Rubber is one of our most interesting and most important raw materials. Natural rubber comes from the juice of a tree. Synthetic rubber is manufactured from chemicals.
Rubber is especially useful for several reasons. It holds air, keeps out moisture, and does not readily conduct electricity. But its chief importance to us is that it is elastic. When you stretch a rubber band and let it go, its elasticity makes it quickly spring back to its original shape. A rubber ball bounces because of this same springiness. Your rubber heels absorb shock when you walk because they have elasticity.
We depend so much on rubber that it would be almost impossible to get along without it. This is not the case with most other materials. If we lack one material, we can usually substitute another. A house can be built using such materials as wood, brick, stone, concrete, glass, or metal. Clothes can be made of cotton, silk, wool, or other fibers.
But what about the tires of an automobile, truck, or bus? It is hard to imagine making them of anything but rubber. Only rubber is elastic, airtight, water-resistant, shock-absorbing, and long-wearing.
Uses of rubber
About three-fifths of the rubber used in the United States goes into tires and tubes. These are used on automobiles, airplanes, buses, trucks, tractors, and construction machinery. Cars have many other rubber parts, such as belts and hoses. Many trucks and buses even have springs made of rubber instead of steel. About one-tenth of the rubber used in the United States is used for mechanical products such as gaskets, sealing devices, belting, and printing rollers.
Manufacturers use rubber to make waterproof aprons, boots, raincoats, gloves, and hats, and to give elasticity to other types of clothing and household fabrics. Hard-rubber goods include hair combs and automobile storage-battery cases. Doctors use rubber hot-water bottles, ice bags, syringes, elastic tapes, and surgeon’s gloves. Hearing aids, oxygen tents, and many other pieces of equipment have rubber parts.
Swimmers wear rubber bathing suits and caps, goggles, and ear stoppers, and sunbathe on rubber rafts. Many sports are played with rubber balls that range in size from small golfballs to large beach balls. Other rubber products include thread, bottle stoppers, toys, jar rings, elastic bands, and rubber-based paints.
Air pockets in sponge and foam rubbers make them springy. Manufacturers use such kinds of rubber for cushions, mattresses, pillows, and upholstery padding. They are also used as an insulating material. For example, some shoes have a layer of foam rubber next to the leather to keep out the cold.
Rubber cement can be used to hold pieces of paper together, but the pieces can be pulled apart easily. This cement is made of a solution of raw natural rubber in a chemical solvent. The solvent evaporates, and the sticky rubber holds the pieces of paper together.
The development of rubber
First uses.
When the early European explorers came to Central and South America, they saw the Indians playing with bouncing balls made of rubber. The explorers learned that the Indians made “waterproof” shoes from latex, the milky white juice of the rubber tree. They spread the latex on their feet and let it dry. The Indians also made waterproof bottles by smoothing latex on a bottle-shaped clay mold. They dried the latex over a fire and then washed out the clay.
The South American Indians called the rubber tree cahuchu, which means weeping wood. The drops of latex oozing from the bark made them think of big white tears. A French explorer, Charles Marie de La Condamine, gathered samples of hardened latex in Peru in 1735, and took them back to France. The French called this new material caoutchouc, the French pronunciation of the Indian name cahuchu. Variations of the French spelling are used as the word for rubber in most European countries. In 1770, the English chemist Joseph Priestley discovered that the material could be used as an eraser to rub out pencil marks. From this use, we get the name rubber.
The rubber industry begins.
By the late 1700’s, scientists had found that hardened latex dissolved in turpentine made a waterproofing liquid for cloth. In the early 1820’s, the English inventor Thomas Hancock built a machine to knead scraps of rubber into a solid mass. His inventions and experiments led to the development of present-day rubber processing.
In 1823, Charles Macintosh, a Scottish chemist, began manufacturing the “mackintosh” raincoats that became world famous. He made them with a layer of rubber between two layers of cloth. Manufacturers in Europe and the United States began to make rubber products, including elastic bands, raincoats, hoses, tubes, and shoes.
Discovery of vulcanization.
Early rubber products became sticky in hot weather, and stiff and brittle in cold weather. In 1839, Charles Goodyear, a Connecticut inventor, discovered a way to make rubber stronger and give it resistance to heat and cold. Goodyear accidentally spilled a sulfur-rubber mixture containing other ingredients on a hot stove while conducting an experiment. The rubber compound was “cured” by the heat, and stayed tough and firm in heat and cold. The process of heating sulfur-rubber mixtures became known as vulcanization, after Vulcan, the Roman god of fire. With vulcanized rubber, manufacturers could make dependable products, and the rubber industry grew rapidly. Vulcanized rubber was elastic, airtight, and watertight. It could be used to make tight seals between the moving parts of machinery.
The first plantations.
At first, manufacturers used only wild rubber. Most of it came from the Amazon Valley of Brazil, although some was from latex-bearing vines in Africa. In 1876, a botanist brought rubber tree seeds to England. Some of the seeds sprouted and were taken to Ceylon (now Sri Lanka) and Malaya for replanting on plantations. Almost all the plantation trees in the Far East come from these seedlings. The British, Dutch, and French developed plantations in Indonesia, Thailand, Indochina, and other countries of the Far East.
The invention of the automobile in the late 1800’s created a tremendous demand for rubber. By 1914, the yearly production of plantation rubber exceeded that of wild rubber. Later, plantations were established in Africa, South and Central America, and the Philippines.
Development of synthetic rubbers.
The importance of rubber in wartime became obvious during World War I. Armies needed rubber-tired vehicles to carry troops and supplies. The Germans were cut off from their natural-rubber supplies by the Allied blockade. They began to make synthetic rubber, but it did not work well. Experiments in producing synthetic rubber continued in the 1920’s, chiefly by scientists in Germany and the United States.
When World War II began in 1939, Germany was manufacturing two chief types of synthetic rubber: (1) Buna S, made from butadiene (a gas) and styrene (a liquid made from coal tar and petroleum); and (2) Buna N, made from butadiene and acrylonitrile (a liquid obtained from acetylene and hydrocyanic acid). Before 1939, experimenters in the United States made small amounts of several types of synthetic rubber. However, the estimated cost of making these synthetic rubbers was much higher than that of natural rubber.
In 1942, the Japanese captured the rubber-growing lands of the Far East. This cut off nine-tenths of the natural-rubber supply to the United States. Almost overnight, the United States developed a synthetic-rubber industry.
The world now uses more synthetic rubber than natural rubber. This is because synthetic rubber has a greater variety of uses and can be produced cheaply enough to compete with the cost of natural rubber. But the rising cost of petroleum, used in making synthetic rubber, has slowed the growth of synthetic rubber production. Synthetic rubber production has also been affected by the increasing popularity of long-lasting radial tires. These tires require more natural rubber than does another kind of tire, called a bias tire (see Tire).
The chemistry of rubber
In 1826, the English chemist and physicist Michael Faraday discovered that rubber is a hydrocarbon—that is, it consists of the chemical elements hydrogen and carbon. In 1860, another English scientist, Greville Williams, heated some rubber and obtained a liquid he called isoprene. Each isoprene molecule contains five carbon atoms and eight hydrogen atoms. In natural rubber, thousands of tiny isoprene molecules link up into a chain to form large molecules of rubber. Chemists call these molecular chains polymers. They call the single molecules, such as isoprene, monomers.
The particular chainlike structure of the rubber polymer explains why rubber is elastic. Polymer molecules of unstretched rubber fold back on themselves somewhat like irregular coils. Vulcanization attaches the polymer coils to each other. Stretching the rubber straightens the chain of folded molecules. Releasing the rubber lets the chain return to its coiled position.
For years, scientists tried to duplicate the true rubber polymer with molecules of the isoprene monomer. They finally built the first successful synthetic rubbers from the monomers of other hydrocarbons, including butadiene, styrene, and isobutylene.
The rubber industry
Production and uses.
More than 80 percent of the world’s natural rubber grows on plantations in the Far East, chiefly in Thailand, Indonesia, and Vietnam. Other Far Eastern countries that produce natural rubber include Cambodia, China, Malaysia, Myanmar, and the Philippines. India and Sri Lanka grow about 7 percent of the world’s supply of natural rubber, and Africa grows about 5 percent. Most of the rest comes from Latin America. The world’s annual production of natural rubber is about 16 million tons (14.5 million metric tons). Asian countries, especially China, use most of the world’s natural rubber.
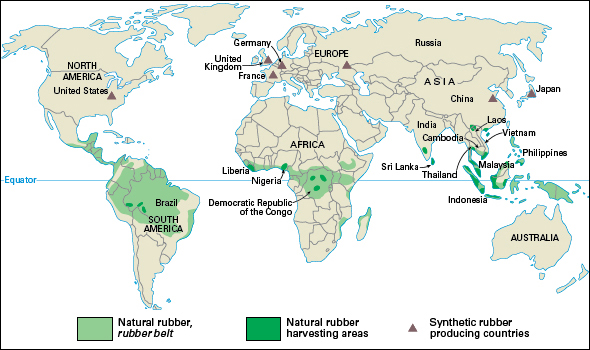
The world’s synthetic rubber production is also about 16 million tons (14.5 million metric tons) a year. China is the world’s leading synthetic rubber producer and consumer. Other important synthetic rubber producers include France, Germany, Japan, Russia, Germany, South Korea, Taiwan, and the United States.
Leading rubber manufacturers
usually grow part of their natural rubber on their own plantations, and produce synthetic rubber in their own plants. These rubber companies make varied products such as tires, mechanical goods, industrial products, shoe materials and footwear, aircraft parts, and rubberized textiles. Some companies also produce, for their own use and for sale to other firms, raw materials used to make synthetic rubber. More rubber is used in the manufacture of tires than for any other purpose. The number of tire manufacturers decreased during the 1980’s as large companies bought smaller companies. Today, the largest tire manufacturers are the Bridgestone Corporation of Japan, the Goodyear Tire & Rubber Company of the United States, and the Michelin Company of France.
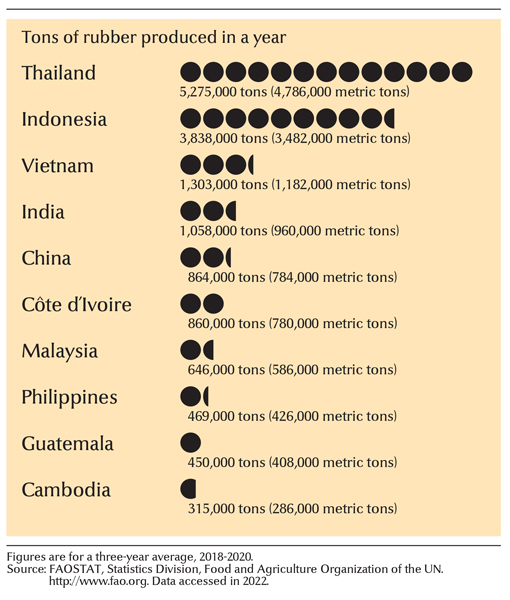
Research
in rubber is directed mainly toward making better synthetic rubbers to provide improved rubber products for home, automotive, and industrial use. In addition, many unusual types of rubber are required in the age of nuclear energy and space travel. As new planes and missiles fly higher and faster, they require rubber parts that can withstand temperatures from –120 to 700 °F (–84 to 370 °C). Chemists hope to develop rubbers that will increase protection against harmful radiation in nuclear power plants.
United States scientists are studying the possible use of the guayule plant as an inexpensive source of natural rubber. This plant could reduce the nation’s dependence on foreign sources of natural rubber and on synthetic rubbers made from petroleum.
Natural rubber
Latex is found in a wide variety of trees and other types of plants. You can see latex oozing from the broken stem of a dandelion or from a cut branch of goldenrod. Scientists are not sure of its use to the plant. Some scientists believe that latex acts as a kind of protective substance when a plant has been wounded.
Chemical analysis shows that about 30 to 35 percent of latex consists of pure rubber. Water makes up another 60 to 65 percent. Latex holds little globules (particles) of rubber in the same way that milk holds butterfat. Latex spoils easily, and must be processed into crude rubber as soon as possible after tapping. This is done by separating the natural rubber in the latex from water and other materials. About 99 percent of all natural rubber comes from the latex of the Hevea brasiliensis. This is the tree that we call the rubber tree.
The rubber tree.
The hevea tree grows best in hot, moist climates in acid, well-drained soils. The finest rubber-growing regions lie within a rubber belt that extends about 700 miles (1,100 kilometers) on each side of the equator. Almost all natural rubber comes from huge plantations of rubber trees in the Far East.
The rubber tree cultivated on plantations grows straight and slender, about 60 to 70 feet (18 to 21 meters) tall. It has smooth, light-colored bark and shiny, dark leaves. When its pale yellow blossoms fade, seed pods grow in their place. Each pod contains three brownish, speckled seeds about 1 inch (2.5 centimeters) long. The latex containing the rubber flows through a series of tubes in the tree’s cambium layer, the layer between the wood and bark. When this layer is pierced, the milky white latex oozes out. By grafting and breeding, botanists have developed trees that produce over 10 times as much natural rubber as the wild hevea.
Rubber has also been collected from landolphia vines that grow in Africa. In Mexico, guayule bushes have been cultivated for their rubber, but they produce only a small amount. In Brazil, a small amount of rubber comes from wild hevea trees. Other rubber-bearing trees include the manihot tree, also found in Brazil, and the trees of the genus Castilloa found in Central America, Colombia, and Ecuador.
Tapping the tree.
Rubber plantations employ workers called tappers who collect latex from the trees. A tapper cuts a narrow groove in the bark of a tree about 4 feet (1.2 meters) above the ground. The groove slants diagonally downward about halfway around the trunk. At the bottom of the cut, the tapper attaches a U-shaped metal spout, and below the spout, a small cup. Latex oozes from the cut and flows down the groove through the spout into the cup. Tappers collect about a teacupful of latex at each tree. The latex is then transported to the factory for processing into liquid latex or dry rubber.
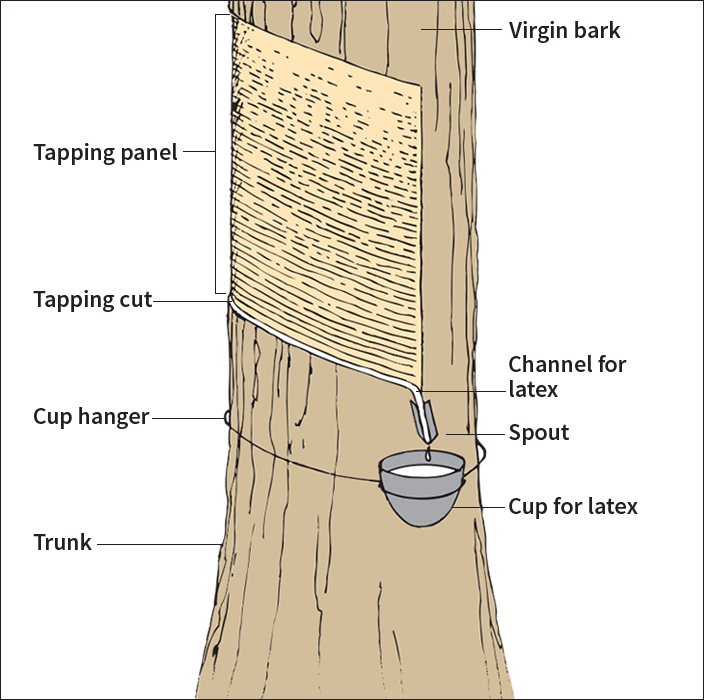
Some plantations tap the trees every other day. Other plantations tap every day for 15 days, and then allow the trees to “rest” for 15 days. On each tapping, the worker slices off a thin shaving of bark from the bottom edge of the groove near the cambium layer. The tapper does not cut into the cambium layer of the tree, because deep cuts that penetrate the wood harm the tree. After three or four years, the groove reaches the ground, and the tapper cuts the bark on the opposite side of the trunk. By the time the second groove reaches the ground, the bark has grown back on the first groove, and it can be tapped again.
Workers begin to tap rubber trees about five to seven years after planting. But younger trees do not give as much rubber as they do about the 10th year, when they are fully grown. Rubber trees yield their full capacity of latex for about 25 to 30 years. About 100 trees grow on 1 acre (0.4 hectare), and each full-grown tree produces from 1 to 4 gallons (4 to 15 liters) of latex a year. One acre of trees on a large, well-developed plantation may yield about 1,800 pounds (816 kilograms) of dry crude rubber a year.
Separating the latex.
Most plantations make crude rubber from latex by coagulation. Tappers pour latex from their collecting pails into tanks and add an equal amount of water. They strain the diluted latex through sieves to remove dirt, bark, and twigs. Formic acid is then added to the strained latex to make it coagulate, or form solid particles. The rubber particles rise to the surface and form a curdlike mass of crude rubber.
Processing crude rubber.
Workers feed the crude rubber through rollers that squeeze out the water and form it into a sheet. Crumb rubber is produced by special machines that chop or shred the sheets into fine, wet crumbs. The crumb rubber is dried in hot air tunnels and then compressed into 75-pound (34-kilogram) bales for shipment to market.
Ribbed smoke sheet is made by putting crude rubber through rollers that give the sheets a ribbed appearance. The sheets are hung to dry for several days in a hot smokehouse. The smoke turns the rubber sheets brown and kills mold and bacteria that would damage them. The dried sheets are pressed into bales for shipment.
Crepe rubber is formed by passing the curdlike mass through rollers that roughen and crinkle the sheets so that they look like thick crepe paper. The rubber is constantly washed while being rolled. The sheets hang in heating rooms to dry. Workers bale the pale, crinkled sheets for shipment.
Processing latex.
Sometimes, all the latex collected on plantations is not coagulated. Workers place part of the fresh latex in machines called separators that remove part of the water from the latex. Ammonia or another preservative keeps the latex from coagulating and prevents spoiling. The preserved liquid latex is sent to market in drums or tanks. Rubber manufacturers use latex to make articles such as surgeon’s gloves, foam-backed carpeting, tubing, and elastic thread.
Synthetic rubber
Rubberlike materials made from chemicals were called synthetic rubbers because they were intended as substitutes for natural rubber. Chemists use the word elastomer for any substance, including rubber, that stretches easily to several times its length, and returns to its original shape.
Manufacturers group synthetic rubbers into two classes: general-purpose and special-purpose. General-purpose rubbers have many uses. Special-purpose rubbers have special properties such as resistance to oils and fuels, air, and extreme temperatures, that make them better than natural rubber for certain uses.
General-purpose synthetic rubbers.
The most important general-purpose rubber is styrene-butadiene rubber (SBR). It usually consists of about three parts butadiene and one part styrene. Butadiene, a gas, is made from petroleum. It must be compressed or condensed into liquid form for use in making rubber. Styrene is a liquid made from coal tar or petroleum.
Styrene and butadiene usually come to the synthetic-rubber plant in tank cars or tank trucks. Sometimes they are piped in directly from the plants that produce them. Correct amounts of styrene and butadiene are pumped into a large tank containing a hydrocarbon solution. An organometallic catalyst, which contains metal atoms bonded to carbon atoms, causes butadiene to react with styrene to form SBR (see Catalysis). The rubber is then recovered by adding the solution to hot water and removing the solvent with steam. The crumbs of rubber are then filtered from the water. After drying, the rubber is usually pressed into large bales.
SDR can also be prepared using styrene and butadiene in a mixture of soap and water. The mixture is heated or cooled depending on the type of SBR being made. A catalyst causes the styrene and butadiene to combine with each other. Gradually, with stirring, the ingredients change to a milky white fluid, also called latex.
Workers pump the latex into another tank where antioxidants are added to prevent the rubber from decaying. The latex is sent to a third tank containing acids and salts. The salts and acids coagulate the latex. The rubber forms into lumps that float on top of the liquid. Washing the rubber lumps removes extra chemicals. The rubber may then be packed as loose crumbs or pressed into bales of dry rubber.
Special-purpose rubbers.
Contact with gasoline, oils, sunlight, and air harms natural rubber. Special-purpose synthetic rubbers resist these “enemies” better than natural rubber and SBR do. Also, some of these special-purpose rubbers have greater resistance to heat and cold. They cost more than natural rubber or SBR, but their special properties make them worth the extra cost. Special-purpose rubbers include butyl rubber, neoprene rubber, and polyurethane rubbers.
Manufacturing rubber products
Manufacturers obtain bales of dry rubber from plantations and from synthetic-rubber manufacturing plants. Latex comes to them in big tanks on ships and in tank cars. Manufacturers usually process natural and synthetic rubber in much the same way, although latex requires different steps.
Plasticization
involves only dry rubber. It is a series of processes that makes dry rubber softer and easier to mold.
Workers first slice the bales into small pieces of rubber that they can handle easily. The lower grades of natural rubber receive a thorough washing in a wringerlike machine called a wash mill. Then the rubber slices are fed into mixing mills and other machines that plasticize, or soften, them into a doughlike mass. Manufacturers plasticize the rubber faster by heating it and adding materials called plasticizers and softeners.
Compounding and mixing.
Compounding means adding carefully measured amounts of various ingredients to plasticized rubber and to latex. The compounding “recipe” helps control the elasticity, strength, and other properties of the final product. Sulfur is commonly added to bring about vulcanization, a process that takes place later in rubber manufacturing. Other ingredients used include accelerators, which speed vulcanization; fillers, which increase the volume and strength of the rubber; and antioxidants, which slow down the rate at which the rubber wears out.
Shaping.
Manufacturers use several methods to shape rubber into final products. These include (1) calendering, (2) extrusion, (3) molding, and (4) dipping.
Calendering
means rolling rubber into sheets. It is done on a machine that has two to five rolls. The rubber passes between the rolls to form sheets. Workers cut the sheets into various sizes and patterns, or stack the sheets in layers to make many products. These products include rubber flooring, toys, bed sheets, baby pants, and mechanical goods, such as wrapping tapes, washers, rings, and disks.
Extrusion
is the final step in the processing of some rubber products. The word extrude means to push out. Tube machines push soft rubber through a hole, much as toothpaste is squeezed from a tube. Extruded products include hoses, inner tubes, and rubber strips used on refrigerators and automobile windshields.
Molding
produces shoe soles and heels, rubber tires, hot-water bottles, mattresses, hard-rubber articles, and industrial products, such as gaskets and fittings. Workers prepare pieces of rubber in the approximate size and shape of the finished product. They put the pieces in molds shaped to form the product. Many products are molded and vulcanized at the same time.
Dipping
is used only to make products from liquid latex. Products made by dipping include rubber gloves and toy balloons. Workers dip molds, usually made of metal, glass, or ceramic materials, into tanks of latex. They drain the excess latex and dry the mold at low temperatures. By repeating this process, they build up several layers on the mold.
Vulcanization
is usually the last step in preparing a final product. It gives strength, hardness, and elasticity to rubber by treating it with heat and vulcanizing agents, such as sulfur. During vulcanization, the heat causes the sulfur to combine with the rubber and cure it. This makes the rubber stronger and more durable. Generally, the more sulfur that is added, the firmer the vulcanized compound will be. Vulcanization may take from a few minutes to several hours.
Manufacturers vulcanize and shape molded products at the same time by heating the molds under pressure. They vulcanize extruded and sheet products on pans in hot-air or steam chambers. Dipped products are vulcanized in hot water, hot air, or open steam while still on the molds. Foam products in their molds are vulcanized in steam chambers or in boiling water.
Sponge rubber
may be made either from dry rubber or from latex. Blowing produces one type of sponge rubber from dry rubber. During vulcanization, the chemicals that have been added turn to gas and “blow” tiny bubbles of air in the rubber compound. When the rubber gels, or sets, in the mold, the bubbles are trapped in it. Blown sponge rubber may be either hard or soft.
Foam rubber is a type of sponge rubber made by whipping air into latex, much as a cook whips air into egg whites. Vulcanization takes place after the foam gels in a mold. Foam rubber has millions of tiny cells filled with air. Some types may be nine-tenths air and only one-tenth rubber. Foam rubber is used for upholstery and foam strips for surgical use.