Leather is a tough, flexible material made from the skin of animals. Cattle hides provide the source of most leathers, but deer, goat, pig, and sheep skins are also widely used. Specialty leathers are made from alligator, crocodile, shark, and snake hides. The process of turning the animal skin into a leather product that can be made into useful objects is called tanning.
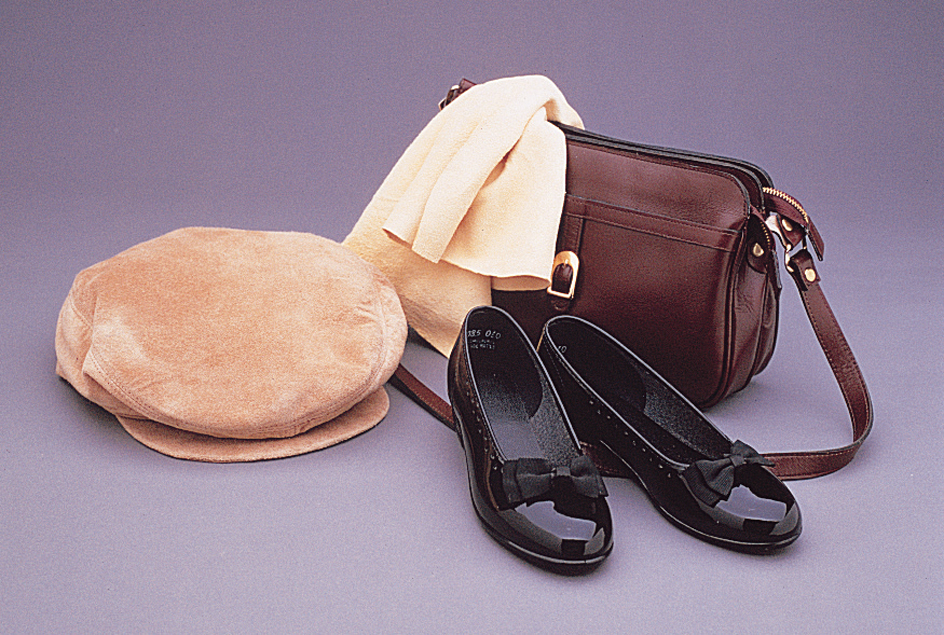
Leather is used to make shoes, boots, belts, gloves, jackets, hats, shirts, trousers, skirts, purses, and many other objects. Baseballs, basketballs, and footballs have leather covers. Industries use drive belts made from leather, and automobiles, trucks, and buses run on bearings protected by leather seals.
Leather is strong and durable. It can be made as flexible as cloth or as stiff as wood. Some kinds of leather are thick and heavy, but other kinds are thin. Leather can be dyed, polished until it has a glossy finish, or embossed (decorated with raised figures).
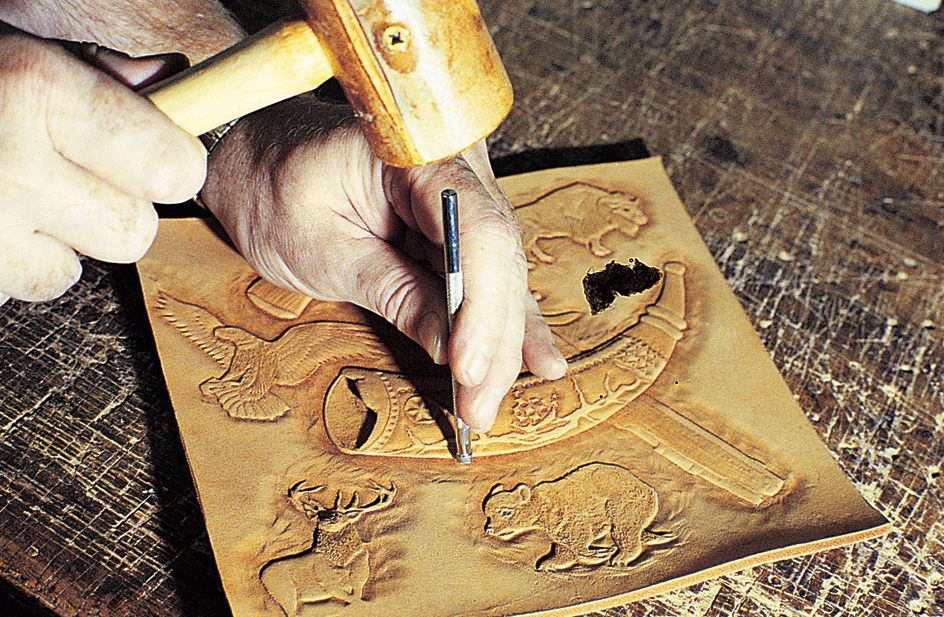
People have known how to make leather since prehistoric times. Some tanning methods that were developed by the ancient Greeks and Romans are still in use. Today, the United States is one of the world’s largest producers of leather. New York, Massachusetts, California, and Wisconsin are the country’s leading leather-producing states.
Kinds of leather
The chief kinds of leather are shoe sole leather, shoe upper leather, chamois, and suede. Shoe sole leather is produced from the thick skins of cattle and other large animals. Shoe upper leather is obtained from the thinner skins of calves, goats, and other smaller animals or by splitting heavy hides into thin layers. About 80 per cent of all tanned leather is made into shoes.
Chamois leather was originally made from the chamois, an animal that resembles the antelope. But today, most chamois leather is made from split sheepskin. Properly tanned chamois leather is as soft as cloth and will hold water like cloth. Chamois leather is often used as a washing and polishing cloth.
Suede is the inside flesh layer of a hide that has been split. Suede has a soft texture, and it can be brushed to enhance this texture. Most suedes are thin and are therefore flexible and pliable. Gloves, hats, shoe uppers, and jackets are often made of suede.
How leather is made
Preparing the hides.
Before animal hides can be tanned, they must undergo certain preparations. These preparations include (1) curing, (2) fleshing, (3) unhairing, and (4) bating.
Curing.
Most animal hides used to make leather come from a meat packer or slaughterhouse. Many of the skins used in the United States are imported.
The skins are cured before they go to the tannery to keep them from rotting. Hides are cured by applying salt to the flesh side of the skin, by soaking them in brine (salty water), by partly drying and salting them, or by just drying them. After they are cured, the skins are stacked in revolving drums filled with water. The water removes dirt and blood, washes out most of the salt, and replaces moisture lost in the curing process.
Fleshing.
After the skins are washed and remoisturized, they are fleshed. Workers run the hides across a fleshing machine equipped with sharp knives, removing all fat and meat on the flesh side of the skin. More and more hides are being fleshed at the packing house, thereby eliminating the fleshing step at the tannery.
Unhairing.
Workers put the fleshed hides in vats containing a lime and water solution that has a small amount of sodium sulfide. The solution weakens the hair roots, and in a few days the hair is loose. The hides are then run through a machine that scrapes the hair away. The hair is kept for use in making felt and other products. After unhairing, the hides are refleshed to remove bits of fat loosened by the unhairing process. Then, they are washed in clean water.
Bating.
After unhairing, the skins are bated—that is, they are placed in a mild acid bath to neutralize the unhairing solutions left in them. This process is necessary because the solutions used for tanning are acidic. If the alkaline solutions used for unhairing were not neutralized in this way, they could prevent the tanning solutions from penetrating the skin. Enzymes are also added to the bath to digest soluble proteins in the hide that could interfere with the tanning process.
Tanning.
After the hides have been cured, fleshed, unhaired, and bated, they are ready for tanning, which is done to prevent further decomposition of the material in the hide. There are four chief methods of tanning hides: (1) vegetable tanning, (2) chrome tanning, (3) combination tanning, and (4) oil tanning.
Vegetable tanning
is generally carried out in large vats filled with tanning solutions, which are made from water and tannin. Tannin is a bitter substance that is obtained from such plants as the chestnut, hemlock, mangrove, oak, and quebracho trees.
Workers increase the strength of the tanning solution in proportion to the time the hide is left in the solution. Tanning solutions commonly start at about 0.5 per cent tannin and are increased to as much as 25 per cent tannin by the completion of the tanning process. Vegetable tanning usually takes from one to three months, but thick skins are sometimes tanned for a year.
Vegetable-tanned leather is firmer and more water-resistant than chrome-tanned leather. Vegetable-tanned leather may be stuffed—that is, materials such as fats and oils may be worked into it. Stuffing makes the leather water-repellant and more resistant to wear. Vegetable-tanned leather is made into bookbindings and heavy belts for machinery. Pure vegetable tanning is also used for such specialty leathers as basil, made from sheepskin; some pigskin; and buffalo, ostrich, rhinoceros, and walrus hides.
Chrome tanning
is the most widely used mineral tanning process. It is performed with a tanning solution of chrome salts (compounds of chromium). Before skins are chrome tanned, they are pickled (soaked in a solution of sulfuric acid and salt). The skins are soaked until their acidic content reaches a predetermined level. Then they are removed and washed. After washing the skins, workers place them in tanning drums filled with water and chromium sulfate. This solution tans the skins and also gives them a light blue color. The skins are usually completely tanned in a few hours.
Chrome-tanned leather can be made much faster than vegetable-tanned leather. It is also more resistant to heat and scratching, more flexible, and easier to soften. Leather for shoe uppers, gloves, wallets, luggage, and upholstery is generally chrome tanned. However, some of these leathers are retanned with syntans (synthetic tanning materials), vegetable-tanning solutions, or substances containing formaldehyde, to give them special characteristics.
Combination tanning
involves the use of both the chrome-tanning and vegetable-tanning methods. Combination tanning is used for leathers with special qualities, such as extremely soft garment, glove, or shoe upper leathers. In today’s tanneries, most leather is chrome tanned, either as the complete tanning process, or as a pretan for vegetable tanning. Pretanning speeds up the vegetable-tanning process and also gives vegetable-tanned leather more flexibility. Some shoe soles are vegetable tanned, but usually they are pretanned with a chrome tan.
Oil tanning
is used for the chamois leather that is made from sheepskin. First the wool is removed from the sheepskin and the skin is split into layers. The flesh split (side) is used for chamois, and workers begin by shaving the split to remove the fat cells. Next, they put the shaved split into a machine that hammers cod-liver oil into the skin. After the oil has penetrated it, the skin is removed from the machine and dried. It is then buffed to soften it and to give it a nap (soft, woolly surface). Saddle leather and leather seals used on some machinery are also oil tanned. However, they are pretanned with chrome before being oil tanned.
Final processing
that is carried out after the skins are tanned includes (1) splitting, (2) dyeing, (3) staking, and (4) finishing.
Splitting.
The tanned skins are removed from the tanning materials and dried. Some are then split by a machine that cuts the skins into two layers. The top layer is called top grain. The bottom, or flesh, layer is often called suede leather. The skin is further divided into four sections. The bend section is the skin on either side of the backbone from the rump to the shoulder. The bend section provides the finest leather. The shoulder section is also fine leather, but it often is wrinkled. The head section is good leather, but the pieces are small and uneven. The belly section is poorest in quality because it is uneven and tends to stretch.
Dyeing.
Almost all leather is dyed after tanning. Dyeing is often done in large drums similar to those used in chrome tanning. Leather can be dyed with a number of aniline dyes, natural wood dyes, acid dyes, and even some tanning agents. The dyeing takes place while the skin is being tumbled with a mixture of warm water and the dyeing material. Oil is usually added to further soften the skin. This process is called fat-liquoring. After the hide is dyed and fat-liquored, it is dried in drying vats, by pasting the hide onto a glass plate or a metal sheet. The hide may also be dried by toggling (pinning) it to a large wooden sheet with holes in it.
Staking.
Some leather must be made softer after it is dyed. The dried skin is partially remoisturized by putting it in a room with a highly humid atmosphere, or by covering it with damp sawdust or a similar material. Then it is put on a staking machine, where steel pegs stretch and work the leather to soften it. If extremely soft leather is desired, it is tumbled in wooden drums. Glove leather is often softened in this way.
Finishing.
After staking, the leather is ready for the final finishing process. Casein (a protein found in milk), other substances obtained from blood and milk, waxes, and oils are some of the materials used for a final finish on leather. The finish is sprayed on in layers. Between applications, a cylindrical piece of glass or steel is rolled over the leather to smooth and glaze it. The most highly polished leather is called patent leather. It is produced by applying successive coats of heavy oil varnish at the end of the finishing process. This varnish gives patent leather a high, durable gloss.
History
People have tanned animal skins since prehistoric times. The ancient Egyptians made such durable leather that specimens over 3,000 years old have been discovered in almost perfect condition. Evidence of oil tanning has been found in leather from Egyptian tombs. The early Greeks and Romans also made contributions to the science of leathermaking. Some of their methods are still in use today.
Many ancient peoples tanned their leather by placing layers of bark, leaves, and fruit over hides and adding water. This process took months, and in the case of thick skins, even years. As early as 800 B.C., people discovered the mineral salt alum and began using it as a tanning agent. The Assyrians, Babylonians, Greeks, and Sumerians used this mineral method of tanning because it was much faster than previous techniques.
The American Indians used deerskins to make leather for their moccasins, cloaks, and tents. Colonial settlers refined the leathermaking process, and leather became one of the most widely used materials in the U.S. territories.
In 1809, Samuel Parker, an American inventor, patented the leather splitting machine. This machine allowed workers to make two skins out of one, thereby doubling production. Fleshing and unhairing machines were invented shortly after the splitting machine.
Manufacturers did not begin producing leather for a large market until the 1800’s. In the United States, leather became more widely available as the standard of living rose. As more cattle began to be consumed for meat, more hides became available for tanning. Augustus Schultz, an American dye salesman, invented a chrome-tanning process in 1884. The method was perfected about 10 years later by Martin Dennis. Chrome tanning allowed more attractive and flexible leathers to be produced at a much faster rate.
Because of the increasing demand for leather, researchers have developed synthetic leather, which is generally created from a film of synthetic material. Synthetic leather closely resembles natural leather and has many uses. It does not, however, have natural leather’s ability to breathe—that is, to allow perspiration to escape from the body. Some synthetic suede fabrics, however, have a film layer with micropores through which perspiration can escape as a vapor.