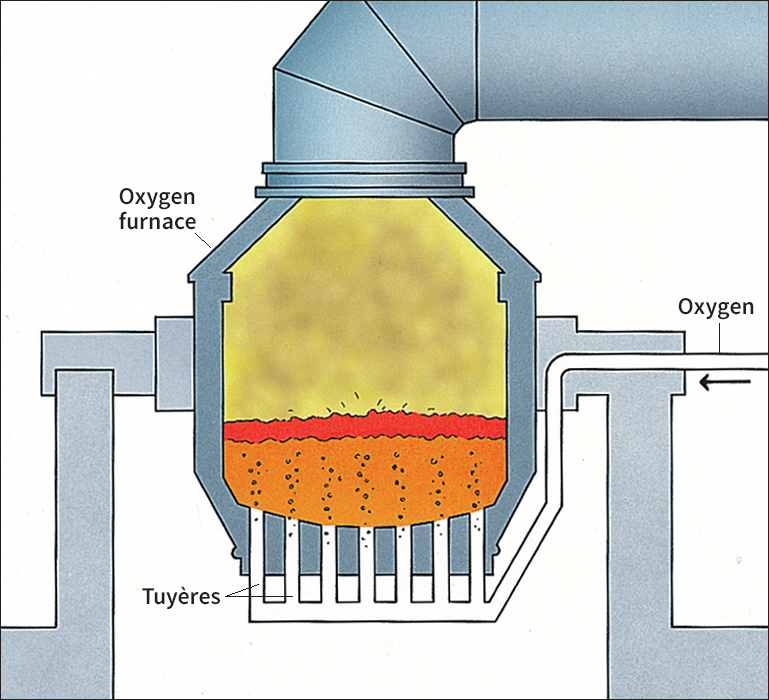
Both BOP and Q-BOP produce steel at relatively low cost, largely because they require no additional fuel to create heat. The two processes also produce steel rapidly. In addition, steel produced by these methods is low in nitrogen. Nitrogen reduces the toughness of certain kinds of steel. However, BOP and Q-BOP do not permit as much precision as other processes do in the control of the chemical composition of steel. They also can use only a limited amount of scrap.
The electric furnace process
uses strong electric currents to produce the heat needed to make steel. The electric arc furnace is the most widely used type of electric furnace. Other types of electric furnaces melt steel by using an oscillating (vibrating) magnetic field to induce current in the steel. This field is created in a coil that encircles the part of the furnace that holds the charge. Electric furnaces account for 25 percent of the world’s total steel production.
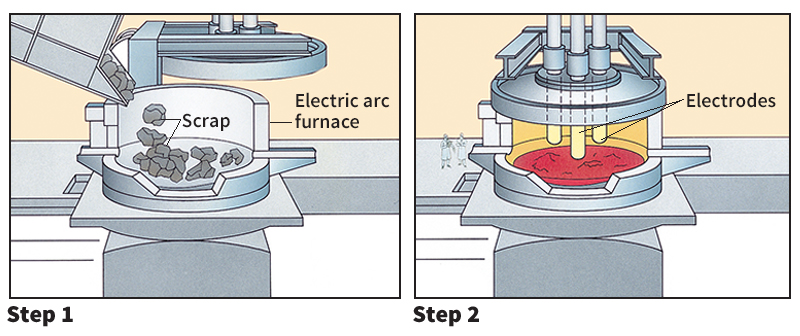
An electric arc furnace consists of a shallow steel cylinder lined with firebrick. The roof has holes through which up to three graphite or carbon rods called electrodes are inserted. A powerful electric current arcs (jumps) from one electrode to the charge material and then to another electrode. This arcing produces intense heat, which melts the charge. Electric arc furnaces that use direct current (DC) power sources have a single rod inserted through the cylinder’s roof. The arc passes from that electrode through the charge to an electrode in the bottom of the furnace.
The charge in an electric arc furnace consists mostly of scrap steel and alloy materials. Steelmakers rarely use molten pig iron in this type of furnace. But they sometimes use pellets of direct-reduced iron in the charge. The furnace roof is raised and swung to one side so the charge can be dumped in. After the charge has melted, fluxes and additional alloying material are added through a charging door on the side. The furnace stands on rockers and so can be tilted to pour off the slag through the charging door. Later, it is tipped in the opposite direction to pour out the molten steel through the tap hole.
Electric arc furnaces are used in minimills. Their advantages over other furnaces include efficient operation, economical construction, and low emissions of pollutants into the air. Electric arc furnaces are ideal for making alloy steels and tool steels. These steels require the addition of alloying elements that readily combine with oxygen. Such elements, which include chromium and vanadium, would be oxidized rapidly in an open-hearth or basic oxygen furnace and thus lost in the slag. The steel and slag in an electric arc furnace contain so little oxygen that alloying elements are not oxidized.
The open-hearth process
got its name because the hearth of the furnace is open directly to the flames that melt the charge. The furnace has a lining of firebrick, and a low, arched roof covers the hearth. A typical open-hearth furnace measures about 90 feet (27 meters) long and about 30 feet (9 meters) wide. Most open-hearth plants have several furnaces end to end in one long building. Workers use heavy-duty cranes and special charging machines to fill the furnaces through doors on one side and tap the steel on the opposite side. The floor on the loading side is higher than that on the tapping side.
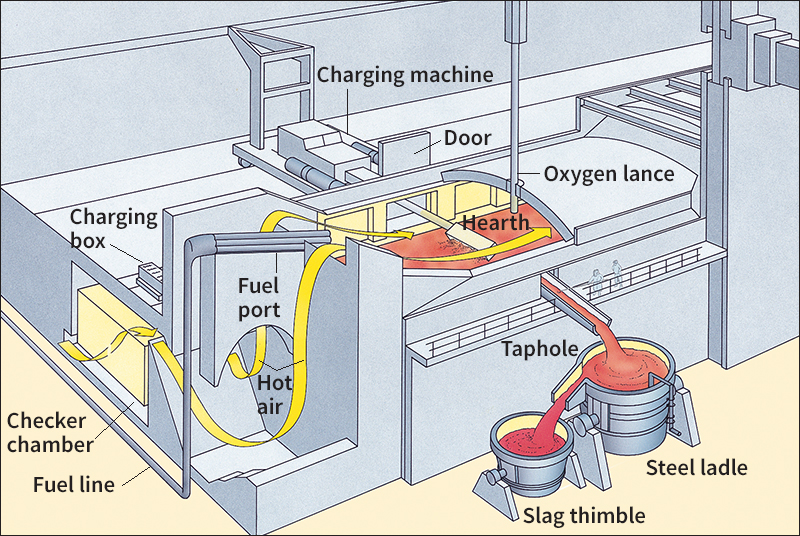
Each end of an open-hearth furnace has a fuel burner and a checker chamber. This chamber contains firebricks arranged in an open, checkered pattern that provides many passages through which air and waste gases can flow. While the burner at one end of the furnace sends flames onto the hearth, the hot exhaust gases are drawn through the checker chamber at the other end. These hot gases heat the chamber, then eventually exit out the smokestack. The furnace automatically switches burners about every 15 minutes, reversing the flow of gases through it. Thus, the air on its way to the hearth is preheated by passing through the hot checker chamber. Many open-hearth furnaces also have an oxygen lance in the roof. Pure oxygen is forced through this pipe into the furnace to speed the melting process.
Open-hearth furnaces can combine molten pig iron and cold scrap in widely varying proportions, but most steelmakers use about equal amounts of each. First, a charging machine dumps limestone and scrap steel into the furnace. After these materials have melted, molten iron is poured into the furnace. As the heating continues, most of the carbon from the iron is driven off in the form of carbon monoxide gas. Other impurities are oxidized and become part of the slag. Workers take a sample of the molten steel and may add materials to obtain the desired composition.
To tap the steel, workers blow out the tap-plug with a small explosive. The steel flows into a large ladle. Workers may then add alloying materials or substances to remove oxygen from the steel. When the slag appears, it overflows from the ladle into a smaller container called a slag thimble.
The open-hearth process can use gas, oil, or even powdered coal as fuels, but it makes steel much more slowly than other methods do. It also produces large volumes of polluting waste gases. For these reasons, use of the open-hearth method has declined steadily since 1950, when it was the chief steelmaking process. Today, only Russia and Ukraine make significant amounts of open-hearth steel.
Special refining processes.
Steel tapped from a furnace may require additional refining and alloying. Such special processes are necessary to produce the highest grades of steel, such as that used in the manufacture of jet airplanes. Steelmakers may put molten steel into a vacuum chamber to remove hydrogen, oxygen, and other gases. They may mix the molten steel by bubbling argon gas through it to distribute alloy elements, make the temperature uniform, or make it easier to remove tiny particles of sulfur or other contaminants. Steelmakers may also add additional alloying elements in precise quantities.
Shaping and finishing steel
Liquid steel must be cast into a solid form before it can be made into useful objects. Steelmakers cast most steel by means of continuous casting or ingot casting. These processes result in solid steel that must be further formed by rolling, forging, extruding, or other processes. In mold casting, a small amount of steel is cast in a mold that gives it the shape of a finished product. Some types of steel receive a special finish or coating.
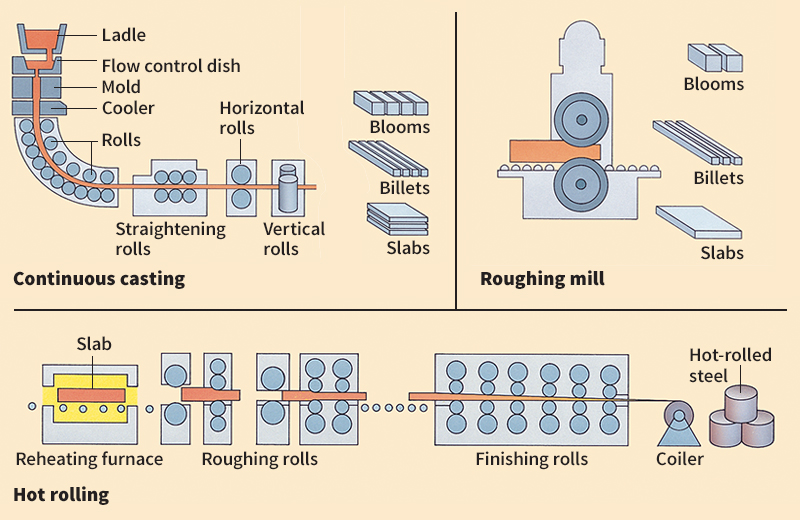
Continuous casting,
sometimes called strand casting, produces blooms, slabs, or billets—three semifinished forms of steel—directly from molten steel. Blooms have a square cross section, and slabs are rectangular in cross section. Billets are square like blooms, but they have a smaller cross section. Most billets are much longer than blooms.
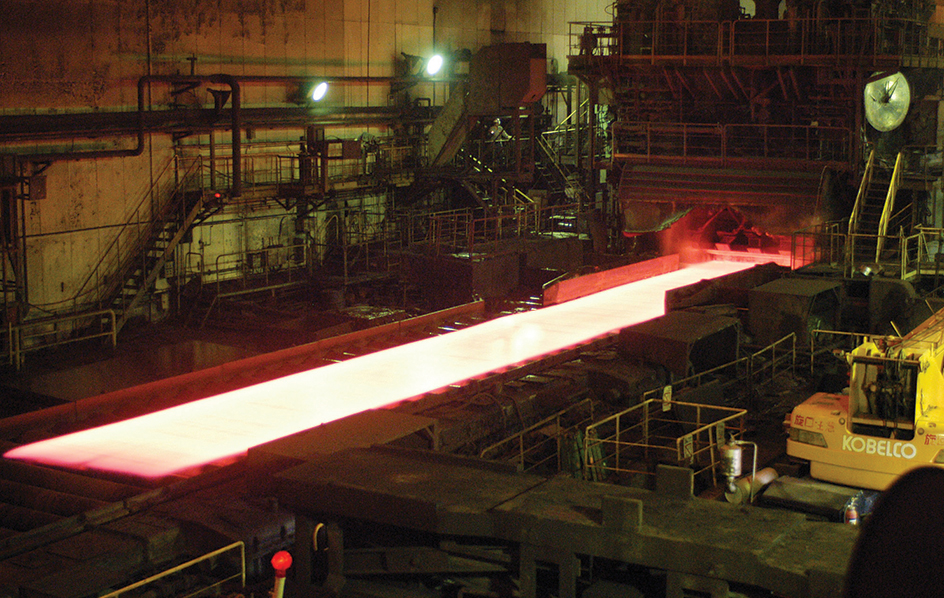
In continuous casting, workers pour liquid steel from a ladle into a tundish (flow control dish) at the top of the machine. The steel flows at a controlled rate from the tundish through a mold that forms the metal into the desired shape. Cold water quickly cools the steel, causing it to solidify even as it continues to move through the caster. As the steel leaves the caster, cutting torches or mechanical shears cut it into desired lengths.
Beginning in the 1960’s, steelmakers in Japan and Western Europe rapidly adopted continuous casting. Today, it accounts for more than 95 percent of raw steel production worldwide. In many countries, including the United States, it accounts for 99 percent or more.
Ingot casting
is the casting of steel into blocks called ingots. Steel ingots vary widely in size, depending on the type of steel and the kind of product to be made. For example, ingots of tool steel may weigh only a few hundred pounds or kilograms. In contrast, huge ingots weighing up to 300 tons (270 metric tons) are made into parts for enormous industrial machines. Most ingots weigh between 2 and 40 tons (1.8 and 36 metric tons).
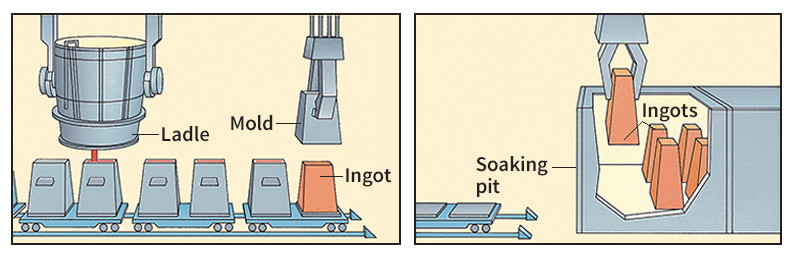
To cast ingots, workers pour liquid steel from a ladle into molds made of cast iron. Most of these molds have a tapered, rectangular shape. The molds are placed on special railroad cars, and steel is poured into them from above. After the steel hardens, which may take up to three hours, the mold is lifted off by giant tongs that grip it by handles on the sides. Iron contracts as it cools, and the outside of an ingot cools faster than its center. As a result, a funnel-shaped depression called a pipe forms in the top of an ingot. The portion of the ingot that contains the pipe—as much as 20 percent by weight—is removed and remelted as scrap.
Ingots are then placed in a furnace called a soaking pit, where they are heated to a temperature of about 2200 °F (1200 °C). The heated ingots travel to a roughing mill, a machine that squeezes them between heavy rollers to form billets, blooms, or slabs.
Since the 1960’s, most steelmakers have switched from ingot casting to continuous casting. The processes of casting, heating, and rolling ingots are more costly and time-consuming than continuous casting methods. Continuous casting avoids inconsistencies that result from the slow cooling of ingots. It also generates less scrap than ingot casting produces.
Rolling
is the most commonly used method of shaping steel products. In this process, billets, blooms, or slabs pass between heavy rollers that squeeze them into the desired size and shape. The major products made by rolling include (1) sheet and strip, (2) bars, (3) railroad rails and structural beams, and (4) plates.
Sheet and strip
are flat products, generally less than 1/4 inch (6.4 millimeters) thick. Strip is much narrower than sheet, which may be up to 100 inches (250 centimeters) wide. Sheet and strip are the main products of the steel industry.
Steelmakers produce most sheet and strip in the form of large coils that the user can cut into pieces of any desired length. However, some sheet and strip is cut into specified lengths at the plant. A great deal of sheet and strip is used in automobile bodies, but thousands of other products also contain these forms of steel.
Machines called hot-rolling mills produce sheet and strip from slabs and billets. The process is known as hot rolling because the steel is reheated to about 2200 °F (1200 °C) before being rolled. A hot-rolling mill has many sets of rollers called roll stands arranged in a long line. In each roll stand, the rollers are closer together than in the preceding stand. As a result, the steel is squeezed thinner and thinner as it travels through the mill. As the thickness decreases, the length increases.
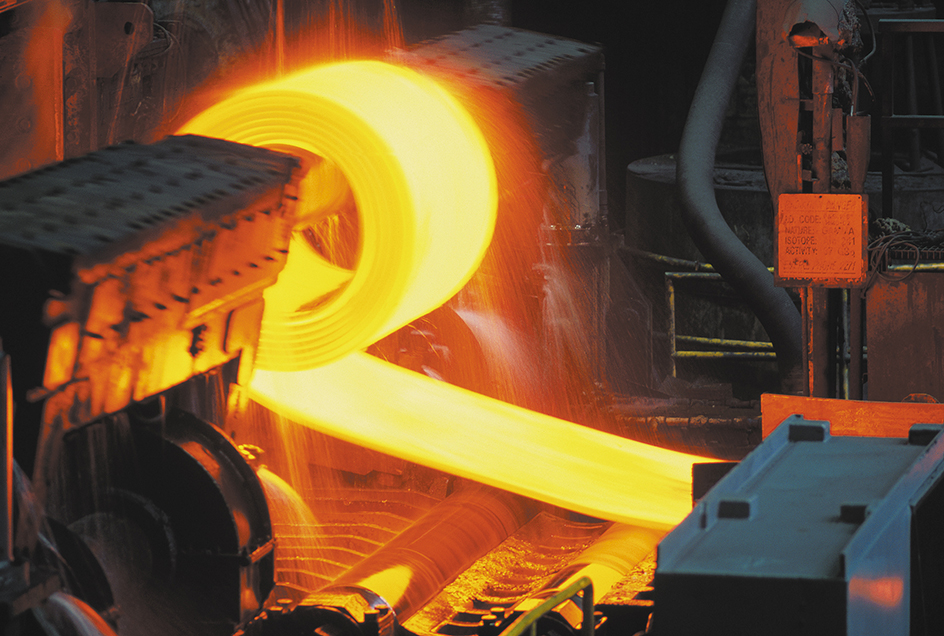
A hot-rolling mill can convert a slab 5 inches (13 centimeters) thick and 8 feet (2.4 meters) long into a sheet 1/16 inch (1.6 millimeters) thick and 1,400 feet (430 meters) long. The process takes only a few minutes. A hot-rolling mill may be housed in a building up to 1 mile (1.6 kilometers) long. This great length is necessary because of the large number of roll stands and the tremendous increase in the length of the steel. As the hot-rolled steel comes out of the last stand, it is wound into large coils.
After cooling down, the coils of steel may be shipped to customers, or they may be processed further. Much hot-rolled sheet and strip is pickled and then cold-rolled. Pickling involves passing the steel through vats of acid to remove oxide that formed on it during hot rolling. In a cold-rolling mill, the steel travels rapidly at room temperature through a series of roll stands and then is re-coiled. Cold rolling gives steel the ability to be stretched and shaped without cracking. It also makes steel thinner and smoother and gives it a bright finish.
Bars
are made in many sizes and in such shapes as round, square, oval, and hexagonal. They are hot rolled by bar mills, which resemble the machines used for sheet and strip. However, a bar mill has grooved rolls that squeeze a hot billet into the desired shape. Many bars receive further processing after being hot rolled. They can be pulled at room temperature through an opening in a tool called a die. This process strengthens the steel and gives it a bright, smooth finish. Products made from steel bars include hand tools and auto parts.
Railroad rails and structural beams
are hot-rolled into long lengths in the same way as bars. Steelmakers produce diverse structural shapes, such as I-beams, angles, tees, zees, and channels. Most railroad rails and structural beams are made from blooms.
Plates
are flat and measure more than 1/4 inch (6.4 millimeters) thick. They are used in the construction of ships and bridges and in many kinds of industrial and scientific equipment. Steel plants roll most plates from slabs, but some come directly from ingots. Machines called reversing mills produce the majority of plates. The heated steel passes back and forth between the rollers of a single roll stand. The distance between the rolls decreases with each pass until the steel reaches the desired thickness. Some plates are made by continuous rolling mills like those that produce sheet and strip.
Forging
is a process in which steel manufacturers heat ingots or billets and hammer or press them into the desired shape. Many products that must withstand great stress are made by forging. This process changes the internal structure of steel to give it the greatest strength where needed. The largest forging presses shape ingots weighing several hundred tons.
Extruding
involves forcing heated steel through an opening in a die. A ram at one end of a cylinder pushes the steel through a die at the other end. Molten glass serves as a lubricant to help the hot steel slip through the die. The steel comes out shaped like the die opening. Steel firms use extrusion to make seamless tubing and products of complicated shapes.
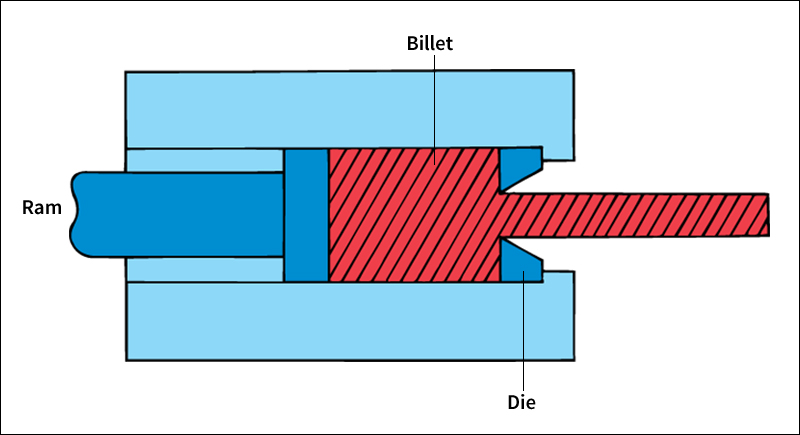
Other shaping processes
are used in making a variety of small steel products. Automatic machines stamp, hammer, and press steel into such products as bolts, nails, screws, and tools. Wire is made by drawing steel rods through a series of successively smaller dies.
Finishing.
Many types of steel receive a special finish or coating. For example, some stainless steel goes through special grinding and polishing. The most important coating processes include (1) galvanizing and (2) electroplating.
Galvanizing
is the process of coating steel with a thin layer of zinc. The zinc coating makes the steel highly resistant to corrosion. Galvanized steel sheet is made into such products as heating ducts and storage tanks. The most widely used method of galvanizing, called hot-dip galvanizing, starts with coils of steel sheet. The steel is annealed (heated and then cooled slowly) to make it more flexible. Next, rollers carry the steel into a pot of molten zinc. The steel then travels through a cooling tower, where the zinc coating hardens. The finished product is wound into coils or cut into sheets.
Electroplating
coats steel with another metal by means of electric current. Steel companies use this process in producing tin-plated steel, which is made into tin cans. Steel is electroplated with chromium to make tin-free steel. This metal can be used instead of tin-plated steel to produce cans and other containers.
The steel industry
Steelmaking ranks among the world’s most important industries. Steel products play an essential role in almost all major economic activities, including manufacturing, mining, construction, transportation, and agriculture. In addition, military forces depend on steel for tanks, ships, and aircraft components. China produces more steel than any other nation. India, Japan, and the United States are also leading steel producers.
In some countries, the government owns and manages the steel industry. In others, the industry consists of privately owned companies. Still other countries have a mixture of private and public ownership. Even in nations where the entire steel industry is privately owned, the government generally plays a major role in regulating it.
The manufacturing plants that make up the steel industry vary greatly in size. The largest, called integrated steel mills, have a full range of equipment, including coke ovens, blast furnaces, steelmaking furnaces, and rolling mills. Most of these plants produce from about 1 million to 10 million tons (900,000 to 9,000,000 metric tons) of steel annually. Minimills generally consist of one or more electric furnaces to melt scrap and a mill that produces bars, rods, or flat rolled steel. A minimill may produce less than 100,000 tons (90,000 metric tons) of steel in a year. However, some minimills produce well over 1 million tons (900,000 metric tons) yearly.
Few of the major steel-producing countries produce as much steel as the capacity of their plants. Actual production varies with the general level of economic activity. The demand for steel rises when there is expansion in construction and manufacturing activities. When these activities decline, so does steel production.
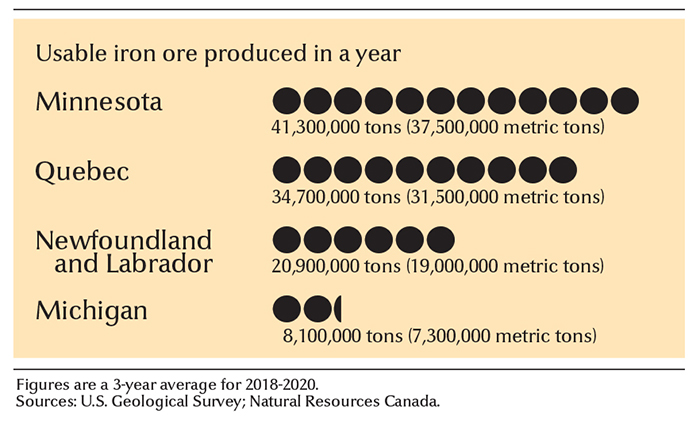
Modern steelmaking methods and equipment enable steel plants to operate with far fewer employees than was possible many years ago. In nearly all major steelmaking countries today, the steel industry employs less than 10 percent of the amount of people it did in 1975. Most employees are production and maintenance workers. Others have professional, administrative, sales, and clerical positions. Steelmaking also offers opportunities for chemists, engineers, metallurgists (experts on metals), and technicians.
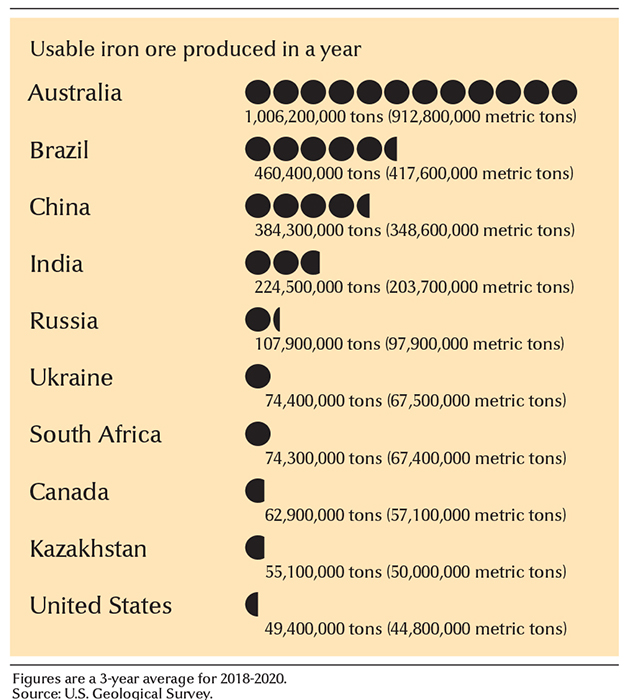
In China,
the steel industry has undergone astonishingly rapid growth since the 1980’s. During the early 2000’s, China’s steel production grew by 10 to 30 percent in almost every year. The country is the world’s leading producer and consumer of steel. Its leading steelmaking company is the China Baowu Group. Other major steel companies include HBIS Group, and Ansteel Group Corporation.
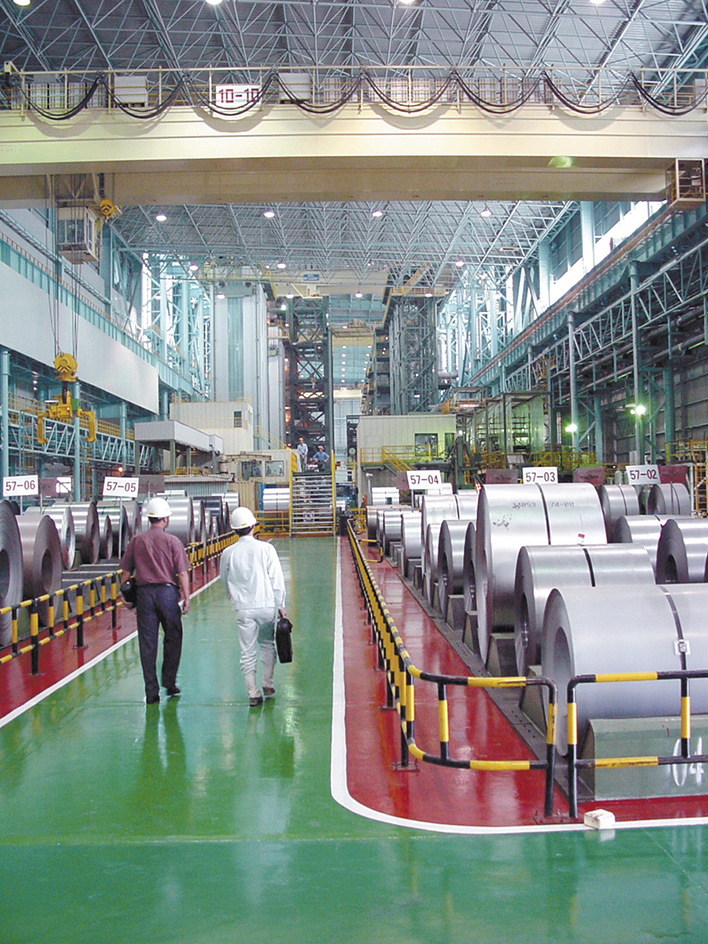
Steel produced by the basic oxygen process accounts for about 95 percent of China’s total production, and electric processes account for about 5 percent. More than 98 percent of China’s steel is continuously cast. China has most of the raw materials it requires to produce steel. However, its domestic iron ore and coal are of low grade. Consequently, its steel industry is a major source of air and water pollution. China also imports high-grade iron ore.
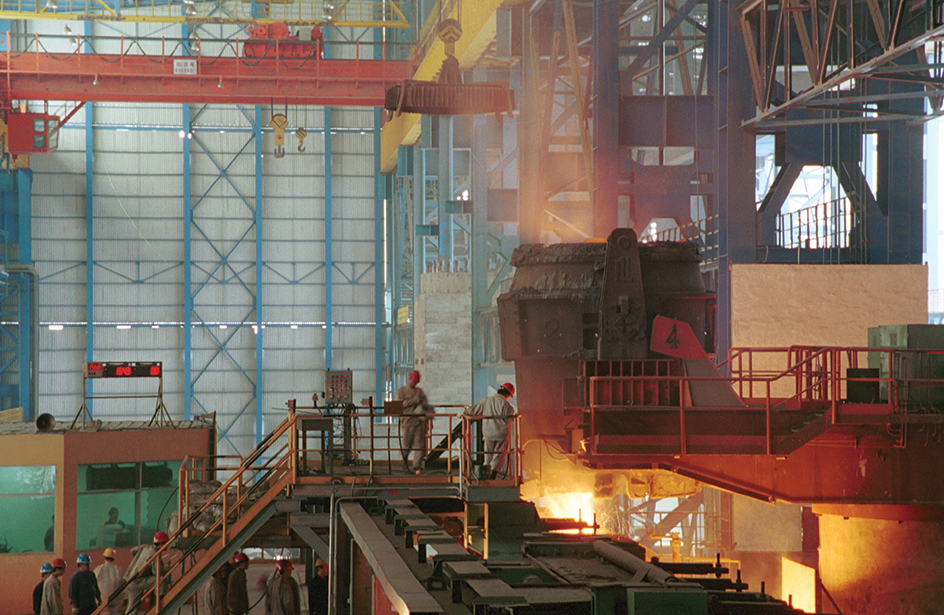
In Japan,
nearly all materials for steel production must be imported. The country’s steel mills are among the most modern and efficient in the world. Japan exports about 40 percent of the steel it produces. Its leading steel companies are Nippon Steel and Sumitomo Metal Corporation Group; JFE Steel Corporation; and Kobe Steel, Ltd.
In the United States,
nearly all the coal used by steel companies is domestic coal. United States steel companies import about 5 percent of their iron ore, mostly from Canada and Brazil. They also import such important alloying elements as chromium, cobalt, manganese, and vanadium. Nucor Corporation and the United States Steel Corporation are the country’s largest steel companies. The United States Steel Corporation operates not only steel mills but also coal mines, iron ore mines, limestone quarries, and transportation systems. Nucor Corporation operates many minimills. Minimills produce over half of the country’s steel.
Indiana is the leading steel-producing state, and Ohio ranks second in steel production. Together, these two states account for about 40 percent of the steel made in the United States. Other important steel-producing states include Illinois, Michigan, Pennsylvania, and Texas.
Nearly all employees in the steel industry below the level of management belong to one labor union, the United Steelworkers (USW). The USW, one of the largest labor unions in the United States, has done much to gain higher wages and better working conditions for steelworkers.
The United States government regulates the steel industry in a number of ways. It sets federal standards for emissions of pollutants from plants. The Occupational Safety and Health Administration (OSHA) establishes regulations to protect the health and safety of workers. From time to time, the U.S. government has also taken actions to control the price of steel.
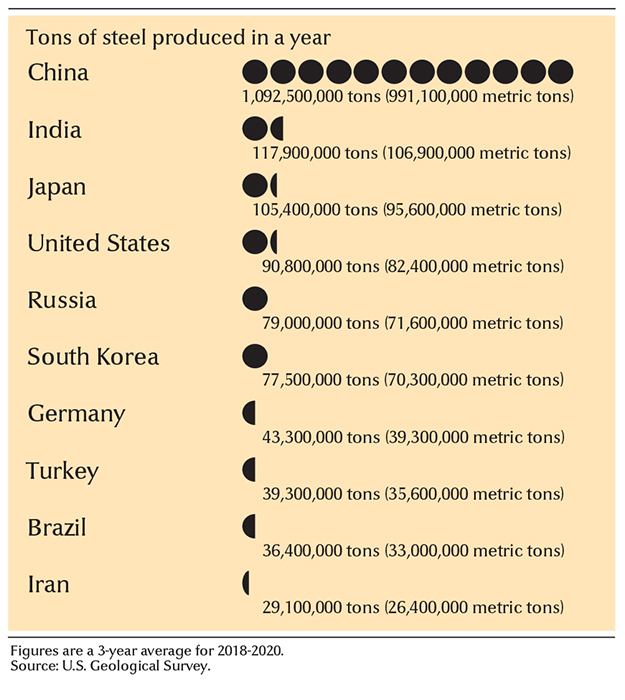
In other countries.
Other major steel-producing nations include Brazil, Germany, Russia, South Korea, and Turkey. Before about 1950, the less developed countries imported nearly all their steel from the United States and other major industrial nations. Since then, however, many developing nations have established their own steel industries. This development has been especially important in countries that have plentiful natural gas and iron ore, such as Mexico and Venezuela. These nations operate plants that produce direct-reduced iron and refine it into steel in electric arc furnaces. Iran and India also make substantial amounts of direct-reduced iron. Blast furnaces produce most of Brazil’s iron, and the country uses basic oxygen furnaces and electric arc furnaces to make steel. South Korea’s POSCO, a private company that began as a government-owned operation, is one of the world’s largest steel companies. Even in nations with limited raw materials, governments have helped establish modern steel industries.
Canada’s steel industry produces about 14 1/2 million tons (13 million metric tons) of steel annually. Ontario produces more steel by far than any other province. Quebec is also an important steel-producing province. Hamilton, Ontario, is the center of the Canadian steel industry.
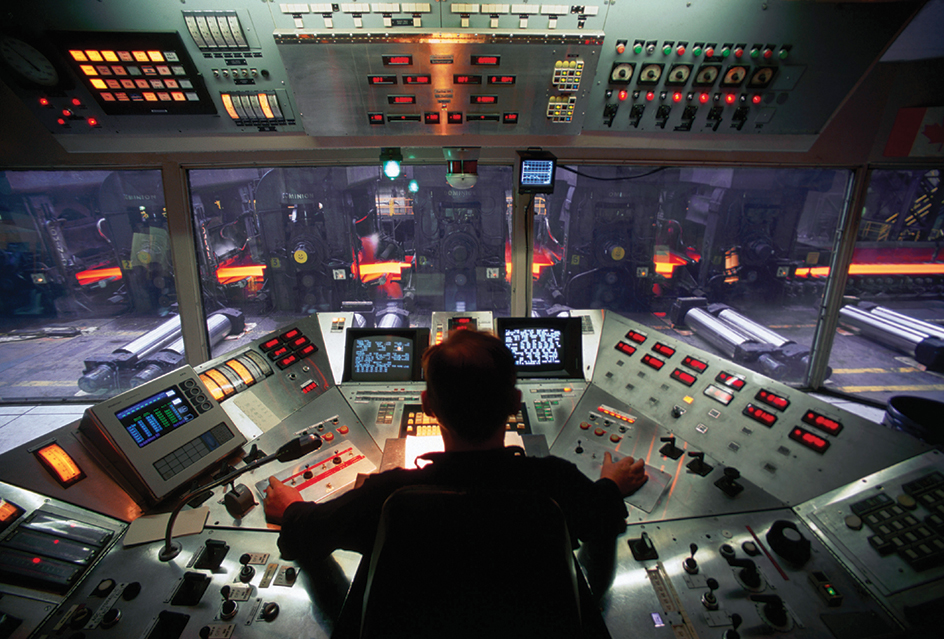
History
The Iron Age.
Prehistoric people obtained iron from meteorites and used it to make tools, weapons, and other items. In several early languages, the word for iron meant stone from heaven or star metal . People used such iron as early as 4000 B.C., but it is not clear when or where they first made iron by smelting ore.
The first people known to have large supplies of iron were the Hittites, who lived in what is now Turkey. By about 1400 B.C., they had learned to make iron weapons and tools. People in China and India also developed methods of making iron. By 1000 B.C., many of the world’s civilizations knew ironmaking techniques, and the Iron Age was well underway (see Iron Age ).
The early ironmaking furnaces were shallow, bowl-shaped hearths in which people heated iron ore and charcoal. After several hours, the ore released its oxygen to the surrounding hot carbon and formed small spongy bodies of metallic iron. But before it could be used, this iron had to be reheated and hammered repeatedly to force out the remaining hard, brittle impurities. By 1200 B.C., ironworkers could reheat, work, and cool this iron to make wrought iron, which could be hammered into useful shapes.
Ironmakers soon learned that blowing air into the furnace made the fire hotter and thus improved the quality of the iron. Later, they used a device called a bellows to blow air through openings into the furnace. In the A.D. 700’s, ironworkers in Catalonia, in what is now northeastern Spain, developed a better type of hearth furnace, called the Catalan forge. A water-powered pump forced air in at the bottom of the furnace. The Catalan forge made up to 350 pounds (160 kilograms) of iron in five hours, far more than earlier furnaces could make.
Historians believe that by about the 400’s B.C., the ironworkers in China had developed furnaces that could melt ore to make liquid cast iron. The ironworkers would pour this iron into molds to make various objects. The Chinese were the first ancient people to shift from making wrought iron to making mostly cast iron. In China during the Han dynasty, which ruled the country from 206 B.C. to A.D. 220, the use of cast iron became widespread. Ironmakers cast such varied products as cooking pans, weapons, plows, and many kinds of tools. They made cast iron in small furnaces, into which a bellows blew air. These furnaces were perhaps 7 feet (2.1 meters) in height. The Chinese probably began smelting with coke about the time of the Song dynasty, also called Sung, which ruled China from 960 to 1279. Blast furnaces, with tall brick or stone shafts up to 30 feet (9 meters) in height, appeared in China by the 1300’s. About this same time, the Chinese began making cast-iron firearms.
Blast furnaces developed independently in Europe. They evolved from earlier methods of smelting iron. European ironmakers built many types of shaft furnaces. A typical shaft furnace around 1350 was probably between 10 and 16 feet (3.0 and 4.9 meters) in height. Workers dumped iron ore and charcoal into the top of a brick-lined shaft, which was 3 to 4 feet (0.9 to 1.2 meters) across at its widest point. Often these furnaces produced the standard spongy masses or “blooms” of wrought iron. But if temperatures were high enough and the metallic iron absorbed enough carbon from the fuel, the furnace would instead produce carbon-rich molten cast iron.
By around 1450, ironmakers, especially those in long-standing ironmaking districts in Italy, France, and Germany, were using blast furnaces to produce sizable amounts of molten cast iron. About that time, Europeans began casting iron into cannons, pans, and many other types of new iron goods. During the 1700’s, a shortage of wood forced British ironmakers to begin using coke instead of charcoal in their blast furnaces.
The English colonists brought ironmaking with them to the New World. An ironworks operated briefly on the James River in Virginia before being destroyed during an Indian raid in 1622. In 1646, the first successful North American ironworks opened in what is now Saugus, Massachusetts. It continued to produce iron until 1668. By 1775, plentiful supplies of charcoal and iron ore had enabled American blast furnaces to reach an annual output of 30,000 tons (27,000 metric tons) of cast iron. This production accounted for 15 percent of the world’s annual production of cast iron.
The first steel.
People made small amounts of some forms of steel during the early part of the Iron Age. For example, the Haya people of eastern Africa made steel in a cone-shaped furnace driven by bellows. In southern India, as early as 300 B.C., a type of carbon steel called wootz steel was made by heating and melting high-grade ore with wood chips or charcoal in closed crucibles or by melting cast iron and wrought iron together. By the A.D. 500’s, the Chinese were producing steel by melting bars of wrought iron with molten cast iron. Ironmaking was introduced into Japan from Korea, probably in the A.D. 300’s or 400’s. During the 700’s, Japanese sword makers began using Tatara steel, which the Japanese made from iron sands. By about the 700’s, Middle Eastern sword makers began to import wootz steel from India. They forged this steel into blades of fine layered steel that became known as Damascus steel.
Europeans used various cementing processes throughout the Middle Ages, which lasted from about the A.D. 400’s through the 1400’s. In cementing, two substances, such as iron and powdered charcoal, are heated together to produce a chemical change in one of them. The Europeans baked wrought-iron bars in sealed pots with charcoal or wood chips for seven days or more. The wrought iron absorbed carbon and became a type of steel known as cemented steel or converted steel. However, such steel was scarce and expensive.
In 1740, Benjamin Huntsman, a clockmaker from Sheffield, England, invented a crucible process for steelmaking. The carbon content of cemented steel was uneven, with more carbon near the surface, where the iron came into contact with the charcoal or wood chips. Huntsman melted cemented steel in sealed clay pots called crucibles at high heats. Huntsman’s process produced steel that was more uniform in quality and freer from impurities than any previously produced. But his method required a great deal of highly skilled labor. In addition, the largest crucibles could produce only about 100 pounds (45 kilograms) of steel. Still, steelmakers in Sheffield became world famous for their high-quality crucible steels.
The birth of modern steelmaking.
During the 1850’s, Henry Bessemer, a British inventor, developed the first method of making steel cheaply in large quantities. This method became known as the Bessemer process. An American ironmaker named William Kelly patented a similar process in the United States.
In the Bessemer process, workers took molten iron from the blast furnace and poured it into a large pear-shaped container called a converter. They then pumped a large blast of air into the iron through openings in the bottom of the converter. The oxygen in the air reacted rapidly with the carbon, silicon, and manganese in the molten iron. This action removed the impurities and converted the iron into steel. Robert Mushet, a British metallurgist, found that adding an iron-carbon-manganese alloy, called spiegeleisen, after the blowing process helped remove oxygen and adjust the steel’s carbon content.
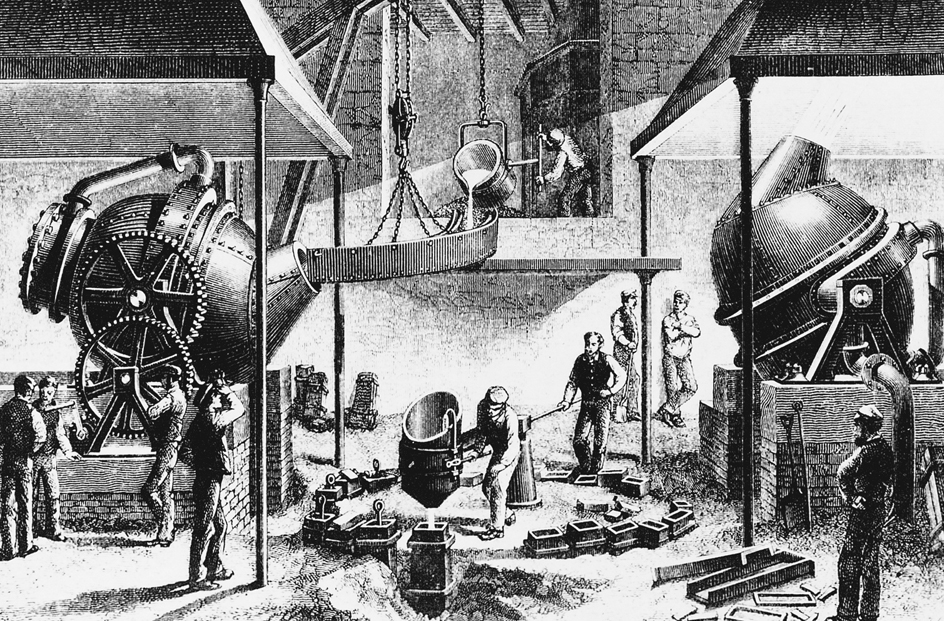
The Bessemer process was used in the United States for the first time in 1864. By 1880, the method accounted for more than 90 percent of U.S. steel production.
The open-hearth process appeared soon after the Bessemer method became widespread. In 1861, Charles William Siemens, a German-born scientist living in the United Kingdom, proposed melting steel in a gas furnace his brother Friedrich had patented several years earlier. This furnace, called a regenerative gas furnace, used hot waste gases to preheat the fuel and air put into it. In 1864, two French brothers, Pierre and Emile Martin, made steel in a furnace that incorporated the Siemens regenerative design. The resulting Siemens-Martin, or open-hearth, process had many advantages over the Bessemer process. Most importantly, it produced steel from scrap and allowed greater control over the chemical composition of the product. Few Bessemer plants were built after 1910, but existing ones continued to operate until the 1960’s.
In 1878, William Siemens demonstrated that steel could be melted in an electric arc furnace. But at that time, electric power was limited in supply and was extremely expensive. In 1899, Paul L. T. Heroult of France, who had invented an electric process for making aluminum, opened the first steel mill equipped with electric arc furnaces.
Growth of the steel industry.
After the introduction of the Bessemer and open-hearth processes, steel manufacturing expanded rapidly. Germany and the United Kingdom became the leading European steel producers.
Rich iron ore ranges opened in the Lake Superior region of the United States, and that nation’s annual production of steel increased tremendously. Between 1880 and 1910, production rose from about 1,400,000 tons (1,300,000 metric tons) to more than 24 million tons (22 million metric tons). In 1875, Andrew Carnegie’s Edgar Thomson Works went into operation in Braddock, Pennsylvania. This steel plant’s design served as the model for many later plants. Carnegie later built or bought up a number of other steel plants.
In 1901, Carnegie sold his mills to the newly formed United States Steel Corporation. Through this purchase, U.S. Steel gained control of 60 percent of the nation’s steelmaking capacity. But its share of the industry gradually declined as other major steel firms grew.
Much of the steel produced in the late 1800’s was used to make rails for the railroads of the United States and Europe. During the 1900’s, production continued to increase to meet the rising demand for steel for automobiles, ships, skyscrapers, and countless other products. Other developments included new processes for rolling steel and the creation of new alloys.
Most of the world’s major steel industries, except that of the United States, were severely damaged during World War II (1939-1945). As a result, U.S. companies dominated world steel production during the postwar years. However, Japan and many European nations rebuilt their steel plants in the 1950’s and 1960’s. The new mills used the most modern and efficient techniques, including the basic oxygen process and continuous casting. This modernization gave the Japanese and European steel industries an advantage over the American industry, which was slow to adopt the new techniques.
The U.S. steel industry faced many difficulties during the 1980’s. Competition from imported steel and declining domestic consumption reduced demand for U.S.-made steel. Many plants were forced to close. Some mills continued to operate using outdated equipment and production methods. By the 1990’s, several large U.S. steel companies had modernized their facilities enough to compete effectively in the world market. Minimills sprang up, and by the early 2000’s, they had surpassed integrated steel mills in total steel production. In the early 2000’s, the United States imported nearly 30 percent of the steel it consumed.
Recent developments.
During the late 1900’s and early 2000’s, steelmakers and steel processors in many countries suffered financially because of unprofitable pricing. Prices for hot-rolled coil steel, a common form of steel made and sold worldwide, fell by nearly half between 1995 and 2001. In the United States, many companies sought bankruptcy protection. During 2002 and 2003, the U.S. government imposed duties of up to 30 percent on many steel imports to help protect U.S. companies. Steelmakers in some countries responded to financial difficulties by merging to create larger companies. For example, steelmakers in France, Luxembourg, and Spain merged to form Arcelor. Other companies expanded into markets outside their home countries. For example, LNM Group of the Netherlands and its London-based subsidiary Ispat International operate plants outside of Europe. In 2004, the two merged to form Mittal Steel. In 2006, Mittal Steel merged with Arcelor to form ArcelorMittal, now the world’s largest steelmaker, with plants in Asia, Africa, Europe and North and South America.
World steel production has continued to rise, primarily because of rapidly expanding output in the developing nations of South America and Asia. By the early 2010’s, yearly steel production exceeded 1.5 billion tons (1.4 billion metric tons).