Wind tunnel is a ground-based testing facility used to study the effects of wind, or airflow, on aircraft and other vehicles and structures. Wind tunnels are built in many shapes and for different purposes. Some of them are very large and can test full-sized experimental aircraft. But most wind tunnels test scaled-down models.
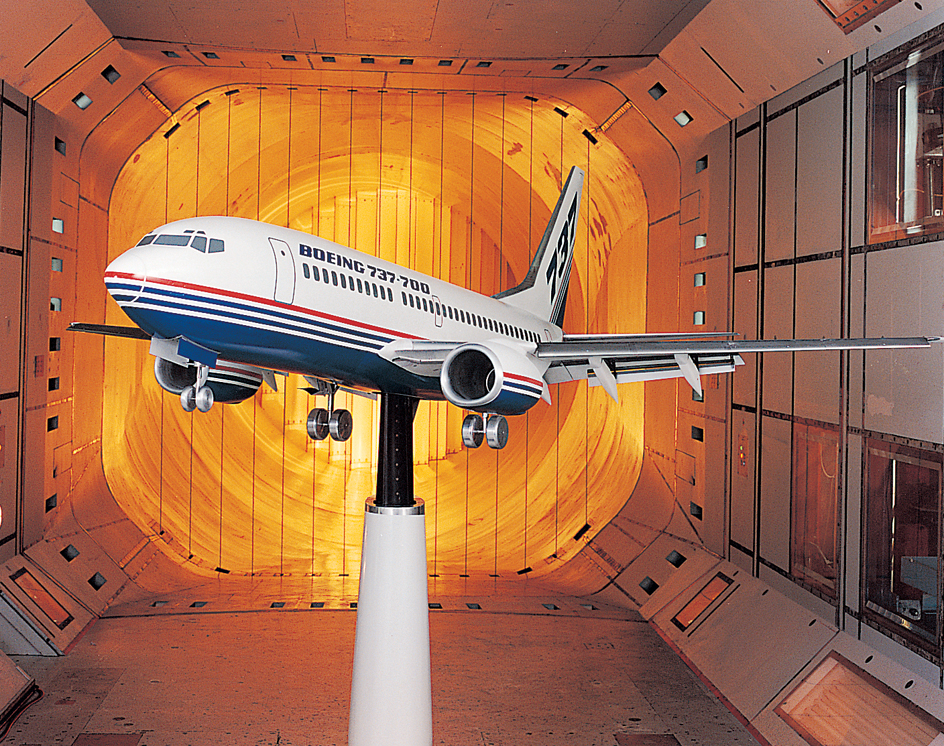
Most wind tunnels have a segment called the test section through which a stream of air is blown at an object at a uniform speed. Air pressure and temperature can be controlled as well. The air is generally blown by electric fans, but other devices, such as pressurized tanks, may be used. A large nozzle in front of the test section accelerates the air to the desired speed. After the wind passes through the test section, a duct called a diffuser slows down the airflow. The vehicle or structure being tested is secured by supports that extend from the ground or from behind the object. The supports are fastened to measuring devices outside the test section that record the force of the airflow on the vehicle or structure. Instruments also can measure surface pressure at many places on the object.
Wind tunnels in which the air speed is close to the speed of sound—that is, about 760 miles (1,225 kilometers) per hour—are called transonic tunnels. In subsonic tunnels, the air travels slower than the speed of sound. Wind tunnels in which air travels faster than the speed of sound are supersonic tunnels. In hypersonic tunnels, air speeds are at least five times as fast as sound.
Highly compressed air or other gases may be blown through wind tunnels to simulate various flight conditions. In some wind tunnels, very high or low temperatures can be achieved, enabling experts to study such subjects as aircraft icing and automobile performance in arctic or tropical climates.