Lumber includes boards and larger pieces of wood that have been sawed from logs. In many countries, the term timber is used to refer to such pieces of wood, but this term can also refer to standing trees, logs, and unprocessed wood. Builders use at least some lumber in the construction of every house. Lumber furnishes material for framing, flooring, siding, woodwork, doors, and other building parts. In industrialized countries, most lumber is used for building construction, remodeling, and repair. The rest goes from sawmills to factories that make boxes, crates, furniture, tool handles, toys, and hundreds of other products.
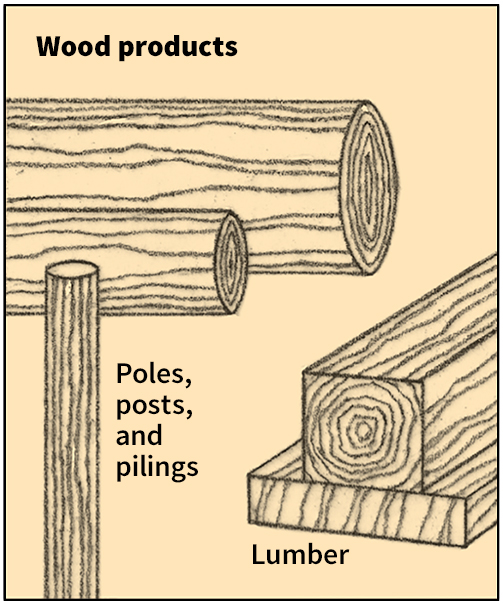
Every time a piece of wood is cut at a sawmill, the cutting produces sawdust and small chips of wood. These leftover bits of wood can be made into many valuable products. Often mills send wood scraps and small logs through a chipper. Pulp mills grind the chips or treat them with chemicals to change them into wood pulp. Manufacturers use pulp to make paper, hardboard, plastics, rayon, and other products. Sawdust and bark are often used for fuel. For a description of the products obtained from trees, see Forest products .
The lumber industry employs thousands of people to harvest trees, transport logs to mills, saw logs into lumber, and sell the lumber. The United States is one of the world’s leading lumber producers. It uses a total of about 55 billion board feet (130 million cubic meters) of lumber every year. A board foot equals 144 cubic inches—a volume equivalent to that of a board measuring 1 foot by 1 foot by 1 inch. This volume equals approximately 0.0024 cubic meter.
Kinds of lumber
Lumber is divided into two main classes: softwood and hardwood. These classes are not based on the softness or hardness of the wood. Rather, they refer to the kind of tree from which the lumber came. Some softwood lumber is harder and heavier than many hardwoods. The term lumber is sometimes used to describe wood boards and timbers made by gluing together smaller pieces of wood. This kind of lumber is called engineered lumber or composite lumber.
Lumber is also classed by its condition. Rough lumber has straight sides and edges but is rough and splintery. Dressed lumber comes in smooth, evenly cut boards. Worked lumber is dressed lumber that has a design cut in it for decoration or to make boards fit together.
Softwood lumber
comes from conifers, trees whose seeds develop in cones (see Conifer ). Common conifers include pines and firs, which are also called evergreens, and cedars, cypresses, and larches. Softwood lumber is used for wall, floor, and roof supports; door and window frames; other building materials; and boxes.
Softwood lumber can be classified according to its use. For example, carpenters use framing lumber to build houses. Structural lumber can stand heavy strain. It is used for posts, planks, joists, and beams. Sawmills usually sell factory and shop lumber directly to factories for making boxes, spools, and other products.
Hardwood lumber
is sawed from broad-leaved trees. These trees are usually deciduous, which means they lose their leaves in autumn (see Deciduous tree ). Hardwoods used for lumber include ash, aspen, beech, birch, cherry, chestnut, cottonwood, elm, hickory, maple, oak, sweet gum, tuliptree, tupelo, and walnut. Hardwoods are used in making furniture, cabinets, paneling, flooring, and trim. They are also used for such items as baseball bats and tool handles. Tropical hardwoods, such as ebony, mahogany, rosewood, and teak, are used to make high-quality furniture.
Much hardwood lumber is sawed into small pieces, without defects, called hardwood dimension parts. Manufacturers use hardwood dimension to make chair arms, piano legs, and other furniture parts. If factories want plain blocks of hardwood, they order rough hardwood dimension. Trimmed, molded, or sanded wood is surfaced hardwood dimension. If manufacturers want parts of a chair, such as legs, arms, or seats, ready to be assembled, they order finished market products.
Engineered lumber
is made by combining wood with at least one other material under high pressure. The wood used may be veneers—long, paper-thin strips—or smaller pieces of shaved wood, chips, or sawdust. Glues, resins, or plastics are typically used as the combining material, but other types of materials may be added to give the lumber special properties. Engineered lumber is made to standard lumber dimensions. It includes plywood, particleboard, and several types of composite structural lumber.
From forest to sawmill
People who work in lumbering operations are generally called loggers or forest workers. Large-scale lumbering operations, such as those owned by many forest products companies, require special mechanical equipment and technical knowledge.
Cutting down trees.
Before loggers go into the woods, a forester decides which trees they should cut, and marks those trees. The decision to cut is determined by the species, age, and size of the trees. The forester is a professional trained in managing forests for a variety of purposes. The forester tries to grow crops of trees so that they will yield the greatest possible amount of lumber while preserving wildlife habitat and other qualities of a forest. He or she also knows how to protect forests from insects, disease, and grazing animals. See Forestry .
Loggers called fallers or fellers cut down, or fell, trees that the forester has marked for cutting. The power saw a faller uses can slice through a tree trunk in a few seconds. In cutting down a large tree, the faller first makes an undercut by cutting a wedge-shaped piece from the tree trunk with an ax or power saw. The faller makes the undercut on the side of the tree that is to fall toward the ground. The cut is made close to the ground to avoid wasting valuable wood by leaving a high stump. After the saw has cut through the trunk, the undercut makes the tree fall toward that side. Expert fallers can drop a tree exactly where they want it. They can avoid striking other trees or hitting stumps that might break or damage the trunk of the falling tree.
After a tree has been felled, loggers cut the trunks into shorter lengths, so that they can take them out of the forest more easily. Loggers who perform this task are called buckers. They use axes or power saws to lop off the limbs. Then they saw the trunks into logs from 8 to 40 feet (2.4 to 12 meters) long.
Large modern machines simplify logging work. For example, hydraulic tree shears quickly cut through a tree like giant scissors. These shears are built into tractors that move from tree to tree. Other machines do more than one job. Some tree harvesters can fell a tree, remove its branches, cut it into logs, and sort the logs in bunches.
Transporting logs
from the woods to the sawmill is the second step in logging. It consists of two operations. First, the loggers skid (drag or haul) or lift the logs to the landing (a central place in the woods). Then they transport the logs from the landing to the sawmill.
Workers typically use special tractors called skidders or long cables called draglines to skid the logs. A system called high-lead << leed >> logging uses pulleys and steel cables to drag logs up steep slopes or to swing them across ravines. The pulleys and cables are supported by portable towers and powered by giant diesel, steam, or electric winches. The cables pick up only one end of the log. The other end may drag along the ground. High-lead logging can bring logs to a landing as far away as 1,500 feet (460 meters). Other cable-logging systems can carry logs 2,500 feet (760 meters) or more. Such systems use cables called skylines that pick up the entire log rather than drag it. Logging with skylines does less damage to the forest floor than high-lead logging. Special carriers, such as hot-air balloons or helicopters, may be used where the ground is steep or the harvest area is difficult to reach.
After the logs reach the landing, they are piled until they can be moved to the mill. Trucks transport the largest number of logs to sawmills. If the landing is on a railroad line, flatcars transport the logs. In some regions of the world, if the landing is on the bank of a stream or river, workers may use chains to bind the logs into rafts that float to the mill. In other regions, loggers use sledges to carry logs over icy roads in winter.
From sawmill to lumberyard
The total world production of sawed wood is about 205 trillion board feet (480 million cubic meters) a year. A trillion equals a million million. Most of the world’s lumber comes from stationary mills that operate from a building. Small milling operations may use mobile sawmills, in which the headrig, or sawing machinery, is loaded on a truck trailer and hauled into the woods.
Mills store their logs on land and handle them with modern loading devices. If the logs will be standing for a long time, the mill sprays them with water to protect them from insects, fungi, stain, and fire.
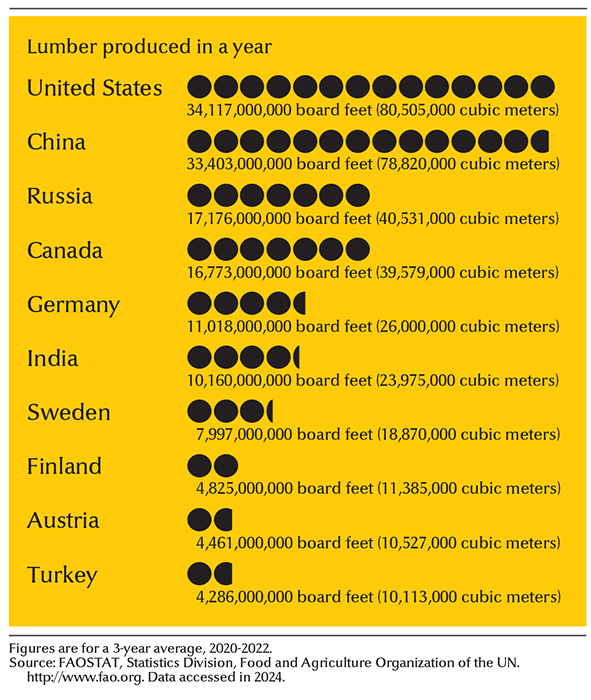
Sawing logs.
A moving conveyor chain or belt carries the logs into the mill. In some mills, water jets first clean the logs so that bits of sand, dirt, or metal do not dull the saws. In most mills, a log debarker removes the bark before the log reaches the first saw, called a headsaw. The bark must be removed because it is dirty and can dull saws. Bark also lowers the value of the pulp chips made from outer slabs of the log. One kind of debarker has metal bars or knives that rub off or chip off the bark. Another kind tears off the bark by the force of water shot onto the log under high pressure.
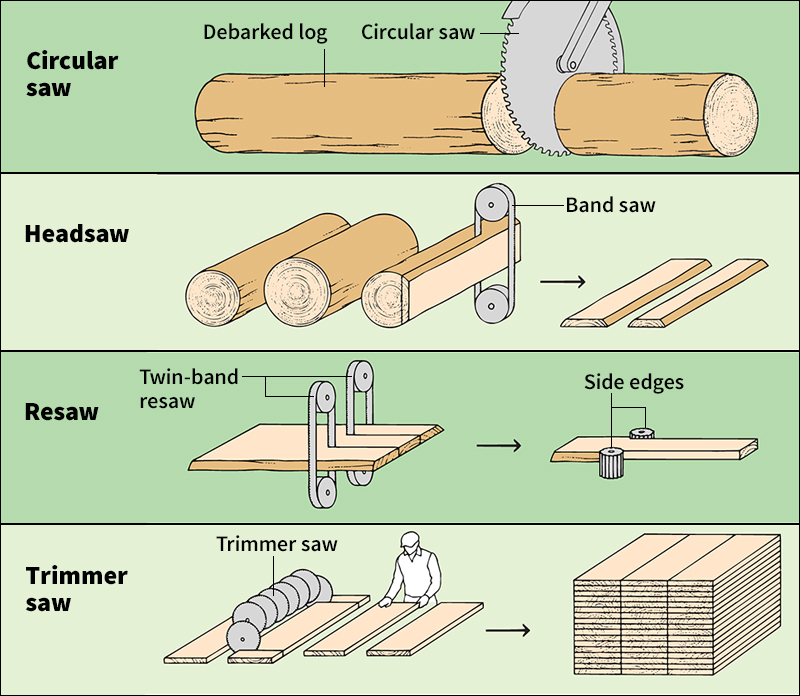
As a log enters the sawmill, an electronic scanner may examine it and accurately measure its diameter and shape. Computers calculate how the log should be cut. Large logs are then moved onto a platform called a carriage. The carriage looks somewhat like a small railroad flatcar and is mounted on tracks. It carries the logs back and forth past the headsaw. Each time the carriage goes past the saw, the saw slices off a board until the log has become a pile of boards. Small logs may be cut into lumber by gang saws. After the outer slabs of a log have been removed, this group of saws cuts the log into boards of the desired thickness in one operation.
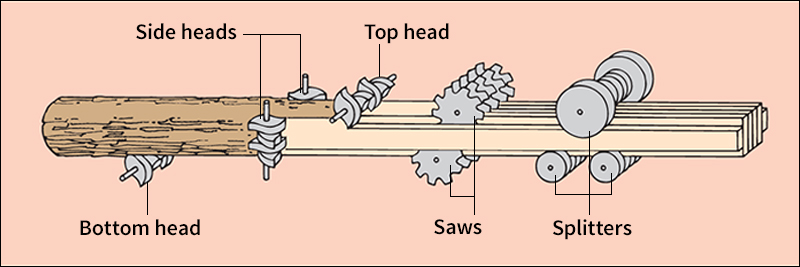
Moving belts carry the newly made boards, called green lumber, to the edger, a set of smaller saws. The edger trims the rough edges from each board and makes the sides straight and even. Next, the edged boards go to a set of saws called the trimmer. It makes the ends of the boards square, and cuts the boards to the exact lengths ordered by lumber dealers. The trimmer also cuts off weak or bad spots.
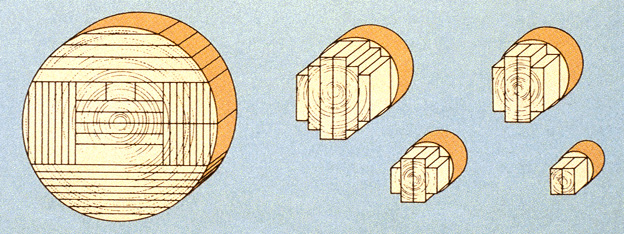
Grading lumber.
The green boards, now called rough lumber, ride slowly on a conveyer belt sometimes called the green chain. Workers called graders walk along the belt, examining the boards and sorting them according to size, quality, and kind of wood. Or a computerized grading system may automatically scan, grade, and mark the lumber.
Lumber is graded differently in different countries or regions. For example, the Scandinavian system, which is widely accepted in Europe, has four basic grades for sawed wood. Grades A1 through A4 represent the best lumber. Grades B, C, and D are for inferior timber. In the United States, the National Hardwood Lumber Association uses seven grades to classify hardwood. They are, from highest to lowest: (1) firsts and seconds (FAS), (2) selects, (3) No. 1 common, (4) No. 2 common, (5) sound wormy, (6) No. 3A common, and (7) No. 3B common.
Hardwood grades are typically based on the proportion of the wood that can be used to manufacture various products. If a large proportion can be used, the lumber receives a high grade. Hardwood finished market products, such as flooring and stair treads, are graded for their particular use. A high-grade piece of such lumber goes through little or no manufacturing.
Softwood-lumber associations use various grades for their lumber. Yard-lumber grades include selects, or finish, in grades A (highest quality) through D; common boards, numbered 1 through 5; and common dimensions, numbered 1 through 4. The lower numbers designate lumber of higher quality. Softwood factory lumber and shop lumber are graded for appearance. Softwood structural lumber is graded according to the load it can carry when used as beams, frames, joists, or planks.
Seasoning
lumber means removing excess moisture from the wood. More than half the weight of green lumber may come from moisture in the wood. After seasoning, less than a tenth of the weight of the lumber may come from moisture. Mills also ship lumber without seasoning. But for most uses, the moisture must be removed so that the wood will not warp. In the process, the wood shrinks in size.
Mills sometimes season lumber by air drying. Workers stack the wood outdoors to let the sun and wind dry it. A quicker way of seasoning lumber is to put green lumber in dry kilns, or special heated buildings in which instruments control the temperature and moisture of the air. The instruments tell how much moisture remains in the wood. Some mills use both drying methods.
Planing.
A small amount of rough lumber for use in construction is shipped directly to lumber dealers. But the rest of the lumber must pass through a planing mill before it goes to market. In a planing mill, boards pass through machines that have sharp knife blades or large abrasive (rough) sheets. The knives or sheets rotate against the rough boards, smoothing the surface. Lumber also receives further treatment to make it into dressed lumber or worked lumber.
Shipping.
Most mills ship lumber to wholesale dealers. The wholesalers sell to retail lumberyards, to factories that make wooden articles, and to construction companies. Railroads do most long-distance hauling of lumber. Trucks make most of the short lumber-carrying trips.
Buying lumber
When selecting lumber, buyers should keep in mind the work they want it to do and the effect they wish to achieve. Lumber for decorative use should be chosen for its color, grain, knots, and texture. Construction applications require strong and durable lumber. Different kinds of wood are used for various types of construction. For example, Douglas-fir and pine are used for structural timbers. Spruce, fir, and hemlock are used for framing lumber. Oak and maple are popular for flooring, and redwood and redcedar make fine siding.
In most countries, lumber is measured before it is seasoned and planed, and so the finished pieces are actually smaller than the nominal (named) size. Standard nominal sizes differ depending on the country of origin and the type of wood and its purpose. In the United States and some other countries that use the inch-pound system of measurement, the width and thickness of lumber are expressed in inches, and the length in feet. For example, the nominal size of a 2 by 4 by 12 board is 2 inches (5 centimeters) thick, 4 inches (10 centimeters) wide, and 12 feet (3.66 meters) long.
Mills cut hardwood lumber into a variety of widths and into lengths that can be divided evenly into 1-foot (30-centimeter) sections. Softwood structural lumber is cut into lengths that can be divided evenly into 2-foot (60-centimeter) sections. Its nominal widths range from 2 to 16 inches (5 to 40 centimeters). The nominal thickness of any lumber classifies it as a board, dimension lumber, or a timber. Boards have a nominal thickness of less than 2 inches; dimension lumber ranges from 2 inches to, but not including, 5 inches (13 centimeters); and timbers measure 5 or more inches thick. Lumber is generally priced by the board foot. The width and thickness of a finished 2 by 4 is actually only about 1 1/2 by 3 1/2 inches (3.81 by 8.89 centimeters).
In countries that use the metric system, the width and thickness of lumber are measured in millimeters or centimeters, and length in meters. Lengths can often be divided into 0.3-meter (1-foot) sections.
The names of classifications based on lumber thickness—and sometimes width—differ from country to country. For example, many countries refer to dimension lumber with a width of more than 4 inches (10 centimeters) as planks and to timbers as balks or baulks. Some countries do not use nominal sizes but rather sell lumber according to the actual dry size for thickness and width. Thickness and width are often rounded off to the nearest millimeter.
History
For thousands of years, forests have contributed to human progress. Prehistoric people built homes out of branches or logs. They used wood as handles for their tools and weapons. Planks cut from logs were joined by crosspieces and rounded to make wheels for early carts. Logs fastened together formed rafts. Wood used as fuel provided warmth and a means of cooking.
Writings, paintings, and sculptures from ancient times serve as records of early uses of lumber. In a relief in the great temple at Karnak in Ancient Egypt, Phoenician princes are shown felling trees for the Egyptian conqueror. A relief in an Assyrian palace shows large logs being transported by sea. Trajan’s Column in Rome, which dates to A.D. 113, includes illustrations of soldiers cutting down trees, carrying timber, building a bridge, and constructing wooden walls.
Boards cut over sawpits in Europe in the 1100’s or earlier were probably the first manufactured boards. In a sawpit, one person stood beneath a log and another stood above it, at either end of a two-handled saw. The earliest sawmills were crude, water-powered mills. By the 1300’s, such mills were in use in many parts of Europe. Steam power replaced water power in the mills about 1830.
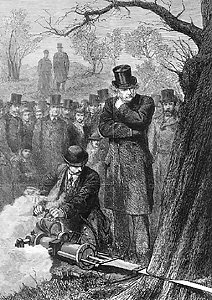
The pioneers of North America cleared vast forests as they moved westward. Lumbering was one of the first industries in the American Colonies. Lumberjacks, who cut down trees and delivered logs to the mills, became famous as strong, hearty, courageous workers. Many legends sprang up about their exploits as they cleared forests and took logs to the mill by ox team, by raft, or by guiding them down rushing streams after spring thaws (see Bunyan, Paul ). Loggers lived in bunkhouses in logging camps where there were few comforts. The colonists traded with Europe. They exported logs, hoops, clapboards (thin overlapping boards used to cover outer walls), wainscoting (wooden panels used to line the lower walls of rooms), and naval stores (tar, turpentine, and other materials used in shipbuilding).
Today, lumber remains an important part of the world economy. It continues to be essential to the construction industry, which uses more lumber than any other industry.