Pump is a device that moves liquids and gases. Pumps are used in a variety of machines and other devices, including home heating systems, refrigerators, oil wells and water wells, and turbojet and automobile engines. The fluids that are moved by pumps range from air for inflating bicycle tires to liquid sodium and liquid potassium used for cooling nuclear reactors. Most pumps are made of steel or cast iron, but some of them are made of glass or plastic. Gas pumps are also called compressors, fans, or blowers.
The two main types of pumps are dynamic pumps and positive displacement pumps. Dynamic pumps maintain a steady flow of fluid. Positive displacement pumps, on the other hand, trap individual portions of fluid that are in an enclosed area before moving them along.
Dynamic pumps
Centrifugal pumps
consist of a motor-driven propellerlike device, called an impeller, which is contained within a circular housing. The impeller is a wheel of curved blades that rotates on an axis. Before most centrifugal pumps can start pumping liquid, they must be primed (filled with liquid). As the impeller rotates, it creates suction that draws a continuous flow of fluid through an inlet pipe. Fluid enters the pump at the center of the impeller and travels out along the blades due to centrifugal (outward) force. The curved ends of the blades then sweep the fluid to an outlet port.
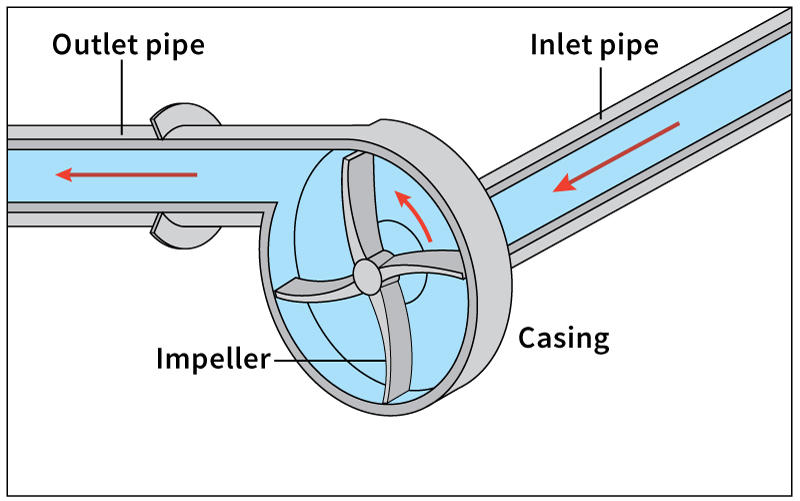
Centrifugal pumps are inexpensive and can handle large amounts of fluid. They are widely used in water distribution systems, chemical-processing plants, and oil refineries.
Axial-flow pumps
have a motor-driven rotor that directs fluid along a path parallel to its axis. The fluid thus travels in a relatively straight path from the inlet pipe through the pump to the outlet pipe.
Axial-flow pumps are most often used as compressors in turbojet engines. Centrifugal pumps are sometimes used for this purpose, but axial-flow pumps are more efficient. Axial-flow compressors consist of alternating rows of rotors and stationary blades. The blades and rotors produce a pressure rise in the air as it moves through the axial-flow compressor. Air then leaves the compressor under high pressure. See Jet propulsion (Turbojet) .
Jet pumps
get their name from the way they move fluid. These pumps operate on the principle that a high-velocity fluid will carry along any other fluid it passes through. Most jet pumps send a jet of steam or water through the fluid that needs to be moved. The jet carries the fluid with it directly into the outlet pipe and, at the same time, creates a vacuum that draws more fluid into the pump. The amount of fluid that is carried out of most jet pumps is several times the amount of fluid that is in the jet itself.
Jet pumps can be used to raise water from wells that are deeper than 200 feet (60 meters). In such cases, a centrifugal pump at ground level supplies water for a jet at the bottom of the well. The jet carries well water with it back up to ground level.
Jet pumps are also used in high-vacuum diffusion pumps to create a vacuum in an enclosed area. In high-vacuum diffusion pumps, a high-velocity jet of mercury or oil vapor is sent into the enclosed area. The vapor molecules collide with the molecules of air and force them out the outlet port.
Electromagnetic pumps
are used chiefly to move liquid sodium and liquid potassium, which serve as coolants in nuclear reactors. These pumps consist of electrical conductors and magnetized pipes. The conductors send current through the fluid. This causes the fluid to become an electromagnet. The fluid is then moved by the magnetic attraction and repulsion (pushing away) between the fluid’s magnetic field and the magnetic field of the pipes. The fluid is therefore moved in an electromagnetic pump in much the same way as an armature is moved in an electric motor (see Electric motor ).
Positive displacement pumps
Rotary pumps
are the most widely used positive displacement pumps. They are often used to pump such viscous (sticky) liquids as motor oil, syrup, and paint. There are three main types of rotary pumps. These types are: (1) gear pumps, (2) lobe pumps, and (3) sliding vane pumps.
Gear pumps
consist of two gears that rotate against the walls of a circular housing. The inlet and outlet ports are at opposite sides of the housing, on line with the point where the teeth of the gears are fitted together. Fluid that enters the pump is trapped by the rotating gear teeth, which sweep the fluid along the pump wall to the outlet port.
Lobe pumps
operate in a manner similar to gear pumps. However, instead of gears, lobe pumps are equipped with impellers that have lobes (rounded projections) fitted together. Lobe pumps can discharge large amounts of fluid at low pressure.
Sliding vane pumps
consist of a slotted impeller mounted off-center in a circular housing. Sliding vanes (blades) move in and out of the slots. As the vanes rotate by the inlet port, they sweep up fluid and trap it against the pump wall. The distance between the impeller and the pump wall narrows near the outlet port. As the fluid is carried around to this port, the vanes are pushed in and the fluid is compressed. The pressurized fluid then rushes out the outlet port.
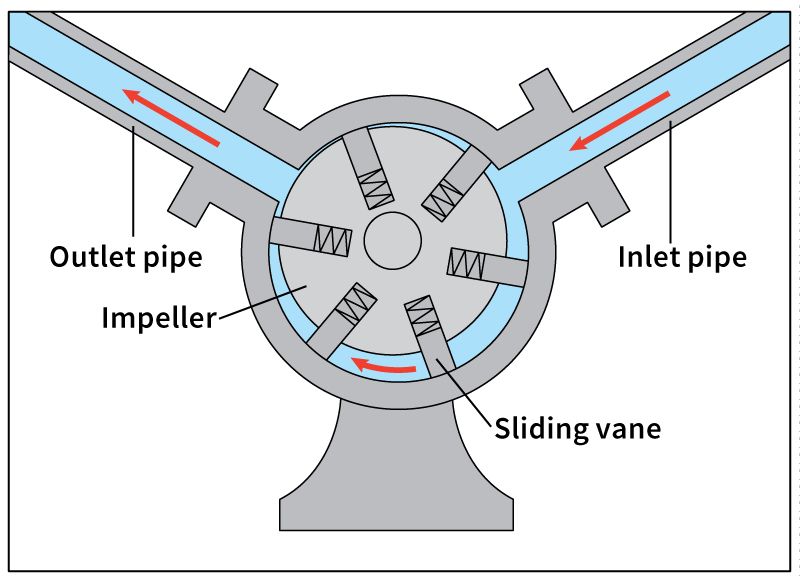
Reciprocating pumps
consist of a piston that moves back and forth within a cylinder. One end of the cylinder has an opening through which the connecting rod of the piston passes. The other end of the cylinder, called the closed end, has an inlet valve or an outlet valve, or both valves, depending on the type of pump. In certain types of reciprocating pumps, the inlet valve or the outlet valve is located on the piston. Common reciprocating pumps include lift pumps, force pumps, and bicycle tire pumps.
Lift pumps
draw water from wells. In a lift pump, the inlet valve is at the closed end of the cylinder and the outlet valve is on the piston. As the piston is raised, water is drawn up through the inlet valve. As the piston is lowered, the inlet valve closes, forcing water through the outlet valve and up above the piston. As the piston is raised again, the outlet valve closes and the water is lifted to an opening, where it leaves the pump. At the same time, more water is drawn through the inlet valve.
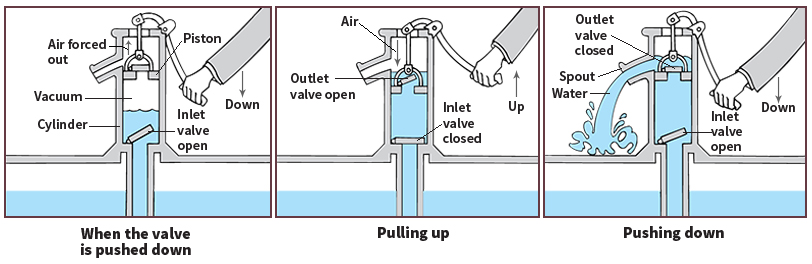
It is theoretically possible for a lift pump to raise water in a well almost 34 feet (10.4 meters) at sea level. But because of leakage and resistance, a lift pump cannot raise water that is deeper than about 25 feet (7.6 meters).
Force pumps
are similar to lift pumps. However, in force pumps, both the inlet valve and the outlet valve are at the closed end of the cylinder. As the piston moves away from the closed end, fluid enters the cylinder. When the piston moves toward the closed end, the fluid is forced out the outlet valve.
Bicycle tire pumps
vary in the number and location of the valves they have and in the way air enters the cylinder. Some simple bicycle tire pumps have the inlet valve on the piston and the outlet valve at the closed end of the cylinder. Air enters the pump near the point where the connecting rod passes through the cylinder. As the rod is pulled out, air passes through the piston and fills the areas between the piston and the outlet valve. As the rod is pushed in, the inlet valve closes and the piston forces air through the outlet valve of the pump.
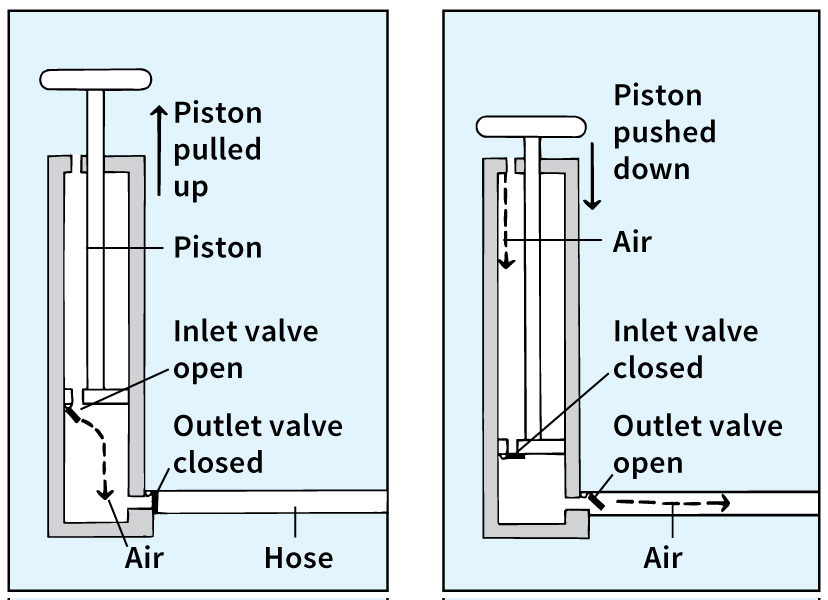
History
Pumping devices have been an important means of moving fluids for thousands of years. The ancient Egyptians used water wheels with buckets mounted on them to move water for irrigation. The buckets scooped water from wells and streams and deposited it in ditches that carried it to fields. In the 200’s B.C., Ctesibius, a Greek inventor, made a reciprocating pump for pumping water. About the same time, Archimedes, a Greek mathematician, invented a screw pump that was made up of a screw rotating in a cylinder (see Archimedean screw ). The ancient Egyptians used this type of pump to drain and irrigate the Nile Valley.
True centrifugal pumps were not developed until the late 1600’s, when Denis Papin, a French-born inventor, made one with straight vanes. The British inventor John G. Appold introduced a curved-vane centrifugal pump in 1851. Axial-flow compressors were first used on turbojet engines in the 1940’s.