Silk is a strong, shiny fiber used to make cloth. Silk has a natural beauty that few other fibers can equal. It is often called the queen of fibers. Silk fiber is made from the cocoons of caterpillars called silkworms. Many other animals, including spiders and lacewings, spin silk threads. But their silk cannot economically be made into cloth.
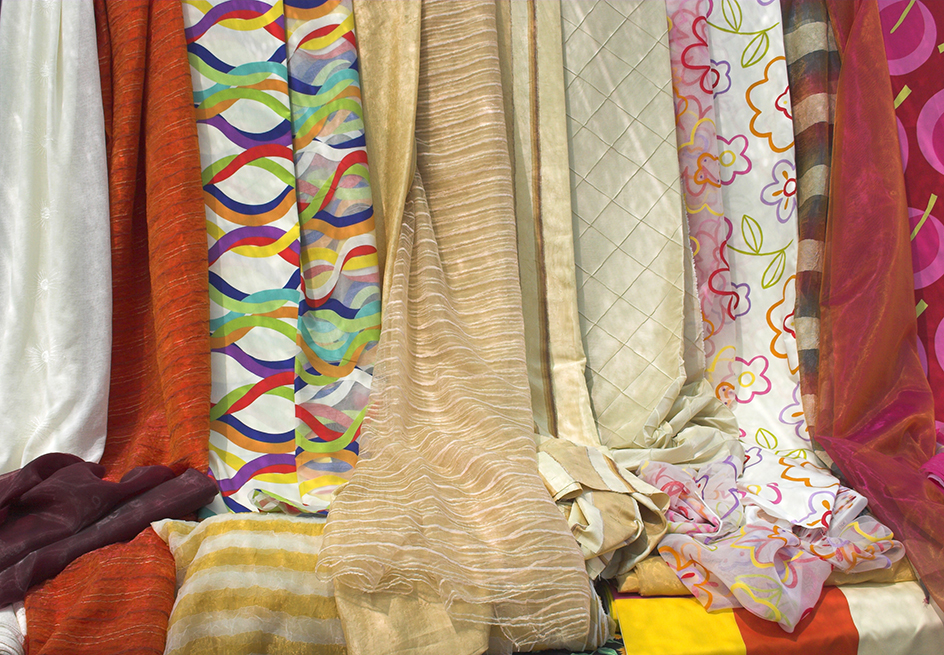
Silk is the strongest natural fiber. A thread of silk is stronger than the same diameter thread of some kinds of steel. Silk is also highly elastic. It can be stretched and will still return to its original shape. Silk garments are light in weight. They are also warmer than cotton , linen , or rayon clothing. Dyed silk cloth has a deeper, richer appearance than most other dyed fabrics. Silk fabric can be ironed easily. It also resists wrinkling.
Silk is used widely in making clothing . It is also used in upholstery and curtain materials, especially in mixed fabrics.
China produces more raw silk than any other country. Japan ranks second. Other leading silk producers include Brazil, India, South Korea, Thailand, and Uzbekistan. China is the world’s leading manufacturer of silk products. Italy is noted for its fine patterned-silk fabrics.
Sources of silk
Silk fiber is made from the cocoons of caterpillars called silkworms . Many other animals, including spiders and lacewings, spin silk threads. Scientists have genetically engineered goats that produce spider silk proteins in their milk. The proteins can be filtered out and used to manufacture silk fibers. But spider silk does not provide a major source of silk cloth.
Cultivated silk
is spun by silkworms. The worms are raised on silk farms. Almost all commercial silk is cultivated. Most high quality cultivated silk is produced by the caterpillars, or larvae, of a silkmoth called Bombyx mori. The last part of the moth’s name comes from the scientific name of the mulberry tree, on which it feeds.
The silkmoth is a rather large white moth, with black-lined wings. From wing tip to wing tip, the moth measures more than 2 inches (5 centimeters). Its body is short and thick. Its legs are stout.
Wild silk,
called tussah, comes from silkworms that feed chiefly on oak leaves. These worms grow wild, mainly in China and India. Tussah’s natural color is tan or brown. The silk is difficult to bleach. It is less shiny than cultivated silk. Tussah is used as a filling in fabrics. It is often blended with other fibers.
Raising silkworms
The raising of silkworms requires care and patience. Silk farmers raise the silkworms under carefully controlled temperatures. They protect them from flies and diseases that may destroy the silkworms.
Production of silkworms.
In early summer, a female silkworm lays from 300 to 500 eggs. She deposits them on special strips of paper provided by the silk farmer. The moth dies soon after she lays her eggs. The eggs undergo many tests to make sure they contain perfect, disease-free worms. Then they are put in cold storage. Early the next spring, the silk farmer puts the eggs in an incubator. This device keeps the eggs at a suitable temperature for hatching. About 20 days later, the eggs hatch into tiny silkworms.
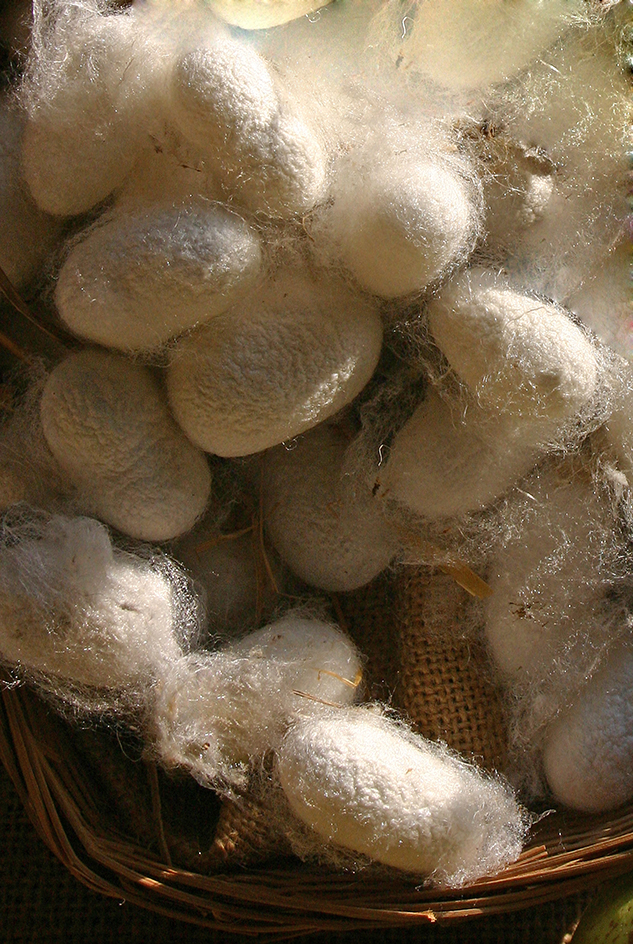
Development of silkworms.
The young silkworms are put on trays that are kept spotlessly clean to prevent disease. At first, the silkworms have enormous appetites. They eat almost continually, night and day. The silk farmer supplies them with fresh mulberry leaves every two or three hours. The worms grow to about 70 times their original size. They shed their skins four times. After four to five weeks, the silkworm is about 3 inches (7.5 centimeters) long and 0.4 inch (1.0 centimeter) thick. It has a head and 13 body segments. The worm has three pairs of true legs. It also usually has five pairs of leglike prolegs farther back on its body.
Spinning the cocoon.
When fully grown, the silkworm stops eating. It is ready to spin its cocoon (outer wrapping). The worm creeps into a tiny wooden compartment containing twigs or stems of straw that the farmer has prepared. The worm spins a net or web to hold itself to a twig or stem. It then forms a cocoon, which is the silk. To do this, it swings its head from side to side in a series of figure-eight movements. Two glands near the silkworm’s lower jaw give off a fluid that hardens into fine silk threads as it hits the air. At the same time, the silkworm gives off a gum called sericin. The sericin cements the two threads of silk together.
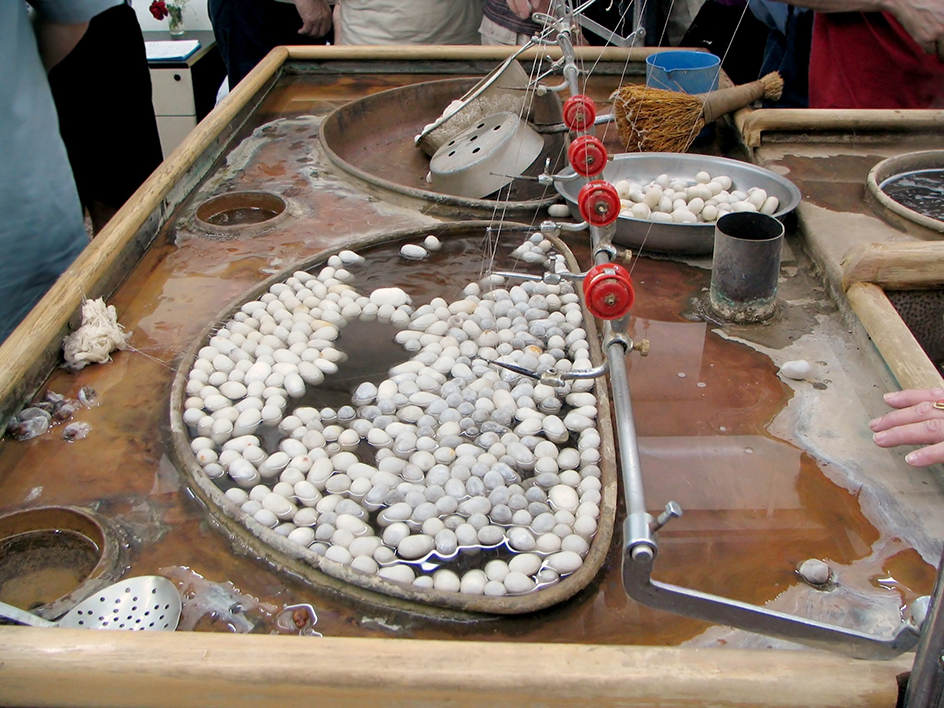
The silkworm spins the silk around and around its body, until all the fluid has been used. After about three days of spinning, the cocoon is completed. The worm then changes into a pupa. The pupa is the third stage of its life cycle. The pupa becomes a moth in about three weeks, thus completing its life cycle. This process of development through several stages is called metamorphosis (see Metamorphosis ).
When a pupa changes into a moth, it bursts the cocoon and breaks the long silk thread into many short ones. For this reason, silk farmers allow only a small percentage of pupae to develop into moths. These moths are kept to lay the next batch of eggs. To save the silk, farmers kill the other pupae before they break their coverings by heating the cocoons in an oven.
Processing silk
Reeling.
After the pupa has been killed, silk workers are ready to reel (unwind) the long delicate threads of the cocoon. This is done in a reeling factory called a filature. The cocoons are soaked in basins of hot water. The water softens the gummy sericin that holds the threads together. As the cocoons bob about in the basin, their filaments (slender threads) are drawn together and pulled by pulleys through a tiny porcelain guide. The guide is much like the eye of a needle.
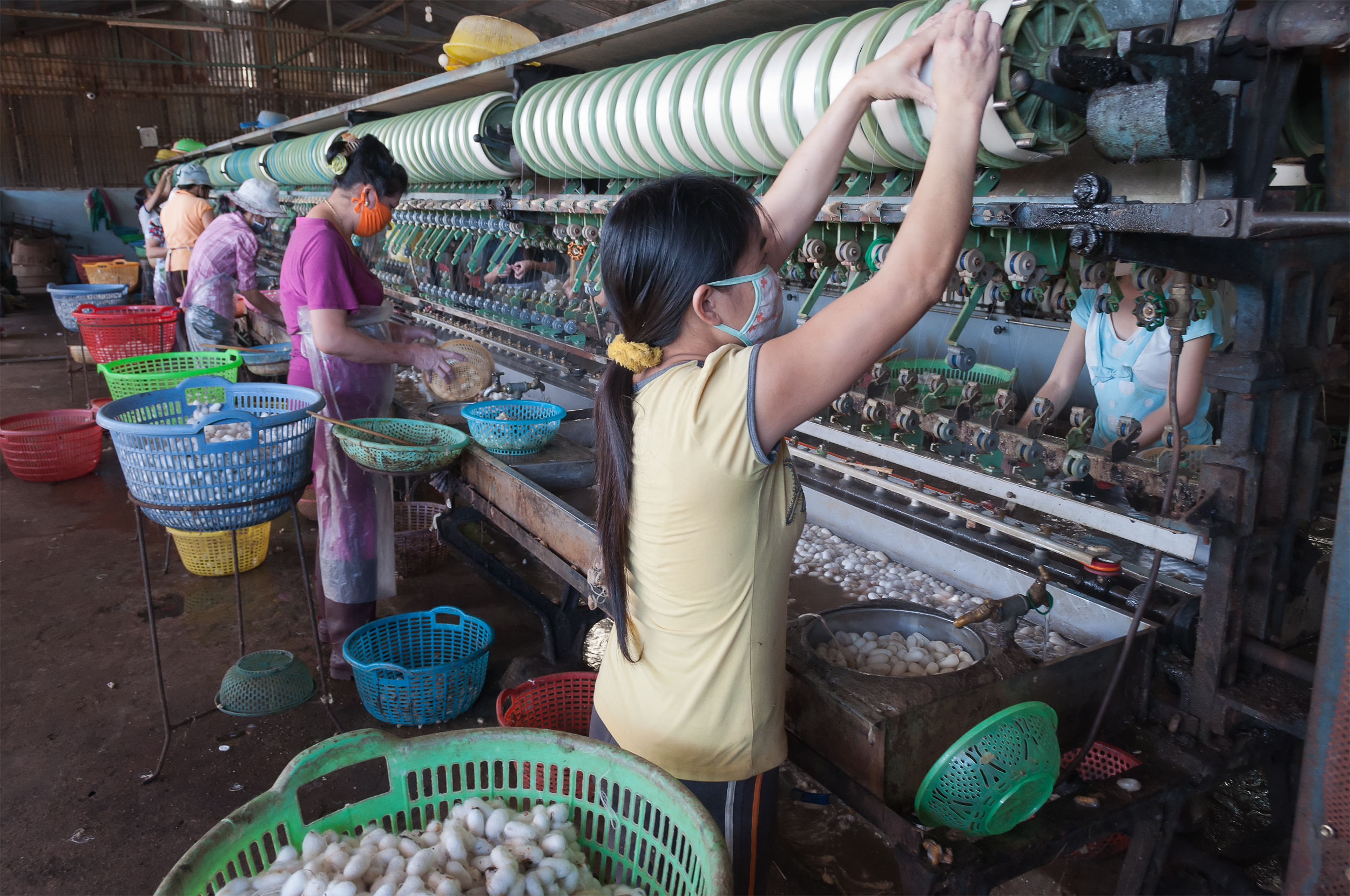
The melted sericin glues several silk filaments into a single thread, which is wound onto a reel. A single filament istoo fine to be wound onto a reel by itself. Instead, threads from several cocoons are reeled at the same time. Later, the silk is removed from the reel and twisted into skeins (small coiled bundles). Thirty skeins are bound into a large bundle called a book. A bale of raw silk ready to be shipped to a mill for weaving contains about 30 books. It weighs about 135 pounds (61 kilograms).
Throwing.
The raw silk is now much stronger than it was when it left the cocoon. But it is still not strong enough to be woven into anything except the sheerest material. It is strengthened by a series of processes called throwing. The term comes from the Anglo-Saxon word thraw (twist). Throwing is increasing the twist or adding strands and twisting them together.
The number of threads thrown together depends on the fabric to be woven. Most raw silk used to make the filling (crosswise threads) is thrown with a certain twist. But much silk used for the warp (lengthwise threads) is reeled in heavier sizes. It need not be thrown.
Boiling off and weighting.
When the silk comes from the throwing machines, there is still sericin on it. In a process called boiling off, workers boil the silk in a solution of hot soap to remove the sericin. The removal of the sericin uncovers the silk’s natural beauty. Boiled-off silk is usually milky-white. The sericin can be removed either before or after weaving, depending on the type of fabric. Boiling off causes the silk to lose about 25 percent of its weight. Before World War II (1939-1945), silk fabrics were often weighted (loaded) with mineral salts to make up for this loss in weight. But heavily weighted silk cracks and tears more easily than pure-dye silk. The United States and many other countries maintain strict trade practices for the silk industry. To be labeled as pure-dye silk in the United States, garments dyed black may be weighted up to 15 percent. Other colors may be weighted up to 10 percent. Garments with more weighting must be labeled as weighted silk.
Dyeing.
Brilliant dyes may be applied to silk yarn before it is woven. This type of dyeing is called skein dyeing. Some silk fabrics are dyed after they are woven. This process is called piece dyeing.
Weaving.
Silk yarns are woven on looms much like those used for cotton and wool. Automatic power looms have replaced hand-weaving methods in almost all countries. Many silk fabrics, including damasks and heavy evening-wear fabrics, are woven on Jacquard looms. Beautiful designs or patterns can be woven on these looms.
Douppioni
are uneven, double silk threads. The double threads come from two silkworms that have nested together and spun a single cocoon around them. In processing, the double threads are not separated. Fabrics woven from douppioni thread have a knotted or twisted appearance. Douppioni are used for the filling in rough weave textiles, such as shantungs.
Spun silk.
Not all silk can be reeled and thrown for weaving. Cocoons broken by the emergence of moths and the beginnings and ends of reeled-off cocoons are known as silk wastes. These fibers are spun into silk yarn. Spun silk yarn is used for the filling in some silk, woolen, and cotton fabrics.
History
Discovery of silk.
No one knows for sure when silk was discovered. According to a Chinese legend, it was discovered about 2700 B.C. in the garden of Emperor Huangdi. The emperor ordered his wife, Xilingshi, to find out what was damaging his mulberry trees.
Xilingshi found white worms eating the mulberry leaves and spinning shiny cocoons. She accidentally dropped a cocoon into hot water. As she played with the cocoon in the water, a delicate, cobwebby tangle separated itself from the cocoon. Xilingshi drew it out and found that one slender thread was unwinding itself from the cocoon. She had discovered silk.
Xilingshi persuaded her husband to give her a grove of mulberry trees. She grew thousands of worms that spun beautiful cocoons. It is said that Xilingshi invented the silk reel, which joined these fine filaments into a thread thick and strong enough for weaving. Some stories also credit her with inventing the first silk loom.
No one knows how much, if any, of this story is true. But historians do know that the Chinese were among the first people to use silk. In addition, China became the world’s first major silk supplier. It remained so for hundreds of years.
Silk making spreads.
China carried on a profitable silk trade with European nations in the days of the Han dynasty (206 B.C. to A.D. 220). Traders from ancient Persia (now Iran) bought richly colored silks from Chinese merchants. Camel caravans blazed routes across Asia (see Silk Road ). The caravans transported silk from China to Damascus, the marketplace at which Asia and Europe met. From Damascus, silk was taken to the Roman Empire , where there were riches to exchange for it.
As early as the 300’s B.C., Europeans heard rumors of the strange worm that spun silk threads. But no one in Europe saw the worm until about A.D. 550. At that time, Persia controlled all silk that came out of China. Persians sold it at fabulously high prices.
The Roman, or Byzantine, emperor Justinian I objected to paying high prices to the Persians. In about 550, he tried unsuccessfully to find a trade route from Constantinople (now Istanbul) to China that would bypass Persia. He later sent two monks to China as spies. Risking death, the monks smuggled out silkworm eggs and mulberry seeds in hollow bamboo canes. This adventure ended the Chinese and Persian silk monopolies.
During the next few hundred years, various peoples learned how to raise silkworms and take silk from the cocoons. The Muslims brought silkworms to Spain and Sicily in the 800’s and 900’s. By the 1200’s, Italy had become the silk center of Europe. Silk weaving began in France in the 1500’s. The French soon rivaled the Italians as silk manufacturers. Silk weaving became an important industry in England after a large number of skilled Flemish weavers entered the country in the late 1500’s. The first silk factory in the United States was built in Mansfield, Connecticut, in 1810.
Silk making today.
Before World War II (1939-1945), the hosiery industry was the biggest user of raw silk. Today, most stockings are made of nylon. There once was also a demand for silk lingerie and silk ribbons. Today, these products are usually made of synthetic fibers (see Synthetics ). Most silk is used in making clothing, curtains, and upholstery. It has also been used with other natural and synthetic fibers to achieve new effects in fabrics. In the United States, the Federal Trade Commission requires that the exact fiber composition be stated on a label attached to such a fabric.